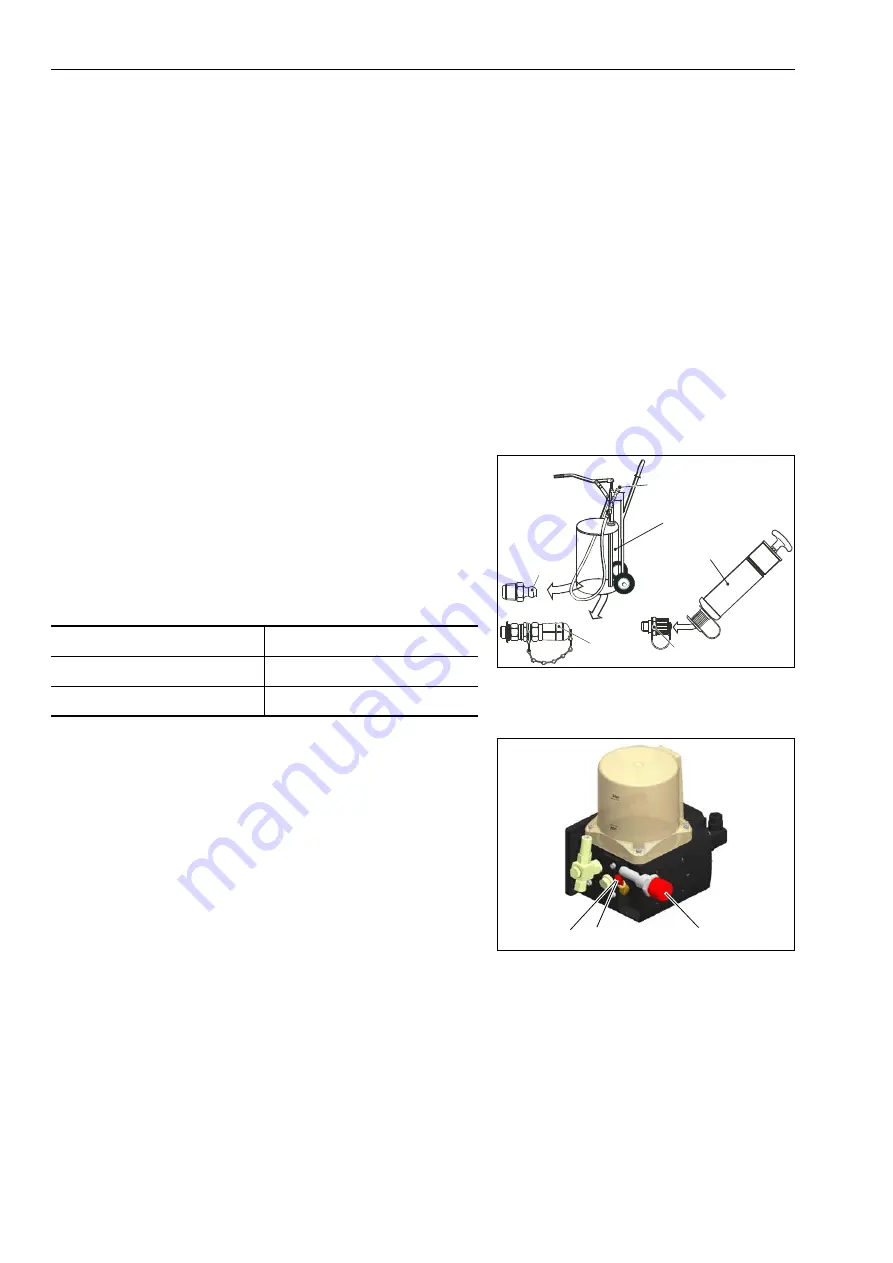
5.8 Maintenance procedure
Maintenance every 50 service hours
Maintenance
5-46
WA80M-7, WA100M-7 – VENAM03001
Central lubrication system – checking, replenishing grease
The following maintenance work is to be carried out as required
or every 50 service hours:
General function check
The basic function of the pilot device and the system compo-
nents can be checked by activating intermediate lubrication.
Regular check of the system components for leakage and
damage.
Visual inspection of the state of lubrication of the bearings and
observation of the lubrication pattern.
In the event of fault indications, consult your Komatsu distributor
to rectify the fault.
NOTICE
Only refill using clean lubricant and a suitable filling device (A or
B). Contaminated lubricant can lead to serious system malfunc-
tions.
Permitted lubricants
Grease of NLGI class 2 with EP additives, compatible with plas-
tics, NBR elastomers, copper and copper alloys and a max. flow
pressure of 700 mbar.
Fill the lubricant container to above the “MIN” marking but no
higher than the “MAX” marking.
When using the factory setting, it is sufficient to fill up for a mini-
mum of 50 hours.
If the lubrication times have been changed or several intermedi-
ate lubrications have been carried out, the level check must be
brought forward.
Depending on the design, lubricant can only be added via:
1. Cone-shaped grease nipple
2. Filling attachment
3. Filling cylinder
The connecting pieces must be free from dirt.
The transparent lubricant container allows you to carry out a vis-
ual level check.
If the container has been emptied to below the “MIN” mark, the
entire system must be bled. Consult your Komatsu distributor to
have the system bled.
1
1, 2
2
3
M20X1,5
A
B
Temperature range of grease
Viscosity classes
-20 °C to 120 °C
G2 LI
-40 °C to 100 °C
GLT2 LI
1 3
2
Summary of Contents for WA100M-7
Page 2: ......
Page 3: ...Foreword WA80M 7 WA100M 7 VENAM03001 1 1 1 Foreword...
Page 26: ...1 7 Equipment Foreword 1 24 WA80M 7 WA100M 7 VENAM03001...
Page 71: ...Operation WA80M 7 WA100M 7 VENAM03001 3 1 3 Operation...
Page 184: ...3 8 Reading error code Operation 3 114 WA80M 7 WA100M 7 VENAM03001...
Page 185: ...Troubleshooting WA80M 7 WA100M 7 VENAM03001 4 1 4 Troubleshooting...
Page 203: ...Maintenance WA80M 7 WA100M 7 VENAM03001 5 1 5 Maintenance...
Page 220: ...5 4 Fuel lubricants and coolants quantities Maintenance 5 18 WA80M 7 WA100M 7 VENAM03001...
Page 279: ...Technical data WA80M 7 WA100M 7 VENAM03001 6 1 6 Technical data...
Page 285: ...Special equipment attachments WA80M 7 WA100M 7 VENAM03001 7 1 7 Special equipment attachments...
Page 292: ...7 3 Central lubrication system Special equipment attachments 7 8 WA80M 7 WA100M 7 VENAM03001...
Page 293: ...Index WA80M 7 WA100M 7 VENAM03001 8 1 8 Index...
Page 298: ...8 1 Index Index 8 6 WA80M 7 WA100M 7 VENAM03001...
Page 299: ...Notes WA80M 7 WA100M 7 VENAM03001 9 1 9 Notes...
Page 300: ...Notes 9 2 WA80M 7 WA100M 7 VENAM03001...
Page 301: ...Notes WA80M 7 WA100M 7 VENAM03001 9 3...
Page 302: ...Notes 9 4 WA80M 7 WA100M 7 VENAM03001...