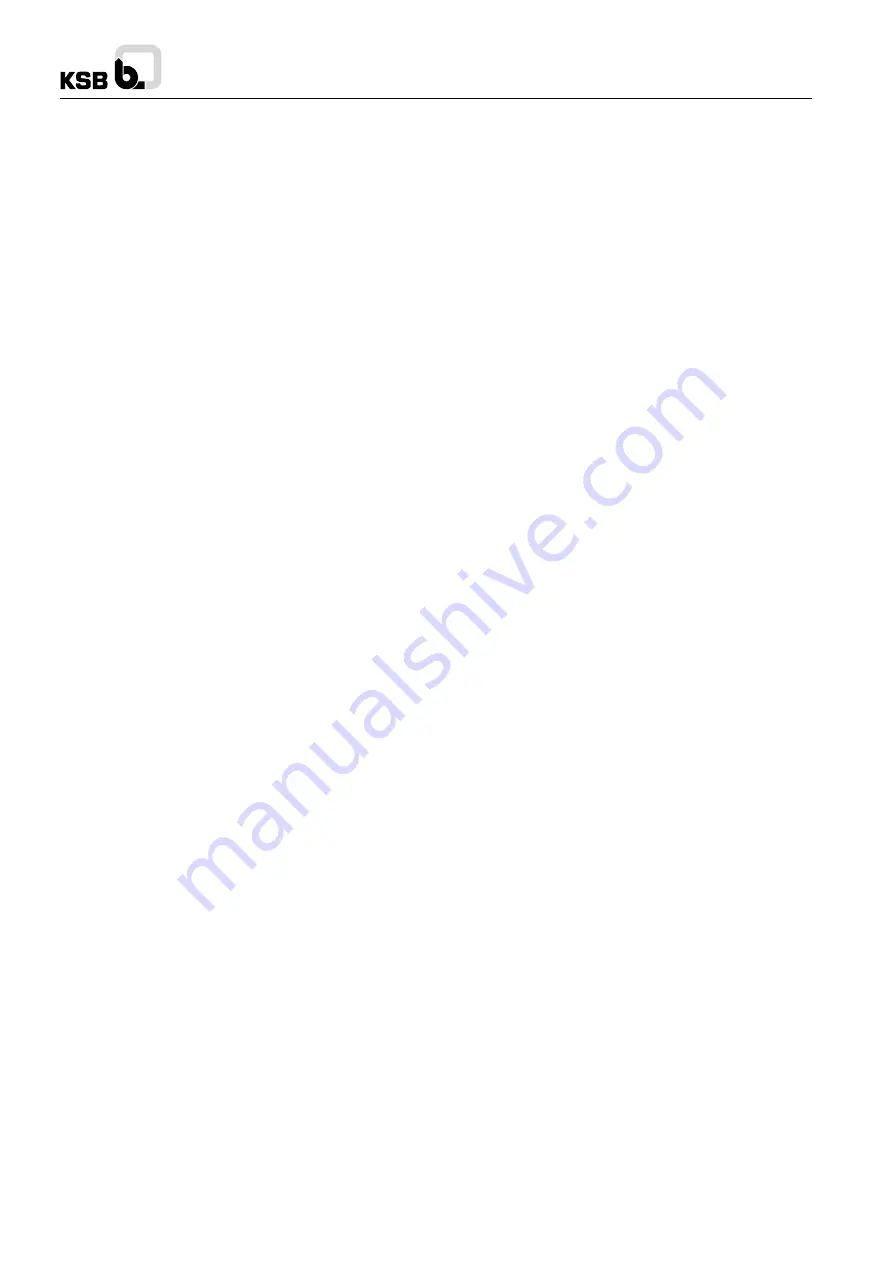
KWP
3.3
Shutdown
Close discharge valve
Switch off motor and check that the pump run down smoothly
and gradually to a standstill.
Close suction valve.
Shut off sealing or flushing liquid supply, and close valve in
vacuum balance line, if applicable.
In case of frost, the pump should be drained or otherwise
protected against freezing, if the pump is shut down for
prolonged periods.
4
Maintenance and lubrication.
4.1
Supervision of operation.
The pump should run smoothly, quietly and vibration free at
all times. The pump must never run dry.
Never run the pump for long periods against a closed discharge
valve. The bearing temperature may exceed the ambient
temperature by up to 50
0
C but must not rise above 90
0
C.
