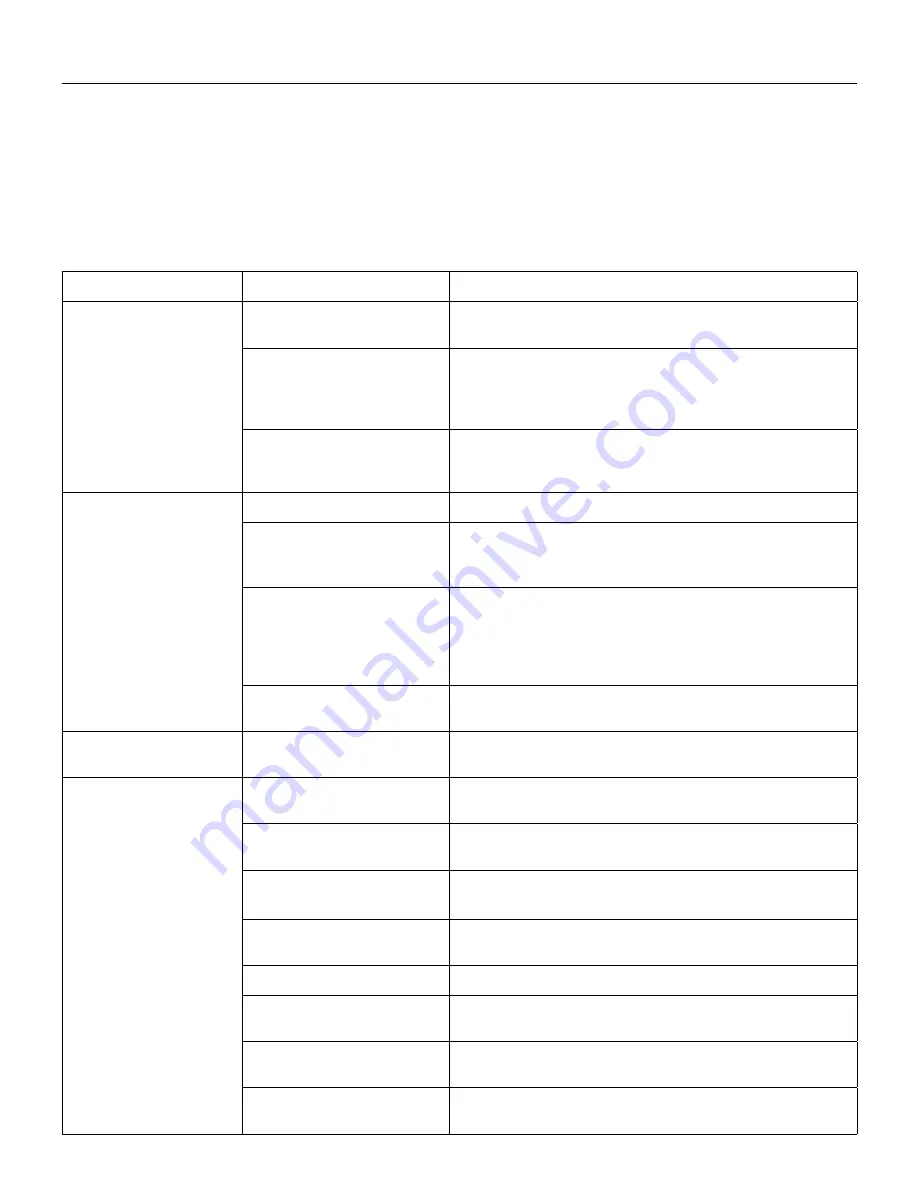
44
TROUBLESHOOTING
13.0 TROUBLESHOOTING
ATTENTION: Troubleshooting must be performed by a qualified
technician.
Before proceeding with the steps in the following troubleshooting
guide,
• Verify proper 120VAC power supply to the control module.
• Verify the control module battery pack and the remote
control batteries are fresh and installed with correct polarity.
• Verify all connections between the wire harnesses and the
system components are proper and positive.
• Verify the communication link is established between the
remote control and the IFC module.
• Verify inlet pressure meets the recommended inlet pressure.
If necessary, adjust line pressure regulator.
Issue
Cause
Solution
Pilot will not light
Electrical power interrupted or
disconnected
Restore electrical power to appliance or use battery back-up.
Wiring disconnection
Ensure batteries are fully charged if using battery back-up as
power source.
Use wiring schematic
to determine that all wiring connections are
secure and correct.
Gas supply turned off
Check remote shut-off valves from the appliance. Usually there is
a valve near the main gas line. There may be more than (1) valve
between the appliance and main gas line.
Pilot will not stay lit
No LP (propane) gas in tank
Check LP (propane tank). Refill if necessary.
Low gas pressure
Consult a plumber or a gas supplier.
Can be caused by situations such as a bent line, too narrow
diameter or pipe, or a low line pressure.
Pilot flame not making contact
with the flame rectification
sensor on the pilot assembly
Verify the pilot flame envelopes the top of the flame sensor and
extends far enough onto burner for ignition.
To adjust pilot flame, turn pilot adjustment screw on the gas valve
clockwise to decrease flame, and counterclockwise to increase
flame.
Pilot adjustment screw not
sealed
Seal pilot adjustment screw. Do not over-tighten.
Pilot flame always on, or
will not extinguish
Control system set to CPI mode
Set control system to IPI mode
Main burner flame will not
light
ON/OFF rocker switch in OFF
position
Switch rocker switch to ON position.
Gas supply turned off
Check for multiple shut-offs in the supply line. Verify gas supply is
turned on.
Low gas supply
Consult with plumber or gas supplier.
Check LP (propane) tank. Refill if necessary.
Wiring disconnection or
improper wiring
Check for faulty or incorrect wiring.
Plugged main burner orifice
Remove blockage.
Pilot flame
Verify the pilot flame is properly directed to ignite burner. See pilot
flame troubleshooting above.
Remote control not working
properly
Replace batteries.
No call for heat
Verify remote control is powered ON and thermostat operation is
turned OFF.