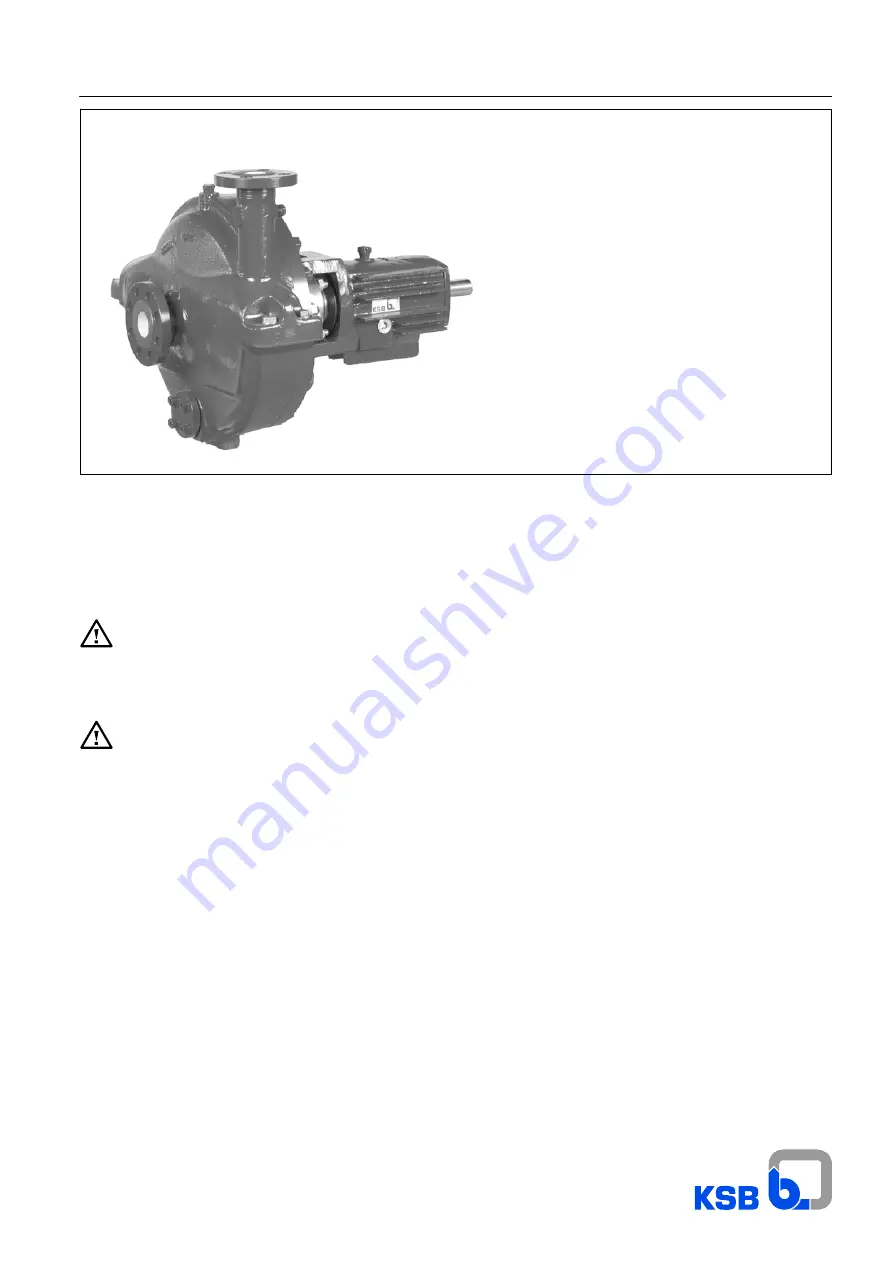
Operating instructions
1316.8014/2-10 G3
RPH
RPH process pump
to API 610, 10th edition and DIN ISO 13709
and Directive 94/9/EC
Standard bearing assemblies B 02 to B 06
Tandem bearing assemblies B 02 to B 06
cooled/uncooled
Mechanical seal
Made by KSB
Works No.:
__________________________________
Type series:
__________________________________
These operating instructions contain fundamental
information and precautionary notes. Please read
the manual thoroughly prior to installation of unit,
connection to the power supply and commissioning. It is
imperative to comply with all other operating instructions
referring to components of this unit.
This manual shall always be kept close to the unit’s
location of operation or directly on the pump set.