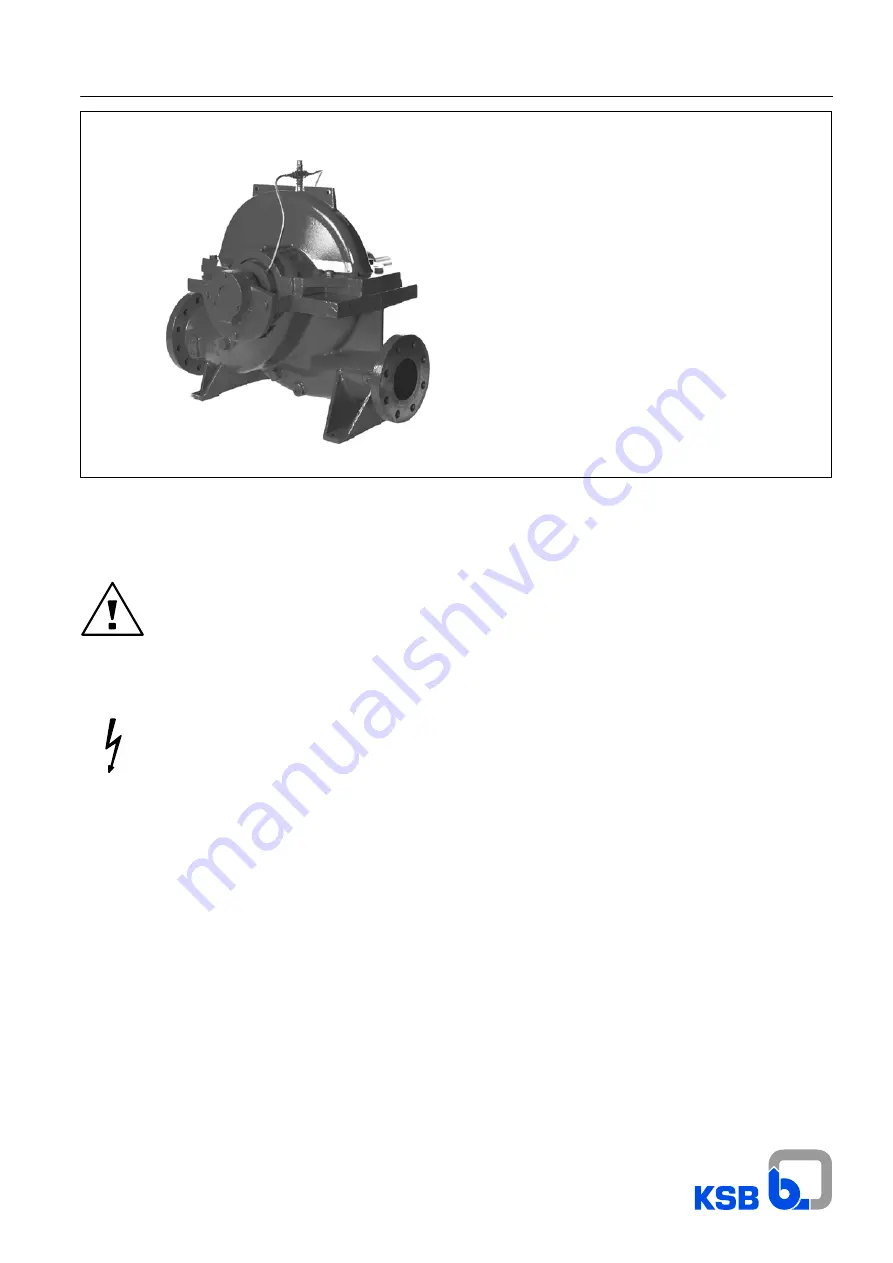
Omega
1384.8/4--10
Operating instructions
Volute casing pump
with radial impeller
Pump set
Horizontal installation -- 3 E
These operating instructions contain fundamental information and precautionary notes.
Please read the manual thoroughly prior to installation of unit, electrical connection and
commissioning. It is imperative to comply with all other operating instructions referring to
components of individual units.
Any work on the unit must only be carried out with the electrical connections (incl. control cable)
disconnected (or unplugged). Make sure that the pump set cannot be switched on accidentally.
Ident--No.:
01 059 616