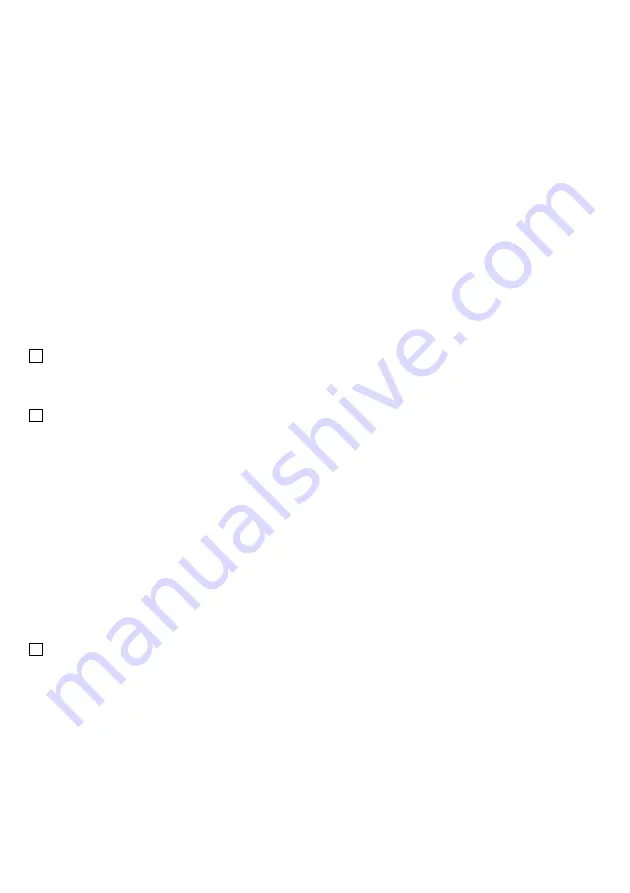
Smooth start
The start-up current limitation reduces the current when
starting up. The motor accelerates gradually to the pre-
selected speed, thereby protecting the operator and the
gears, and extending the service life of the machine.
Electronic overload protection
If an excessive load occurs which could damage the motor,
the integrated motor monitor reduces the rotation speed of
the angle grinder. The machine must be disengaged - and
ideally removed briefly from the work piece - so that full
power becomes available again.
Electronic control with motor-tacho generator
The adjusting wheel (20) of the full cycle control electro-
nics allows the preselection of optimal rotation speeds for
all grinding, cutting and polishing work. When under load
the motor-tacho generator provides an increased power
supply. The preselected rotation speed is held constant.
The working speed required is dependent on various
factors such as, for example, the type, hardness and
characteristics of the material being worked, and the type
and condition of the grinding, cutting and polishing tools
to be used. The optimal setting should be determined in
tests at the beginning of a job.
Use only low speeds when polishing.
When grinding, the best results are achieved if you
work at a setting angle of approx. 20° – 30°.
Disassembly/mounting of the protection cover
Turn the protection cover (4) until the cams (5) on the pro-
tection cover (4) align with the safety groove (6). The
protection cover (4) can now be easily lifted off the gear
flange. The protection cover is mounted in the opposite
order.
Cutting and grinding may only be done with the pro-
tection cover on!
Adjusting the protection cover
The protection cover (4) can be moved into any position
required by loosening the pan head screw (7). Tightening
the pan head screw (7) locks the protection cover (4) into
position. When working with the protection cover swung
back and the curved handle mounted, make sure that the
protection cover is never swung over the handle side.
Danger of injury!
Mounting instructions for roughing and cutting wheels
The two examples of usage show how thick (5–10 mm)
and thin (1–6 mm) grinding wheels are to be fastened to
the spindle end with the clamping flange (18). A spindle
lock makes loosening and tightening the clamping flange
(18) with the pin-type face wrench easier. During this pro-
cess the pusher (19) must be pressed in.
Attention!
Actuate only during standstill!
Replacing carbon brushes
Our service personnel will carry out this and all other
servicing work quickly and professionally.
Before mounting tools, disconnect the machine from
the power supply, or remove the mains cable module
(21) from the casing using the locking device button
(22).
Mains cable
Damaged mains cables must not be used. They are to be
replaced immediately.
This has been made very straightforward by the new mains
cable module (21). Press both locking keys (22) and pull
the mains cable module (21) out of the handle. Insert the
new mains cable into the handle and lock in place. Diffe-
rent lengthed mains cables are available as special acces-
sories.
Only use the mains cable module for KRESS power
tools! Do not attempt to operate other electrical appli-
ances with it!
Accessories included in delivery
1 pin-type face wrench 30
Noise/vibration information
Measured values correspond with EN 50144.
Sound pressure level:
802 WS:
= 82.5+3 dB (A).
1052 WSE: = 86.5+3 dB (A).
Sound power level:
802 WS:
= 95.5+3 dB (A).
1052 WSE: = 99.5+3 dB (A)
Work place emission value:
802 WS:
= 85.5+3 dB (A).
1052 WSE: = 89.5+3 dB (A).
Operators require noise protection equipment.
The acceleration measured is usually less than 2.5 m/s
2
.
Special equipment
Roughing wheel for stones and non-ferrous metals
Roughing wheel for steel and castings
Cutting wheel for stones (stoneware)
Adhesive grinding wheels, complete set
Adhesive fleece (grit 180)
Adhesive supporting disc M 14
Vulcanised fiber wheels, complete set
Supporting wheel with clamping flage for vulcanized fiber
wheels
Steel wire cup-shaped brush
Environmental protection
Kress takes back used machines for resource saving re-
cycling. Due to their modular construction Kress machines
can be very easily broken down into their recyclable basic
materials. Hand in your old Kress machine at a dealer or
send them directly to Kress.
Subject to change without notice.
4
3
2