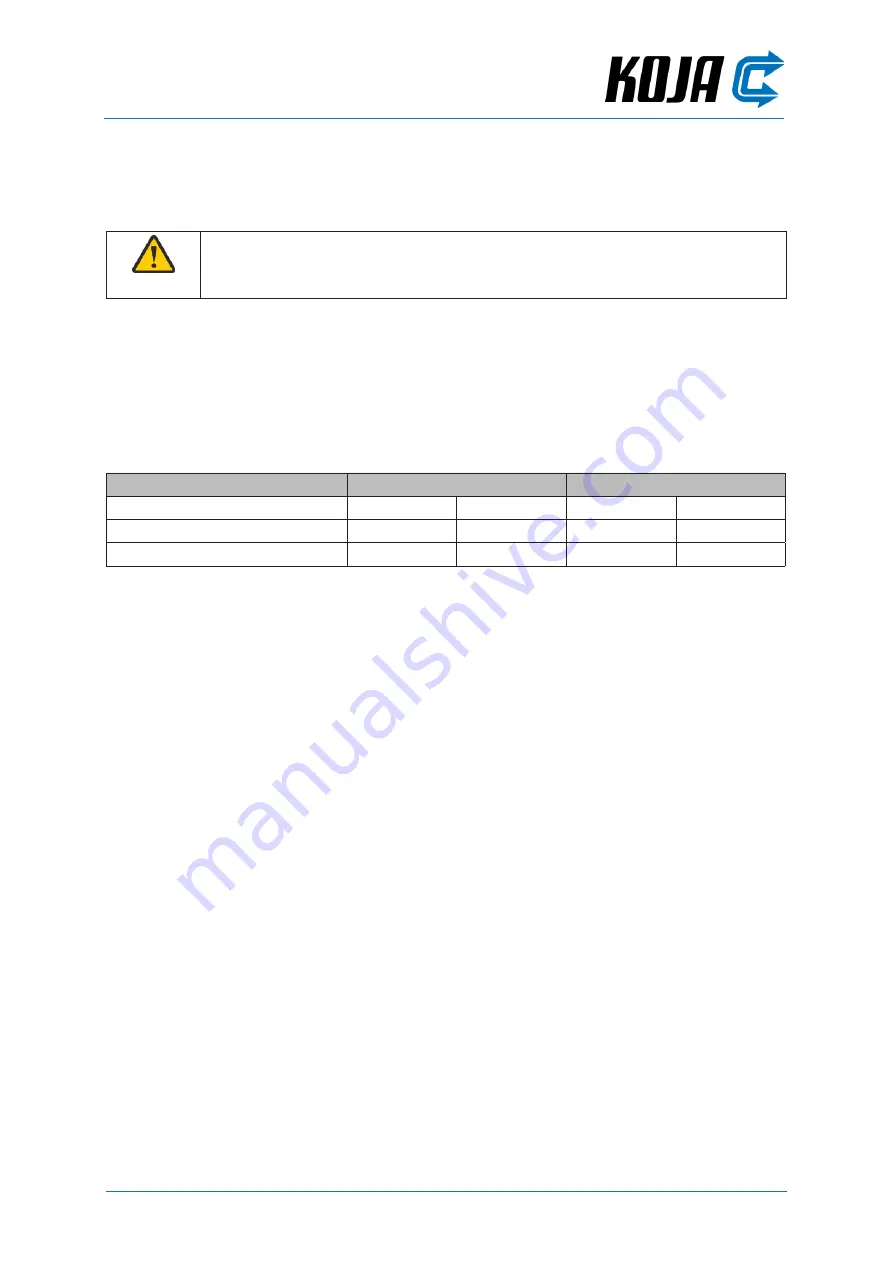
AIR HANDLING UNIT FUTURE
INSTRUCTIONS FOR OPERATION AND MAINTENANCE
Fan section, motors and frequency converters
2017-02-13
V. 2.0
39
phases on either the motor or frequency converter end. Before this, you must switch off the power supply, lock
the motor axle and allow the frequency converter voltage to discharge.
12.4. EC motors
WARNING
An EC motor rotating freely generates voltage to the internal motor connections. These
voltages can be dangerously high. After the motor has stopped, wait at least five minutes
to allow dangerous voltages to discharge.
The EC motors have an integrated control unit. EMC requirements do not apply to the EC motor power cabling.
Nevertheless, it is advisable to use screened cable control wires. The bus conductors must be screened and of
the twisted pair type. Any control cable screens are connected on the EC motor end only. The supply cable must
be equipped with a service switch. The equipment must be protected against short circuits and the installations
against overloading with, for example, fuses.
Koja offers fans equipped with EC motors from EBM Papst / Fläkt Woods and Ziehl Abegg. The connections vary
between the manufacturers, and also depend on the number of control unit phases. See the table below for EC
motor information.
EC motor
EBM / Fläkt
Ziehl
Supply voltage
AC 1 x 230 V
AC 3 x 400 V
AC 1 x 230 V
AC 3 x 400 V
Ambient temperature during use
–25…40 ˚C
–25…40 ˚C
–25…60 ˚C
–35…60 ˚C
Protection class
IP44
IP54
IP54
IP54
If not specifically prevented, the EC motor may start automatically after a malfunction. This may happen, for
example, if the set point is saved on the fan memory.
The EC motor control unit parameters and the operation of the control connectors can be changed via the Mod
-
bus bus. Refer to the fan manufacturer’s instructions for more information about the parameter changing and
how it affects the operation of the fan. With factory settings, the rotating speed of the motor is controlled with
a 0…10 V signal. The motors start when they receive the enable device input and the voltage control is approx.
1…1.5 V. When the motor is rotating, it can be controlled with a voltage of approx. 1 V at minimum. With facto
-
ry settings, control voltage of 10 V corresponds a 100 per cent rotating speed.
In case of failure or malfunction, the integrated control unit stops the motor.
The operating voltage of the EC motor varies depending on the power of the motor. The operating voltage must
be the same as that stated on the nameplate.
12.5. Connection of the EBM / Fläkt EC motor
The connection of the three- and one-phase EBM Papst EC motor is described in the figure
EC motor
. In both
cases, the speed set point is delivered between the connectors GND and Ain1/U. The speed set point can also
be generated using the motor’s own 10 V output. The motor starts, when the speed set point voltage exceeds
1.4 V.
There is no separate enable device input; the control unit is allowed to start when the control voltage exceed
one volt. A voltage signal must be used to control the motor on and off. On/off control must not be done using
the supply voltage, which must be kept switched on at all times.
Alarm data is received from the motor via a potential-free contact, the maximum load of which at alternating
voltage is 250 V / 2 A.
Summary of Contents for 0603
Page 1: ...Instructions for operation and maintenance www koja fi Air handling unit Future...
Page 2: ......
Page 50: ......
Page 51: ......