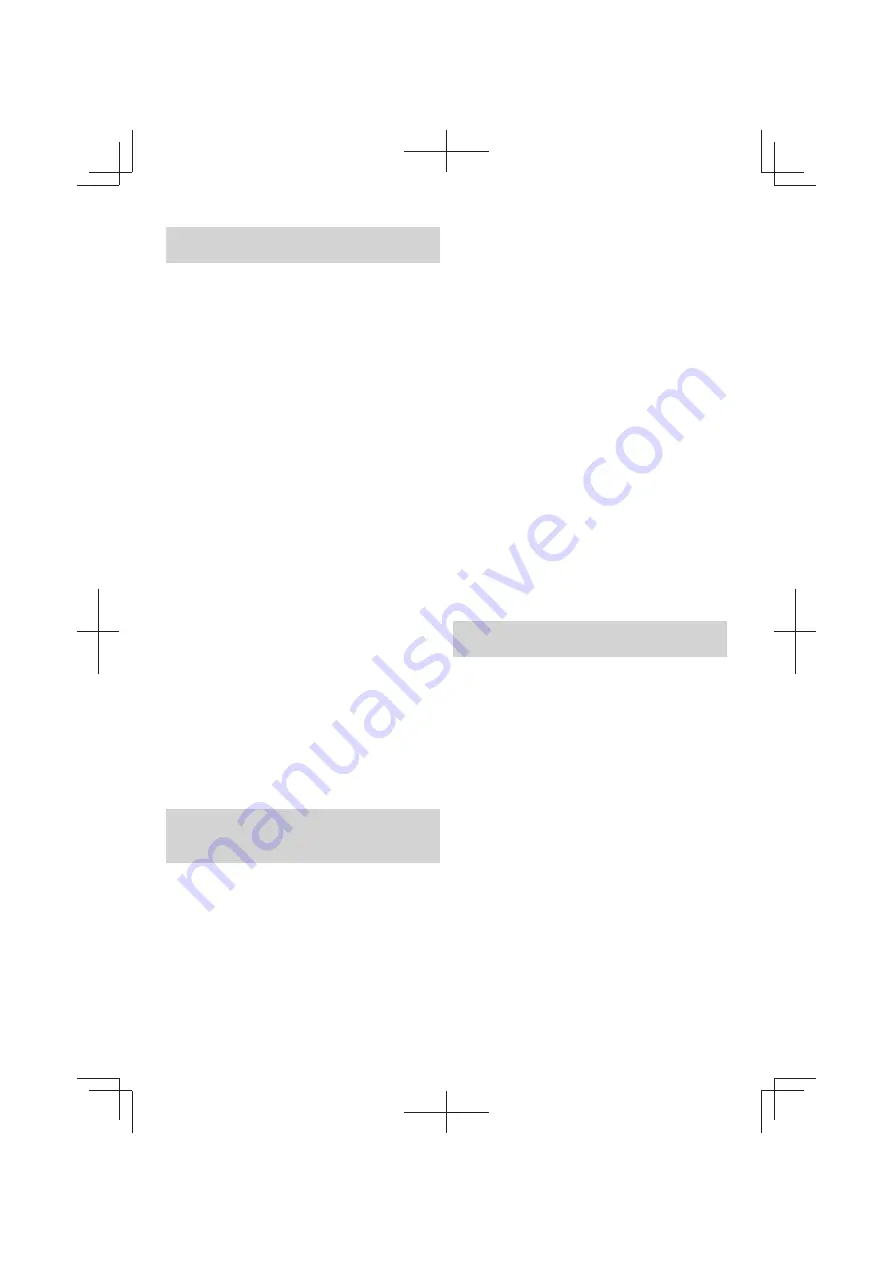
7
KICKBACK AND RELATED
WARNINGS
Kickback is a sudden reaction to a pinched or snagged
rotating wheel, backing pad, brush or any other accessory.
Pinching or snagging causes rapid stalling of the rotating
accessory which in turn causes the uncontrolled power tool
to be forced in the direction opposite of the accessory’s
rotation at the point of the binding.
For example, if an abrasive wheel is snagged or pinched by
the workpiece, the edge of the wheel that is entering into the
pinch point can dig into the surface of the material causing
the wheel to climb out or kick out. The wheel may either jump
toward or away from the operator, depending on direction of
the wheel’s movement at the point of pinching.
Abrasive wheels may also break under these conditions.
Kickback is the result of power tool misuse and/or incorrect
operating procedures or conditions and can be avoided by
taking proper precautions as given below.
a) Maintain a
fi
rm grip on the power tool and position
your body and arm to allow you to resist kickback
forces.
The operator can control kickback forces, if proper
precautions are taken.
b) Use special care when working corners, sharp
edges etc. Avoid bouncing and snagging the
accessory.
Corners, sharp edges or bouncing have a tendency to
snag the rotating accessory and cause loss of control or
kickback.
c) Do not attach a toothed saw blade.
