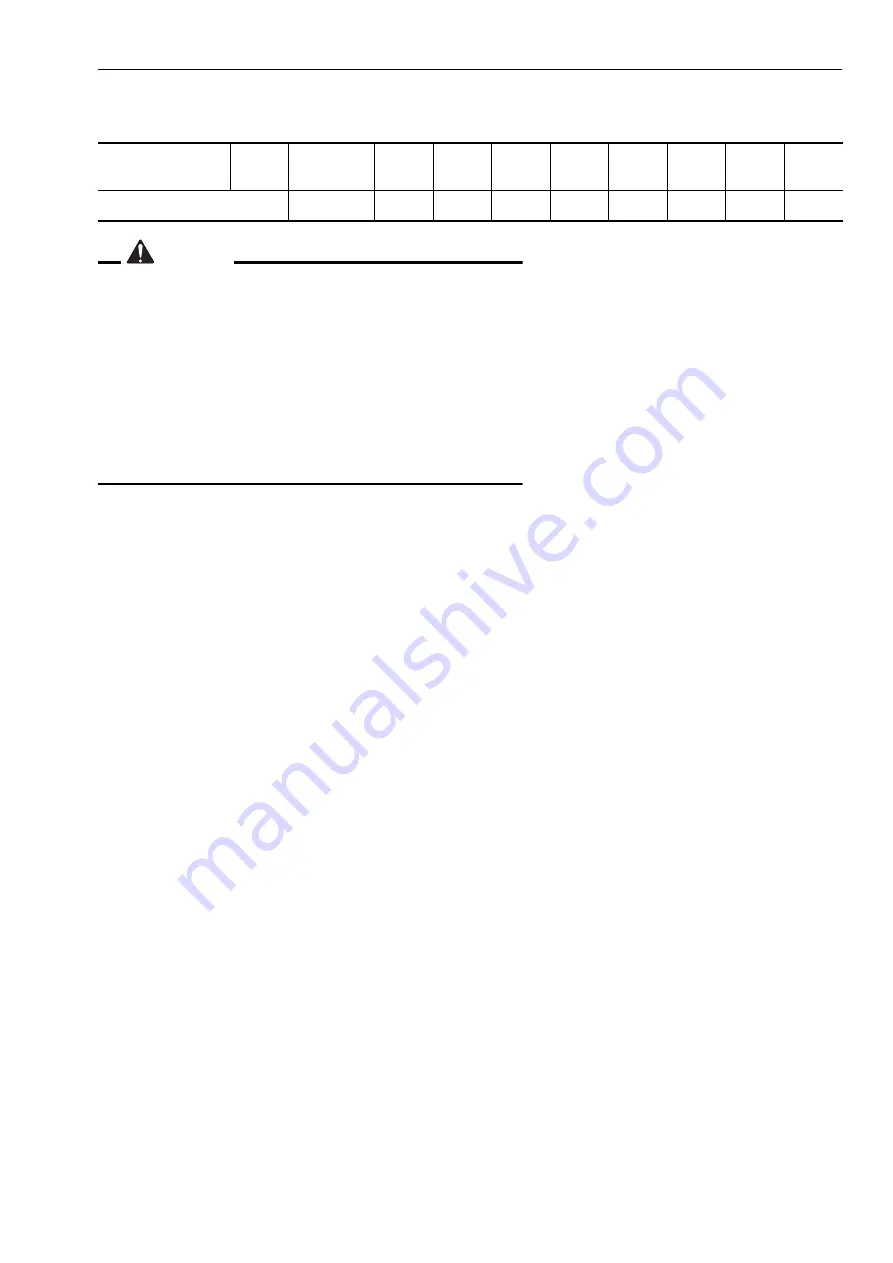
5.8 Maintenance procedure
Maintenance
Corrective maintenance
WA80M-7, WA100M-7 – VENAM03001
5-33
Coolant density table
WARNING
Coolant is toxic. When you open the drain valve, make sure
you do not get any coolant on your body. If it gets into your
eyes, rinse your eyes with a large volume of fresh water and
seek medical assistance immediately.
Please contact your Komatsu distributor when you are chang-
ing the coolant or processing the cooling water containing
coolant which has been drained in the course of repairing the
radiator; alternatively, have this work done by a specialist
company. Coolant is toxic. Do not let it flow away in drainage
channels, and do not sprinkle it on the ground either.
The amine-free engine coolant (AF-NAC) is already diluted with
distilled water, which makes it nonflammable.
Check the density using a coolant tester.
Place a container ready to collect the drained coolant; the volume
of the container should be larger than the specified volume of
coolant.
Prepare a hose for filling the coolant with.
Minimum ambient
temperature
°C
Above -10
-15
-20
-25
-30
-35
-40
-45
-50
Density (%)
30
36
41
46
50
54
58
61
64
Summary of Contents for WA100M-7
Page 2: ......
Page 3: ...Foreword WA80M 7 WA100M 7 VENAM03001 1 1 1 Foreword...
Page 26: ...1 7 Equipment Foreword 1 24 WA80M 7 WA100M 7 VENAM03001...
Page 71: ...Operation WA80M 7 WA100M 7 VENAM03001 3 1 3 Operation...
Page 184: ...3 8 Reading error code Operation 3 114 WA80M 7 WA100M 7 VENAM03001...
Page 185: ...Troubleshooting WA80M 7 WA100M 7 VENAM03001 4 1 4 Troubleshooting...
Page 203: ...Maintenance WA80M 7 WA100M 7 VENAM03001 5 1 5 Maintenance...
Page 220: ...5 4 Fuel lubricants and coolants quantities Maintenance 5 18 WA80M 7 WA100M 7 VENAM03001...
Page 279: ...Technical data WA80M 7 WA100M 7 VENAM03001 6 1 6 Technical data...
Page 285: ...Special equipment attachments WA80M 7 WA100M 7 VENAM03001 7 1 7 Special equipment attachments...
Page 292: ...7 3 Central lubrication system Special equipment attachments 7 8 WA80M 7 WA100M 7 VENAM03001...
Page 293: ...Index WA80M 7 WA100M 7 VENAM03001 8 1 8 Index...
Page 298: ...8 1 Index Index 8 6 WA80M 7 WA100M 7 VENAM03001...
Page 299: ...Notes WA80M 7 WA100M 7 VENAM03001 9 1 9 Notes...
Page 300: ...Notes 9 2 WA80M 7 WA100M 7 VENAM03001...
Page 301: ...Notes WA80M 7 WA100M 7 VENAM03001 9 3...
Page 302: ...Notes 9 4 WA80M 7 WA100M 7 VENAM03001...