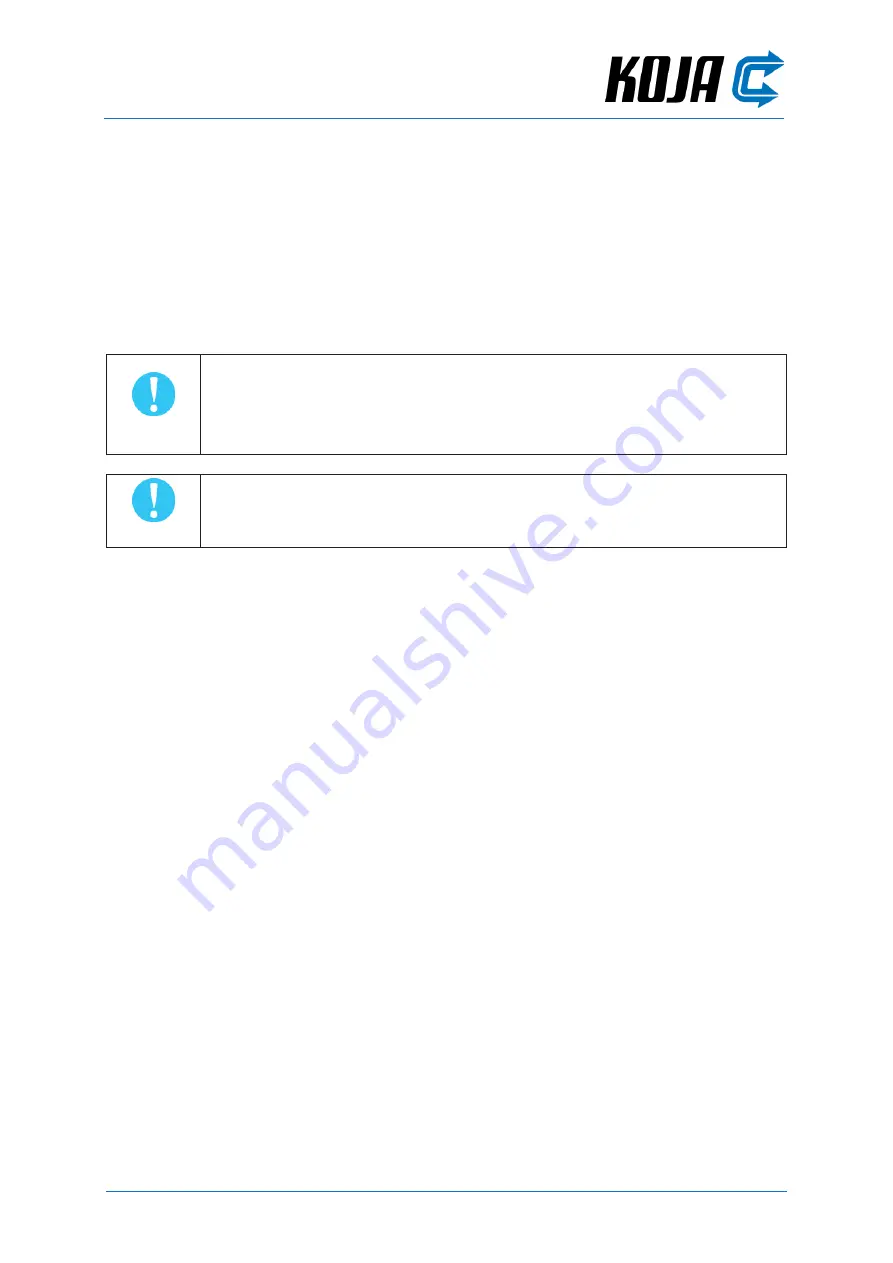
AIR HANDLING UNIT FUTURE
INSTRUCTIONS FOR OPERATION AND MAINTENANCE
Coil sections
2017-02-13
V. 2.0
19
5.5.
Maintenance
•
Make sure that the water side connections of the coil do not leak.
•
Make sure that the heat transfer surfaces of the coil are clean and intact.
•
Clean the coil gently with a brush, compressed air or a vacuum cleaner. If the unit has water drains, the
coil can be cleaned with water and a mild detergent.
NOTE! Do not use pressure cleaning.
•
Bleed the coil and check the operation of the anti-freezing thermostat at the beginning of each heating
season.
•
Check and clean the condensation water discharge system, i.e., drip tray, piping and water trap (traps).
•
A damaged coil must be repaired in place, sent to the manufacturer to be repaired or replaced.
CAUTION
If the coil is not used during the heating season, water must be drained from it or it has to
be filled with a water-glycol mixture to avoid freezing. The coil does not drain fully through
the drain screw; 20 to 30% of the total water volume remains in the coil. To fully drain
water from the coil, you can, for example, blow compressed air through the bleed screw,
observing the maximum permissible operating pressure.
CAUTION
The HR circuit must be bled again after 2–4 weeks of heating in order for the energy
efficiency in heat recovery to be the best possible.
Summary of Contents for 0603
Page 1: ...Instructions for operation and maintenance www koja fi Air handling unit Future...
Page 2: ......
Page 50: ......
Page 51: ......