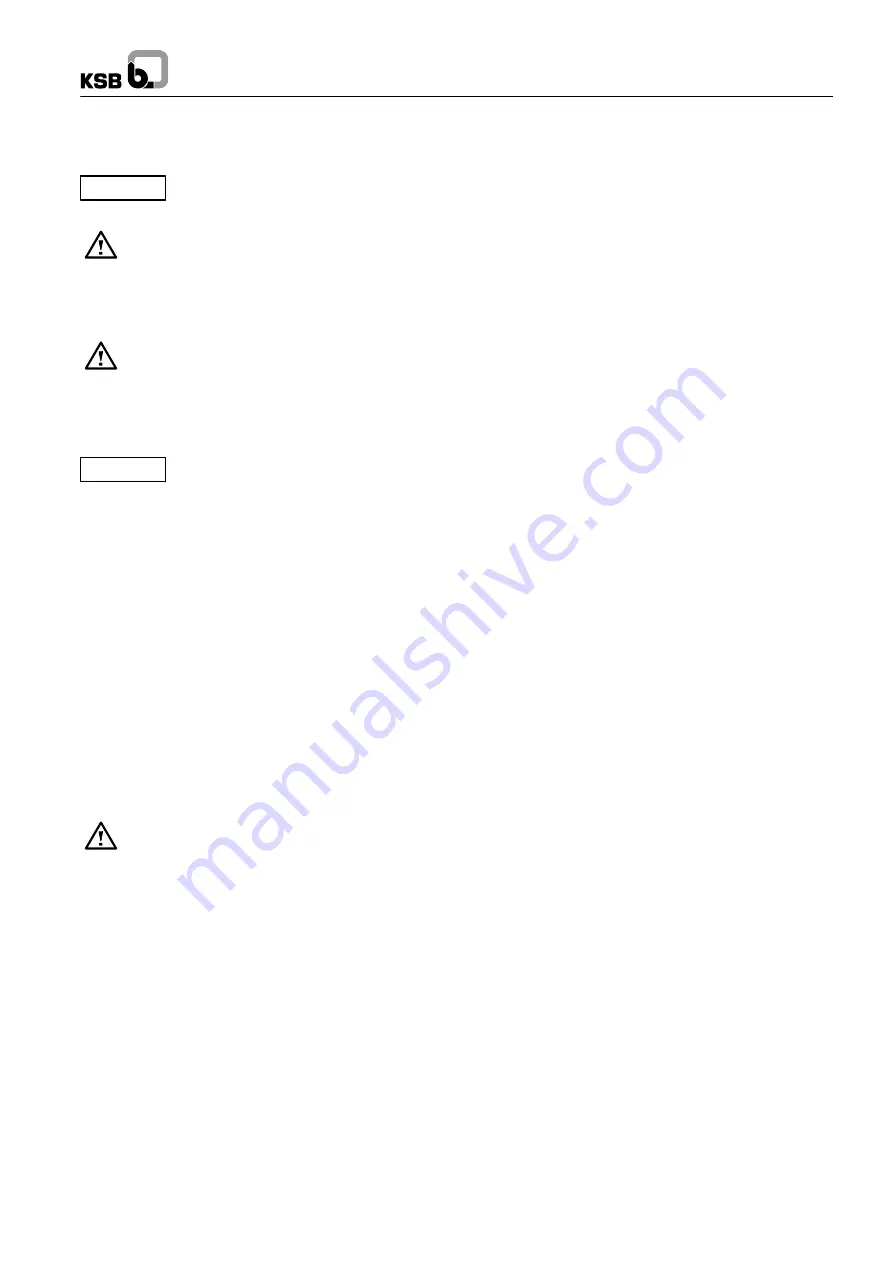
Caution
Caution
Omega
11
7.2
Maintenance / Inspection
7.2.1
Supervision of Operation
The pump shall run quietly and free from
vibrations at all times. The pump must never be
allowed to run dry.
Prolonged operation against a closed shut--off element
is not permitted in order to prevent the medium handled
from heating up.
