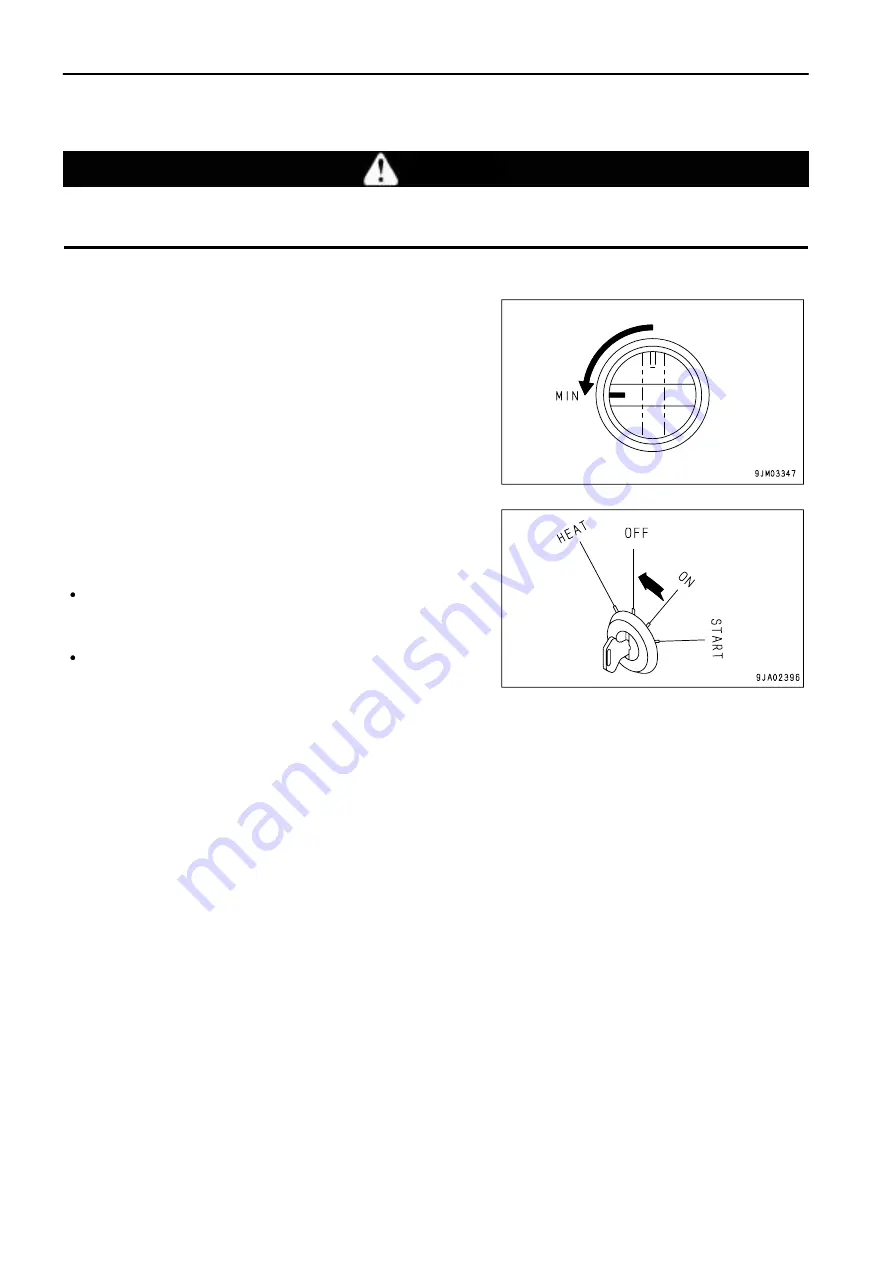
.
OPERATION
OPERATION
STOPPING ENGINE
WARNING
Do not stop the engine suddenly except in case of emergency, before it cools down. Otherwise durability of the engine
components may be shortened. Sudden stop of the engine should be limited only to a case emergency.
Let the engine cool down gradually after the work and stop it thereafter.
1. Turn the fuel control dial to the low idling (MIN) position.
2. Run the engine at low idling for about 5 minutes to cool down
gradually.
3. Turn the starting switch key back to the OFF position, stop the
engine and pull out the key.
REMARK
When the engine is overheated, do not stop it on the spot, but
allow it to cool down gradually while running at a medium speed,
and then stop it.
If it is required to start the engine again, start it after approx. 30
seconds.
CHECK AFTER STOPPING ENGINE
1. Walk around the undercarriage, crusher, belt conveyor and machine covers to check for oil and water leakage.
If any leakage or abnormality is found, fix it.
2. Fill the fuel tank.
3. Check the engine compartment for paper and debris. Clean out any paper and debris to avoid a fire hazard.
4. Remove any mud affixed to the undercarriage.
3 - 54
https://tractormanualz.com
Summary of Contents for GALEO BR550JG-1
Page 1: ...https tractormanualz com...
Page 2: ...1 1 https tractormanualz com...
Page 4: ...FOREWORD FOREWORD 1 3 https tractormanualz com...
Page 5: ...FOREWORD FOREWORD 1 4 https tractormanualz com...
Page 14: ...2 1 https tractormanualz com...
Page 19: ...SAFETY SAFETY LABELS POSITIONS OF SAFETY PICTOGRAMS 2 6 https tractormanualz com...
Page 50: ...3 1 https tractormanualz com...
Page 93: ...OPERATION OPERATION CHECK OF JAW CRUSHER AND RELATED ACCESSORIES 3 44 https tractormanualz com...
Page 117: ...OPERATION OPERATION UNIT OPERATOR S POSITION AT WORKSITE 3 68 https tractormanualz com...
Page 145: ...OPERATION TRANSPORTATION 3 96 https tractormanualz com...
Page 171: ...4 1 https tractormanualz com...
Page 181: ...MAINTENANCE WEAR PARTS 4 11 https tractormanualz com...
Page 183: ...MAINTENANCE WEAR PARTS 4 13 https tractormanualz com...
Page 189: ...MAINTENANCE STANDARD TIGHTENING TORQUES FOR BOLTS AND NUTS 4 19 https tractormanualz com...
Page 256: ...5 1 https tractormanualz com...
Page 258: ...SPECIFICATIONS SPECIFICATIONS 5 3 https tractormanualz com...
Page 259: ...6 1 https tractormanualz com...
Page 275: ...ATTACHMENTS OPTIONS MUCK DISCHARGE CONVEYOR 6 17 https tractormanualz com...