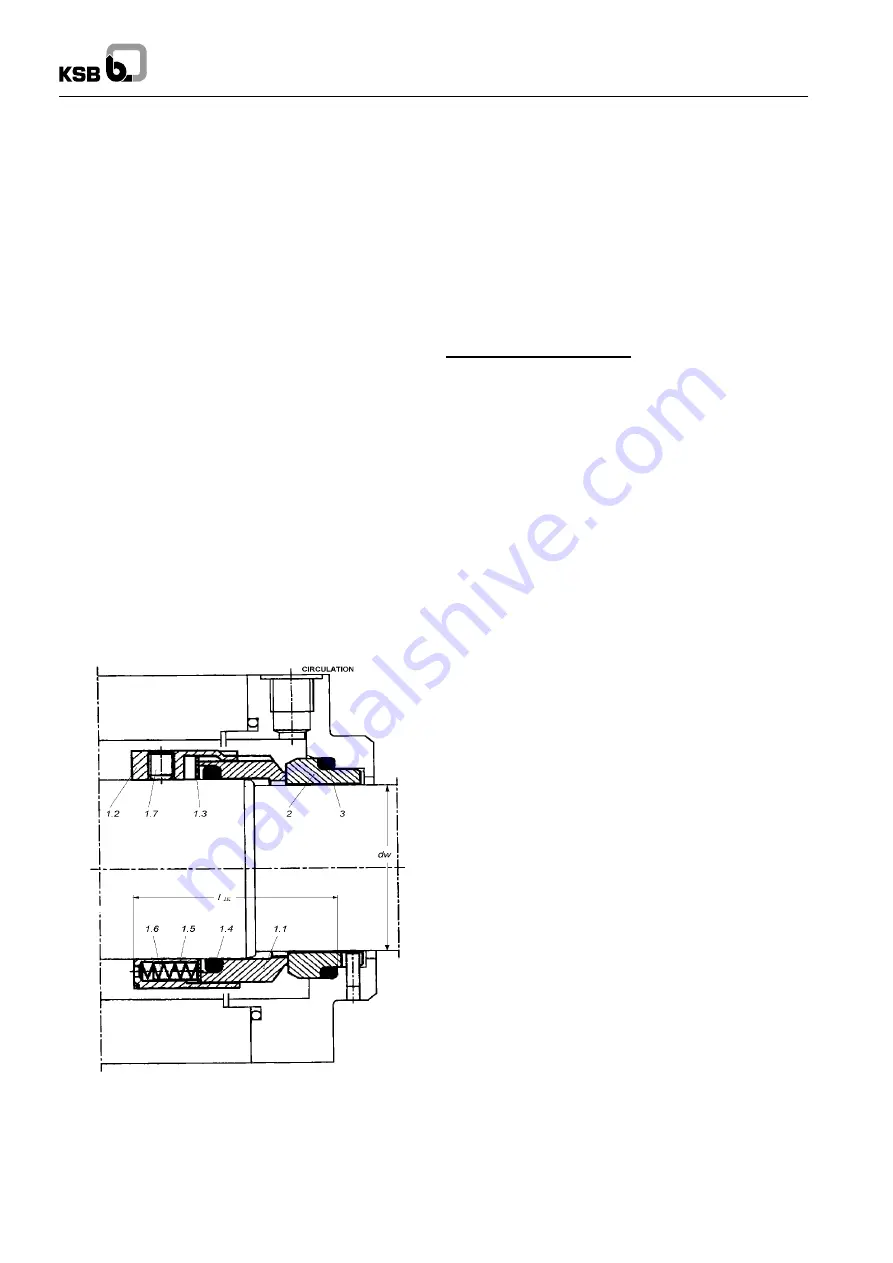
30
Operating maual mechanical seal
Rev. 0, 13.02.2004
D
Thread--locking compound, e.g. type ”LoctiteR Nr. 243”,
producer: Loctite Corporation
D
O--ring extractor
D
Set of hex. keys (WAF 2 mm -- 6 mm)
D
Cardboard washers to protect the contact faces during in-
stallation
D
Manual screw press (compulsory from DN 80 mm)
J
INSTALLATION
Refer to the general pump assembly drawing when installing
the mechanical seal.
Mechanical seals are precision--machined machinery compo-
nents which have been inspected several times. They must be
installed with due care and in compliance with certain procedu-
res, particularly regarding the contact faces and elastomer
seals.
Utmost cleanliness must be ensured in the immediate vicinity
of the location where a mechanical seal is to be installed.
Never use force
when installing a mechanical seal.
Unpack the seal and inspect the spring--loaded ring, seat ring,
O--rings and contact faces for damage.
D
Never place the spring--loaded ring and the seat ring on the
table facing down without protecting the contact faces.
D
Thoroughly clean all parts with alcohol and paper tissue.
The sequence of operations required to install the mechanical
seal in the machine depends on the design of the machine in
question, which is described in the pump’s operating manual.
Unless otherwise stated, apply a very thin coat of grease to
O--rings which will slide into or onto other components during
mechanical seal installation.
Fig. 1: General mech. seal design
Primary seal components
1.1
Spring--loaded ring
2
Seat ring
Secondary seal elements
1.4
O--ring (dynamic)
3
O--ring (static)
Spring components
1.5
Guide sleeve
1.6
Spring
Torque transmission and housing components
1.2
Torque--transmitting sleeve
1.3
Thrust ring
1.7
Grub screw
Possible installation sequence:
D
Slide the degreased O--ring onto the seat ring.
D
Cover the contact face of the seat ring with a cardboard
washer. Generously lubricate the seat ring with water or al-
cohol and press it slowly and evenly into its seat. Use a spa-
cer, if necessary. Check squareness of seat ring to the shaft
axis.
D
Apply a thin coat of grease to the shaft protecting sleeve in
the mechanical seal area.
'
Never use mineral oil base lubricants on sealing ele-
ments made of ethylene propylene rubber (swelling,
possibly decomposition).
D
Slide the rotating seal assembly with greased O--rings onto
the shaft protecting sleeve.
D
Fit the degreased grub screws, having applied one drop of
thread--locking compound (e.g. Loctite R No. 243) to each
screw.
D
Tighten the grub screws to lock the torque--transmitting
sleeve in place.
D
Clean the contact faces with propyl alcohol and paper tissue
(
no cloth, no cleaning rags
!) to remove any smears. Do
not touch the contact faces with bare fingers after that.
'
Do not apply lubricants to the contact faces. The contact
faces must be installed in clean and dry condition.
D
Fit the seal cover with pre--assembled seat ring.
J
COMMISSIONING
Prime the pump and the seal chamber with the fluid handled
and vent thoroughly. The seal is now ready for operation.
J
SAFE OPERATION
For single mechanical seals, the pressure in the seal chamber
of the pump must always exceed ambient pressure, to prevent
any air intake at the seal faces, which would result in dry running
and thus failure of the mechanical seal.
In all operating conditions, the product to be sealed off must be
available in liquid state at the mechanical seal, particularly du-
ring pump start--up and shutdown.
If the operating conditions indicated are observed and the in-
structions given in this operating manual are complied with, the
mechanical seal can be expected to give trouble--free opera-
tion.
J
HEALTH AND SAFETY
Mechanical seals are often used for sealing off hazardous sub-
stances (chemicals, pharmaceuticals, etc.). The applicable in-
structions and regulations for handling hazardous materials
must absolutely be adhered to.