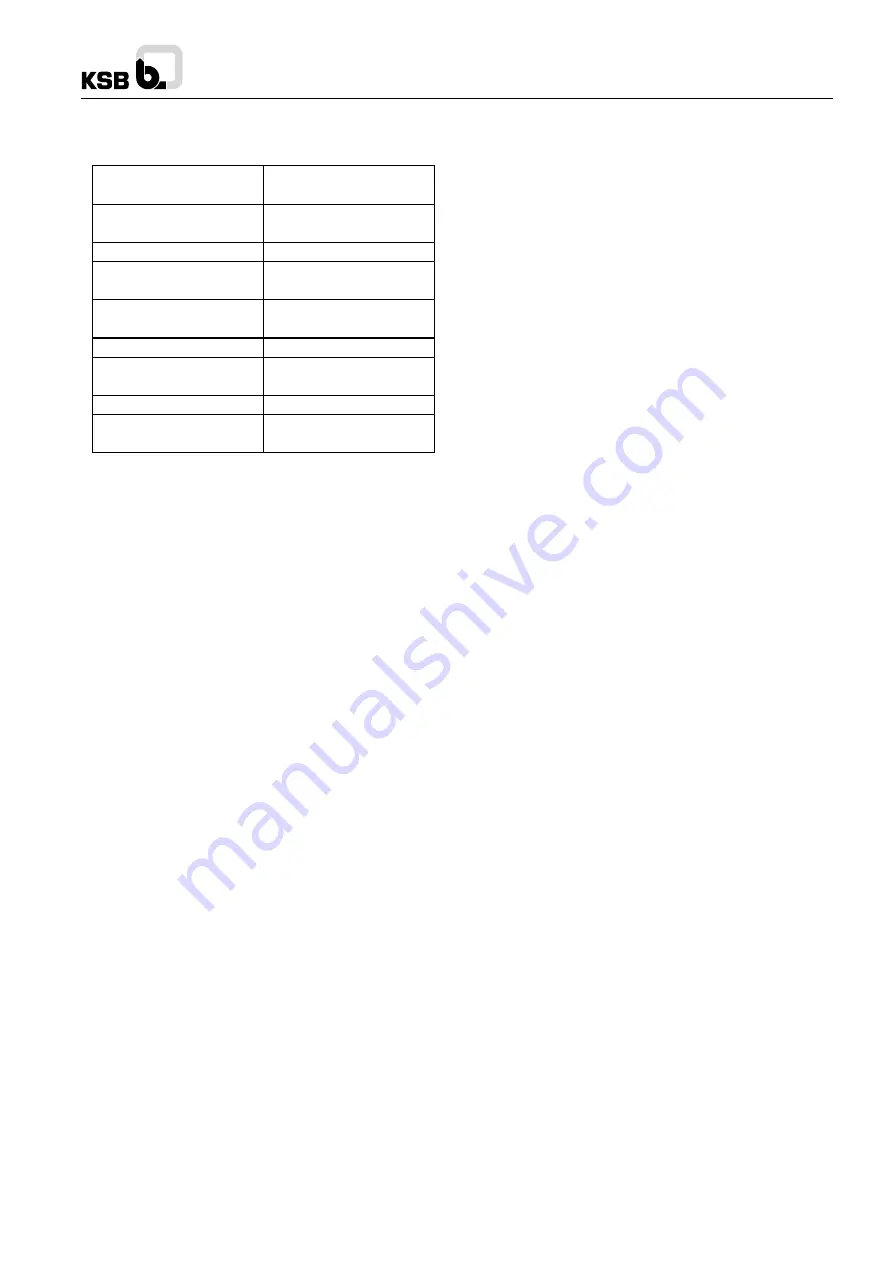
KWP
6
Faults
6.1
Faults, causes & remedies
6.2
Cause - Remedy
1)
1. The pump delivers against an excessively high
discharge pressure.
