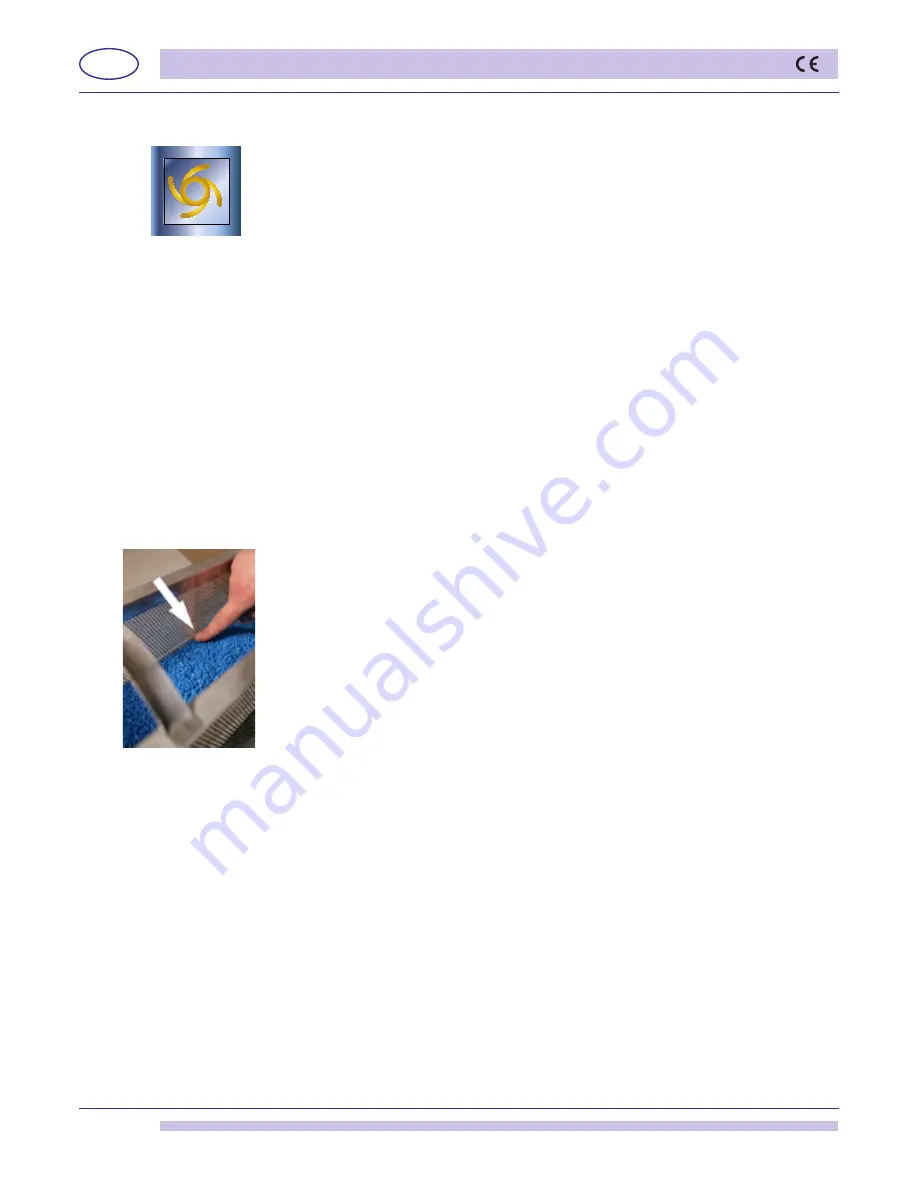
EN
page 36
USER SECTION
7. OPERATION
7.1 General operation
The machine needs 3 connections to run:
• Electric;
• Water supply;
• Drain.
The machine is designed with a wash chamber inside which there is:
• A basket support, connected to a clutch equipped gear, where the rack is placed to rotate
during the wash cycle.
• Two interchangeable wash arms where water and water mixed with granules flow from.
• A rinse arm connected to a pump which withdraws from the boiler guaranteeing constant
temperature rinse ("Plus" system).
• A filter located under the chimney to prevent granules from rising and getting stuck in the
fan located at the end of the chimney.
A tank is found under the chamber which contains water in one part and water mixed with
granules in the other. The part containing water shall always be covered by blind chutes to
avoid granule contamination.
The part containing the granule water mixture shall always be covered by work perforated
filters or, in the granules recuperation phase, the collection strainer with special lateral
compensatory chutes (see chap. 7.7).
7.2 Machine preparation
• Prepare the right amount of granules by filling the strainer to the indicated level (see
photo 1).
• Pour the contents into the right-hand side of the tank.
• Place the overflow tube in the dedicated seat, at the tank bottom.
• Insert the two chutes above the water-only area (left-hand side of the tank) and the two
perforated filters above the granule area (right-hand side of the tank).
• The filters shall be cleaned every 15-20 cycles and whenever necessary.
Do not use
the machine without filters.
• Make sure that the wash and rinse arms are properly placed.
• Make sure that the rack support is inserted properly.
• If the machine is equipped with a detergent dispenser, insert the transparent hose into
the detergent canister.
• Insert the special green rinse-aid chemical container and check that the quantity is
sufficient for the workload of the day.
• Shut the door.
• Open the water valve, activate the main wall switch and proceed with turning on the
machine by pressing key “B” (see fig. 7). The green led will come on. After a few seconds,
the filling stage shall begin.
• After water-filling, the machine will automatically activate the heating stage.
• The machine shall be ready for washing, only when the boiler and tank thermometers
indicate that the proper temperatures have been reached: 80-85°C for the boiler and
50-55°C for the tank.
• Insert the rack with the various objects to wash and shut the door.
• Before beginning the wash cycle, insert the proper detergent into the tank (if the machine
is not equipped with an automatic dispenser).
• Select the wash cycle time using the keys (C/D) and the type of wash cycle (only water
or water and granule) using the keys (E/F) (see fig. 7). The green led shall come on in
correspondence to the selected cycle (1, 2, 3, 4,
∞)
.
• Start the cycle by pressing key “A” (see fig. 7) Cycle start-up shall be indicated by a cycle
selected blinking light. At the end of the cycle the light stops blinking and the word END
appears on the display.
• The machine is ready for a new wash cycle.
• It is recommended to replace the tank water with new water at least after 30 wash cycles
or 2-3 times a day.
photo 1