At room temperatures of up to 30
_
C (86
_
F) the bearing tempe-
rature shall be below 90
_
C (194
_
F). At higher room tempera-
tures, the bearing temperature shall be below 100
_
C (212
_
F).
During pump operation the shut--off element in the inlet
line must not be closed.
Any stand--by pumps installed shall be switched on and then
immediately off again once a week to keep them operational.
Attention shall be paid to the correct functioning of the auxiliary
connections.
If the flexible coupling elements begin to show
signs of wear, they must be replaced in due
time. See section ”
Coupling
”.
If an external supply of sealing, flushing or lubricating liquid is
used, make sure supply pressure is 1.0 to 2.0 bar higher than
pressure at the suction nozzle.
On pumps fitted with a gland packing the packing must drip
slightly during operation. The gland cover should therefore only
be gently tightened. (See section 8 ”
Special instructions for
subassemblies, shaft seal variants
”).
7.2.2
Shaft Seal Maintenance
For required maintenance work on gland packings please refer
to section 8.1. ”
Shaft seal
”. Mechanical seals are mainte-
nance--free.
7.2.3
Bearing Maintenance
The bearings are maintenance--free and greased for life. No
re--lubrication is required.
7.3
Dismantling
Before dismantling, secure the pump so as to make sure
it cannot be switched on accidentally. The shut--off ele-
ments in the suction and discharge lines must be closed. The
pump must have cooled down to ambient temperature, pump
pressure must be released and the pump must be drained.
Dismantling and reassembly must always be carried out in ac-
cordance with the relevant sectional drawing.
7.3.1
Fundamental Instructions and
Recommendations
Repair and maintenance work to the pump must only be carried
out by specially trained personnel, using original spare parts.
Observe the safety regulations laid down. Any work on the mo-
tor shall be governed by the specifications and regulations of
the respective motor supplier.
Dismantling and reassembly must always be carried out in ac-
cordance with the relevant general drawing. The general dra-
wing and other relevant documents are found in the annex. The
dismantling sequence can be derived from the general dra-
wing.
In case of damage you can always contact our nearest custo-
mer service centre.
7.3.2
Preparations for Dismantling
The pump is designed so that the complete rotor can be remo-
ved in the sequence described below without removing the suc-
tion or discharge pipe or disturbing the alignment of the pump
unit:
·
Close the suction and discharge--side gate valves and drain
the pump by opening the drain plug (903.01 bottom) and
vent plug (903.01 top).
·
Remove any pipes between additional equipment and the
pump.
·
Remove the coupling guard. Decouple pump--side coupling
half as described in the appendix.
·
Loosen and push back the seal cover (471), if a mechanical
seal is fitted.
·
Undo the flange screws (901.01 / 901.02) and separate the
upper casing half (105.02) from the lower casing half
(105.01) with the aid of the forcing screws. Remove with lif-
ting gear. The interior of the pump (impeller with casing
wear rings, shaft seal) is now accessible for inspection.
·
Remove the screwed connection (901.04) between bearing
housing (350.01) and bearing brackets. Also undo the nuts
(920.05) and bolts (901.07) which secure the bearing cover
(360).
·
Press the bearing housing out of the recesses and lift the
rotor out of the lower casing half. For further disassembly,
place securely in horizontal position.
·
Pull off the bearing housing of the fixed bearing (opposite
the drive end).
·
Undo and remove the keywayed nuts (920.03).
·
Remove the deep--groove ball bearing (312) with bush
(520) from the shaft.
·
Remove the bearing cover (360).
·
Remove the V--ring (412.02) from the shaft--protecting
sleeve (524.01).
·
Pull off the shaft--protecting sleeve (524.01).
·
Remove the shaft seal housing (441).
·
The impeller (234) is located with a sliding fit on the shaft
and can normally be removed easily. In case of difficulty, it
can be loosened by gently tapping the hub with a wooden
hammer.
·
Remove the second shaft protection sleeve (524.01) com-
plete with the shaft seal housing (441), if fitted.
·
Remove the coupling half.
·
Pull off the bearing housing (350.01).
·
Remove the circlip (932) and pull off the deep--groove ball
bearing (321).