Check the oil level per section 2.1.1. The isolating valves in
the auxiliary lines, if applicable, must remain open while the
pump is running.
If the pump has a gland packing, this should leak slightly during
operation. The gland should only be tightened lightly.
Any standby pumps should be started up, then shut down
immediately, at least once a week, to ensure they are in
constant readiness for operation. Check the condition of the
auxiliary connections.
The flexible coupling elements should be regularly checked
and replaced as soon as they show signs of wear.
It is necessary to maintain a log book on hourly basis, whether
the suction and discharge pressure, actual discharge bearing
temperatures (pump end and motor end), motor current and
voltage should be noted.
4.2
Lubrication and lubricant changes
4.2.1
Lubrication
The antifriction bearings are mineral oil lubricated. See section
4 of the lubricant flowrate.
4.2.2
Oil change
The first oil change must be carried out after 300 hours of
operation; all subsequent oil changes after 3000 operating
hours.
4.2.2.1
Procedure
Remove the drain plug below the constant level oiler and drain
off the oil.
When the bearing bracket is empty, replace the drain plug
and fill with oil as described in section 3.1.1.
4.3
Preservation
If the pump is taken out of service for a prolonged period, it is
advisable to dismantle it completely. Proceed as described in
section 4.2, “Dismantling”. All components should be
thoroughly cleaned, dried and all machined surfaces coated,
with grease. Thereafter, the pump should be reassembled.
All apertures on the pump should be reassembled. All apertures
on the pump should be plugged with wooden stoppers soaked
in oil or blanked off with wooden cover plates fitted with O
rings. A sachet filled with Silica gel (Silica gel absorbs moisture)
should be attached to the inside faces of the oil soaked wooden
cover plates on the suction and discharge nozzles (i.e inside
the nozzles.)
The packing should be removed from the stuffing box
compartments and these should be sealed by oil soaked
wooden half tubes, each provided with two O rings, in order to
prevent the penetration of moisture (not applicable to pumps
fitted with mechanical seals)
CAUTION :
Only use acid free oils and greases when preserving the pump.
5
Special instructions &
recommendations.
CAUTION
If a constant level oiler 638 is provided, it must be screwed
into the upper tapped hole on the bearing bracket 336 before
filling in any oil (see Fig. 7)
5.1
Dismantling and reassembly.
5.1.1
General
CAUTION :
Safeguard the pump against unintentional switching on before
proceeding with dismantling.
The isolating valves in the suction and discharge lines must
be closed.
The pump casing must have cooled down to ambient
temperature.
The pump casing must be pressureless and drained.
Always refer to the relevant sectional drawing when dismantling
and reassembling the pump.
The process type of construction enables the pump to be
dismantled without disconnecting the piping from the pump
casing or removing the latter from the baseplate.
If a spacer type coupling is fitted, the driver can also remain
bolted on the baseplate.
Handle all components with great care during dismantling,
The impeller and coupling should only be pulled off or pushed
on to the shaft with the aid of a suitable puller / pusher device.
After completion of dismantling, all dismantled components
should be thoroughly cleaned and examined for signs of wear.
Damaged or worn components should be touched up or
replaced by new ones if necessary. Deposits on the impeller
and inside the casing should be cleaned off.
When cutting new Gaskets, make sure they are of exactly the
same thickness as the old ones.
It must be possible to rotate the pump rotor easily by hand
after reassembly, without causing any scraping noises. Prime
bearing bracket with oil according to 2.1.
5.1.2
Dismantling
5.1.2.1
Standard bearing arrangement.
1. Remove coupling guard.
2. Disconnect spacer sleeve between the pump and motor
coupling halves (if a non-spacer type coupling is fitted, the
driver must be removed from the base plate)
3. Disconnect auxiliary piping for sealing and leakage liquid.
4. Unscrew hexagonal nuts 920.1 and the bolts 901.4 fixing
the support foot 183 to the base plate. Remove the support
foot.
5. Loop a rope tightly around the top stay of the bearing bracket
lantern ( to sustain the weight of the subassembly described
below ). Force off the distance piece 344, including the bolted-
on bearing bracket 330 and pump rotor, by means of the forcing
screw 908.1 on the bearing bracket lantern.
6. Carefully pull the complete rotor out of the pump casing
and set it down. Unscrew drain plug 903.11 on the bearing
bracket & drain the oil. Tilt the bearing bracket to ensure
complete removal of oil.
5