Such blades create frequent kickback and loss of
control.
d) Always feed the bit into the material in the same
direction as the cutting edge is exiting from the
material (which is the same direction as the chips
are thrown).
Feeding the tool in the wrong direction causes the cutting
edge of the bit to climb out of the work and pull the tool in
the direction of this feed.
e) When using rotary
fi
les, cut-o
ff
wheels, high-speed
cutters or tungsten carbide cutters, always have
the work securely clamped.
These wheels will grab if they become slightly canted
in the groove, and can kickback. When a cut-o
ff
wheel
grabs, the wheel itself usually breaks. When a rotary
fi
le,
high-speed cutter or tungsten carbide cutter grabs, it
may jump from the groove and you could lose control of
the tool.
SAFETY WARNINGS SPECIFIC FOR
GRINDING AND ABRASIVE CUTTING-
OFF OPERATIONS
a) Use only wheel types that are recommended
for your power tool and only for recommended
applications. For example: do not grind with the
side of a cut-o
ff
wheel.
Abrasive
cut-o
ff
wheels are intended for peripheral
grinding, side forces applied to these wheels may cause
them to shatter.
b) For threaded abrasive cones and plugs use only
undamaged wheel mandrels with an unrelieved
shoulder
fl
ange that are of correct size and length.
Proper mandrels will reduce the possibility of breakage.
c) Do not “jam” a cut-o
ff
wheel or apply excessive
pressure. Do not attempt to make an excessive
depth of cut.
Overstressing the wheel increases the loading and
susceptibility to twisting or snagging of the wheel in the
cut and the possibility of kickback or wheel breakage.
d) Do not position your hand in line with and behind
the rotating wheel.
When the wheel, at the point of operation, is moving
away from your hand, the possible kickback may propel
the spinning wheel and the power tool directly at you.
e) When wheel is pinched, snagged or when
interrupting a cut for any reason, switch o
ff
the
power tool and hold the power tool motionless until
the wheel comes to a complete stop. Never attempt
to remove the cut-o
ff
wheel from the cut while the
wheel is in motion otherwise kickback may occur.
Investigate and take corrective action to eliminate the
cause of wheel pinching or snagging.
f) Do not restart the cutting operation in the workpiece.
Let the wheel reach full speed and carefully re-enter
the cut.
The wheel may bind, walk up or kickback if the power
tool is restarted in the workpiece.
g) Support panels or any oversized workpiece to
minimize the risk of wheel pinching and kickback.
Large workpieces tend to sag under their own weight.
Supports must be placed under the workpiece near the
line of cut and near the edge of the workpiece on both
sides of the wheel.
h) Use extra caution when making a “pocket cut” into
existing walls or other blind areas.
The protruding wheel may cut gas or water pipes,
electrical wiring or objects that can cause kickback.
GENERAL SAFETY INSTRUCTIONS
FOR CORDLESS GRINDER
– Check that speed marked on the wheel is equal to or
greater than the rated speed of the grinder;
– Ensure that the wheel dimensions are compatible with
the grinder;
– Abrasive wheels shall be stored and handled with care in
accordance with manufacturer’s instructions;
– Inspect the grinding wheel before use, do not use
chipped, cracked or otherwise defective products;
– Ensure that mounted wheels and points are
fi
tted in
accordance with the manufacturer’s instructions;
– Ensure that blotters are used when they are provided
with the bonded abrasive product and when they are
required;
– Ensure that the abrasive product is correctly mounted
and tightened before use and run the tool at no-load for
30 seconds in a safe position, stop immediately if there
is considerable vibration or if other defects are detected.
If this condition occurs, check the machine to determine
the cause;
– If a guard is equipped with the tool never use the tool
without such a guard;
– Do not use separate reducing bushings or adapters to
adapt large hole abrasive wheels;
– For tools intended to be
fi
tted with threaded hole wheel,
ensure that the thread in the wheel is long enough to
accept the spindle length;
– Check that the work piece is properly supported;
– Do not use cutting o
ff
wheel for side grinding;
– Ensure that sparks resulting from use do not create
a hazard e.g. do not hit persons, or ignite
fl
ammable
substances;
00Book̲GP18DA̲UK.indb 7
00Book̲GP18DA̲UK.indb 7
2021/03/04 15:38:10
2021/03/04 15:38:10
Summary of Contents for Hikoki GP 18DA
Page 18: ...18 00Book GP18DA UK indb 18 00Book GP18DA UK indb 18 2021 03 04 15 38 12 2021 03 04 15 38 12 ...
Page 20: ...20 00Book GP18DA UK indb 20 00Book GP18DA UK indb 20 2021 03 04 15 38 14 2021 03 04 15 38 14 ...
Page 22: ...22 00Book GP18DA UK indb 22 00Book GP18DA UK indb 22 2021 03 04 15 38 14 2021 03 04 15 38 14 ...
Page 23: ...23 00Book GP18DA UK indb 23 00Book GP18DA UK indb 23 2021 03 04 15 38 14 2021 03 04 15 38 14 ...