Open discharge valve further until the dutypoint conditions
have been attained (adjusted)
2. Excessively high back pressure.
- Fit an oversize impeller
- Increase rotational speed (Applies to turbine or I.C. engine
driven pumps)
3. The pump and / or piping are incompletely vented or primed.
- Vent or prime the pump and system completely.
4. Suction line or impeller clogged
- Remove deposits in the pump and / or piping.
5. Formation of air pockets in the piping.
- After piping layout
- If necessary, fit a vent valve
6. NPSH available is too low (on positive suction head
installations)
- Check liquid level in suction vessel
- Open isolating valve in suction line fully.
- Install different suction line if necessary,
if the friction losses in the suction line are excessive.
- Check suction line strainer
7. Excessively high suction lift.
- Clean out suction strainer basket and suction piping.
- Check liquid level in the pit
- Alter the suction line
8. Entertainment of air through the stuffing box
- Sealing liquid passages are clogged; clean them out.
- If necessary, arrange a sealing liquid supply from an
outside source, or increase sealing liquid pressure.
- Fit a new shaft seal.
9. Reverse rotation
- Change over two of the phase leads of the power supply
cable.
10. Rotational speed is too low.
2) 3)
- Increase rotational speed
- Increase voltage power supply
11. Excessive wear of the pump internal
- Replace worn components by new ones.
12. Pump back pressure is lower than specified in the
purchase order.
- Adjust duty point accurately by means of the isolating
valve in the discharge line.
In case of persistent over loading, trim the impeller if
necessary.
2)
13. Specific gravity or viscosity of the fluid pumped is higher
than that specified in the purchase order.
2)
14. Stuffing box gland tightened excessively or askew.
Adjust the gland as required.
15. Excessive rotational speed
- Reduce speed (applies to turbine or I.C. engine driven
pump.)
2) 3)
17. Worn shaft seal
- Check condition of shaft seal and renew it if
necessary.
- Check flushing liquid or sealing liquid pressure.
18. Grooving, score marks or roughness on shaft
protection sleeve surface.
- Fit a new shaft protection sleeve
20. Stuffing box gland or seal cover incorrectly
tightened. Wrong type of packing material used.
- Remedy the fault
21. The pump runs rough
- Correct the suction conditions
- Check alignment of pumping set and realign if
necessary.
- Rebalance the pump rotor dynamically.
- Increase the suction pressure at Pump suction
nozzle.
22. Pumping set misaligned
- Check alignment at coupling and realign the set if necessary.
23. The pump is warped
- Check piping connections and pump fixing bolts.
25. Too much or too little lubricant, or unsuitable
lubricant quality.
- Top up lubricant, reduce quantity of lubricant, or change
lubricant quality
26. The prescribed coupling gap has not been
maintained.
- Restore correct coupling gap in accordance with the data
on the foundation drawing.
27. Operating voltage is too low.
28. The motor is running on two phases only
- Replace the defective fuses
- Check the cable connections
29. The connecting bolts are slack
- Tighten the bolts
- Fit new gaskets
30. The rotor is out of balance
- Clean the rotor
- Rebalance the rotor dynamically
31. Defective bearings
- Fit new bearings
32. Insufficient rate of flow
- Increase the min. rate of flow.
1)
The pump should be made pressureless before
attempting to remedy faults concerning parts exposed to
pressure.
2)
Please refer to KSB
3)
This fault can also be remedied by altering the impeller
diameter.
Trouble
Code number
Cause-remedy
Pump delivers insuficient
liquid
1,2,3,4,5,6,7,8,9,10,11,2
8
Driver is overloaded
12,13,14,15,23,27,28
Excessively high pump
discharge pressure
15
Excessively high bearing
temperature
22,23,25,26,31
Leakage at the pump
29
Excessive leakage at
shaft seal
17,18,20,21,22,23
The pump runs rough
3,6,11,12,22,23,30,31,32
Excessive temperature
rise inside the pump
3,6,32
10