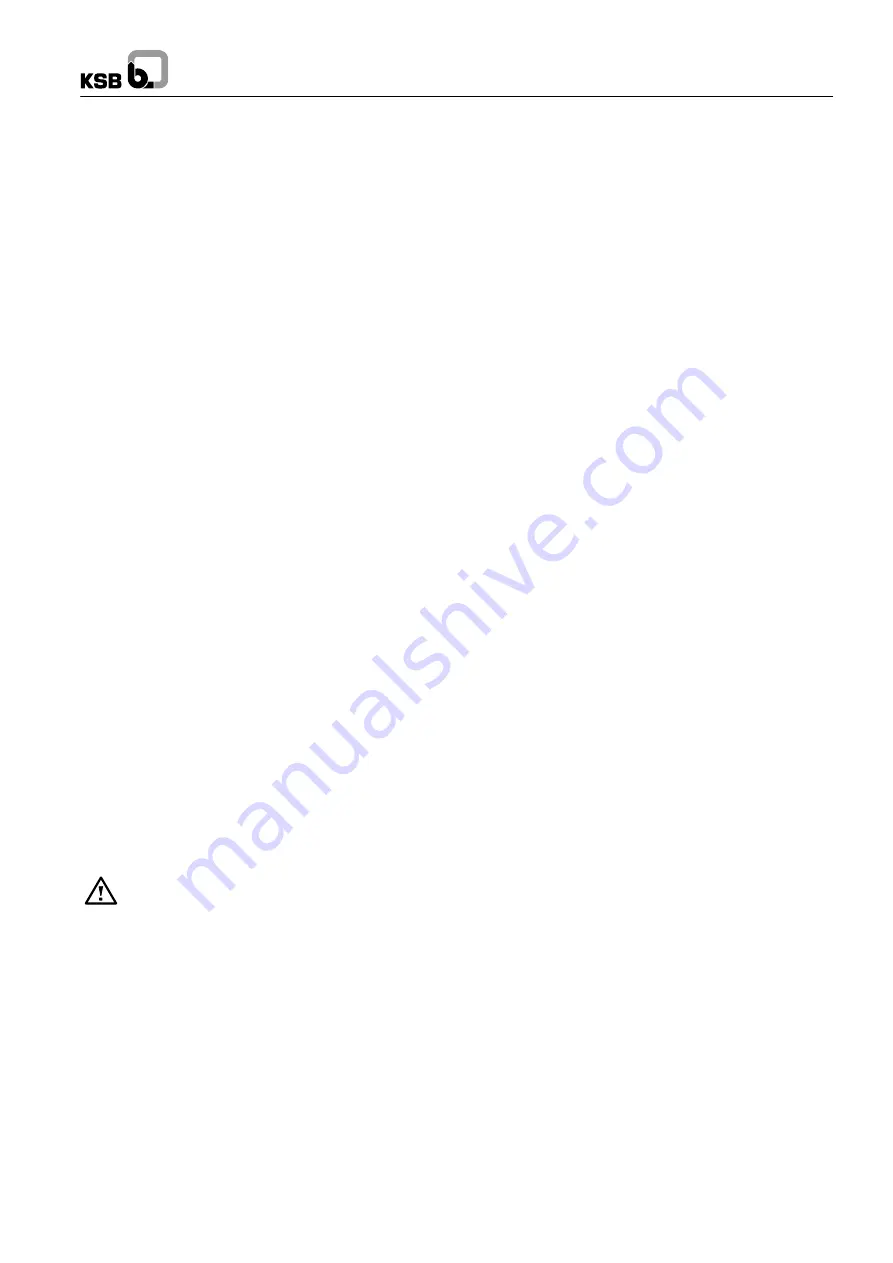
Omega
21
Installation
Never use force
during mechanical seal installation.
·
Slip the degreased O--ring onto the seat ring.
·
Cover the contact face with a cardboard washer.
·
Push the seat ring slowly and evenly into its seat. Use a spa-
cer sleeve, if necessary. Lubricate with a generous amount
of water or alcohol.
·
Verify that the seat ring position is normal to the shaft axis.
·
Push the rotating assembly with the
degreased
joint rings
onto the shaft. Thread in the
degreased
grub screws with
1 drop of thread sealant each (e.g. Loctite No. 243) and po-
sition the mechanical seal by tightening the grub screws.
The installation dimensions given in the drawing must be
adhered to.
·
The contact faces must only be cleaned with propyl alcohol
and paper tissue (no cleaning rags or cloth). Clean carefully
to remove any smears. Do not touch the contact faces with
bare fingers afterwards.
The contact faces must not be lubricated; they must be clean
and dry.
·
Assemble the seal cover with the installed seat ring.
Commissioning
Flood the pump and the seal chamber with the medium to be
handled and vent carefully. The seal is operational now.
Reliable seal operation
On
single--acting
mechanical seals, the
pressure in the seal
chamber
of the pump (stuffing box) must always
exceed am-
bient pressure
, to prevent any
air intake
at the seal faces,
which would result in
dry running
and thus
failure of the me-
chanical seal
.
In all operating conditions
, the product to be sealed off must
be available
in liquid state
at the mechanical seal, particularly
during pump start--up and shutdown. This must be ensured by
appropriate facilities on the pump (e.g. heating).
If the operating conditions indicated are observed and the in-
structions given in this operating manual are complied with, the
mechanical seal can be expected to give trouble--free opera-
tion.
Should the mechanical seal
fail
, the liquid to be sealed
off may
spurt out
. Take
suitable precautions
to pre-
vent hazards to persons and the environment, e.g. install
splash guards, wear safety goggles, etc.
Proper disposal
of
leakage shall be arranged for and supervised
by the operator
.
Faults
Determine and document the nature of the fault.
In the event of a fault as evidenced by excessive leakage, ob-
serve the tendency of the leakage amount. Changes in opera-
ting conditions must be documented. If an excessive tempera-
ture rise is detected, the mechanical seal must be shut down for
safety reasons.
A continuous flow of leakage indicates a fault.
During the warranty period the mechanical seal shall only be re-
moved and dismantled with the manufacturer’s approval or un-
der instructions of the mechanical seal manufacturer’s service
engineers.
If the
fault
cannot be remedied by the operator or if the cause
is unclear, please contact the KSB service centre.
Maintenance
Mechanical seals operated in compliance with the manual are
maintenance--free; however, wear parts will have to be repla-
ced as required.
The mechanical seal should be inspected in accordance with
the plant inspection schedule. We recommend to have the me-
chanical seal inspected by KSB service centre.
If the mechanical seal is inspected during plant outage, the con-
tact faces should be re--worked and all elastomer seals and
springs should be replaced.
Repair
If the seal needs to be
repaired
, always
return the complete
seal
to the manufacturer. The manufacturer will know best
which parts can be re--worked and which parts have to be repla-
ced to ensure an optimum sealing effect.
If repair on the spot is absolutely necessary
(e.g. no spare
seal available, long transport distances, problems with customs
procedures),
skilled
operator staff may carry out the repair
work in a clean workshop to the directions of KSB service cen-
tres.