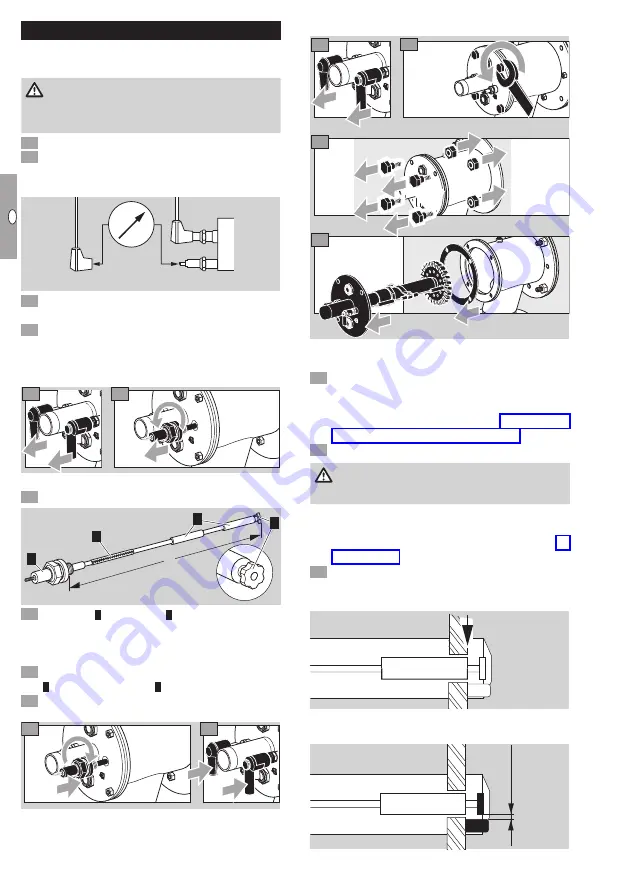
GB-10
D
GB
F
NL
I
E
Maintenance
We recommend that a function check is carried out
every six months.
WARNING
Risk of burning! Outflowing flue gases and burner
components are hot.
Check the ionization and ignition cables.
Measure the ionization current.
▷
The ionization current must be at least 5 µA and
must not vary.
+
μ
A
–
Z
I
Disconnect the system from the electrical power
supply.
4
Shut off the gas and air supply – do not change
the restrictor settings.
Checking the ignition and ionization
electrodes
6
5
▷
Ensure that the electrode length does not change.
7
Remove dirt from electrodes or insulators.
L
1
2
3
4
8
If the star
4
or insulator
is damaged, replace
the electrode.
▷
Before changing the electrode, measure the
total length
L
.
9
Connect the new electrode with the spark plug
using the dowel pin
.
0
Adjust spark plug and electrode to the measured
total length
L
.
11
12
▷
Turning the spark plug makes it easier to feed
the electrode into the burner insert.
Checking the burner
16
13
14
15
▷
If the burner insert is dismantled, the gas housing
gasket will have to be renewed.
7
Place the burner insert in a safe place.
▷
Depending on the amount of dirt or wear: replace
the ignition/ionization electrode rod and dowel
pin during servicing – see page 10 (Checking
the ignition and ionization electrodes).
8
Check burner head for dirt and thermal cracks.
WARNING
Risk of injury! Burner heads have sharp edges.
▷
When replacing any burner components: ap-
ply ceramic paste to the screw connections in
order to avoid cold-setting – see page 12
(Accessories).
9
Check the electrode positions.
▷
The insulator must be flush with the front edge
of the burner air disc.
▷
Distance of ignition electrode from ground pin or
gas nozzle: 2 ± 0.5 mm (0.08 ± 0.02").
2
±
0,5
mm
(0.08
±
0.02"
)