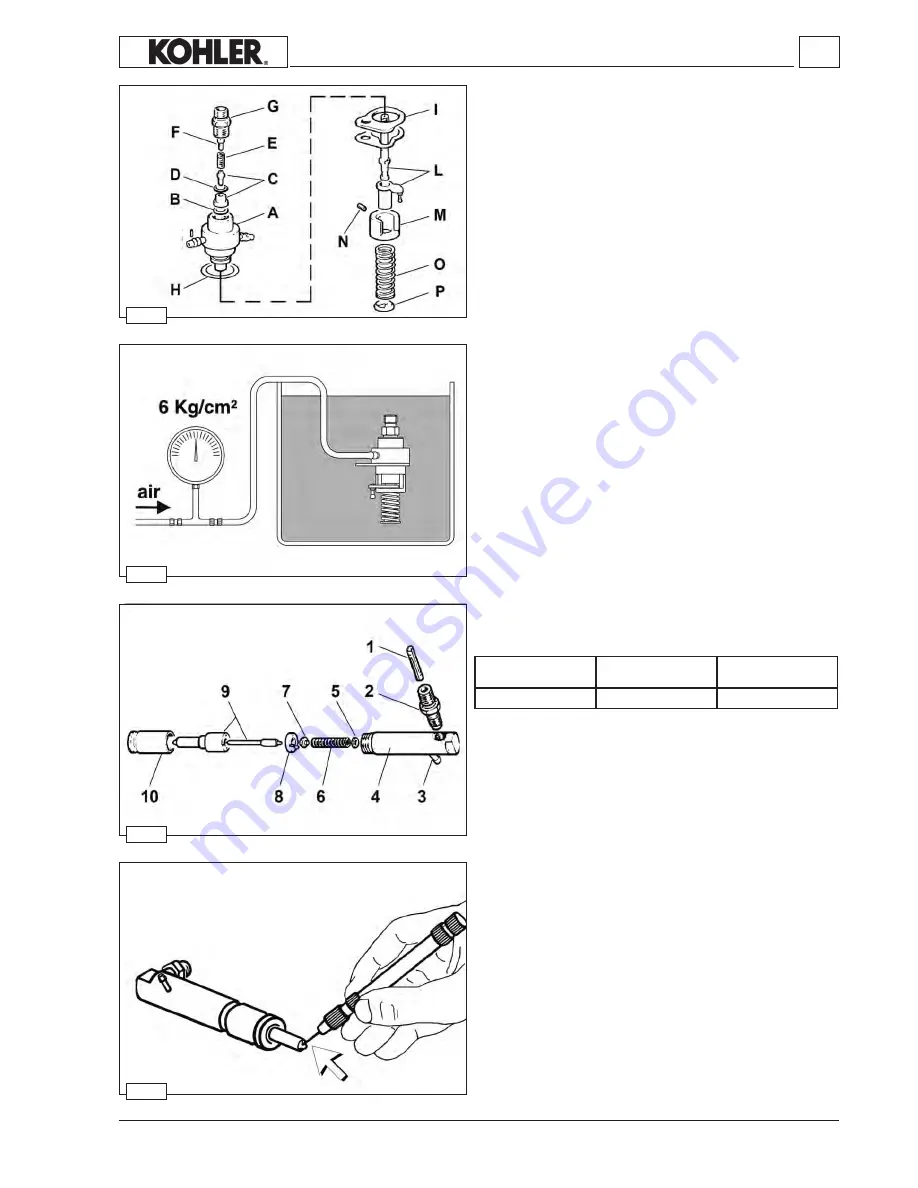
- 27 -
- 27 -
39
38
37
36
11
0,24
5
0,25
Injection equipment
5.
Insert the adjuster sleeve unit and plunger (
L
) into the pump
casing (
A
), making sure that the helical profile is directed on a
level with the return union with ball.
6.
Fit in the adjuster block (
M
), matching the reference marks
applied during the demounting phase.
7.
Tighten the plug (
N
) to a 0.5 to 0.6 Nm torque, locking it in
place with Loctite 290.
8.
Insert the spring (
O
) and lower cap (
P
).
9.
Compress the tappets in the various operating positions to
check that the adjuster sleeve (
L
) slides perfectly. Resistance
or jamming will make the engine to hunt during operation.
Leak test
Plug the fuel return union and let air in through the fuelling
union at a pressure of
6 Kg/cm²
. Fully immerse the pump in a
receptacle containing diesel fuel for about 50 - 60 seconds (fig.
37) and make sure that no bubbles appear.
NOTE: the position of the pump adjuster sleeve is of no
importance for this test.
Injector
Details of fig. 38:
1.
Filter -
2.
Fuel inlet union -
3.
Fuel return union -
4.
Nozzle
holder -
5.
Calibration washer -
6.
Spring -
7.
Pressure rod -
8.
Spacer -
9.
Nozzle -
10.
Ring nut.
Injector inspection and calibration
1.
Clean the nozzle holes with a thin steel wire (fig. 39) with the
following diameters:
2.
Mount the injector on the test bench (code
00365R0430
, fig.
40).
Disconnect the pressure gauge and rapidly operate the lever.
The nozzle must make the characteristic "trilling" sound and
inject with a good atomizing action.
3.
Connect the pressure gauge. Slowly depress the level in a
continuous way until injection occurs.
The injector needle must "open" at the pressure of 230 to 238
bar. Vary the washer shims (N°
5
fig. 38) to calibrate in the
correct way.
4.
Leak test:
operate the test bench lever until the gauge pointer
is 20 Kg/cm² below the injection pressure value. Nozzle
tightness is good if no fuel comes out within 10 sec.
5.
Checking for leaks on the nozzle return phase:
operate the
test bench lever until the gauge pointer is 20 Kg/cm² below
the injection pressure value. Release the lever and
Diameter of steel
wire (mm)
Number
of holes
Diameter
of holes (mm)
Workshop Manual KD500 _ cod. ED0053029390 -
1° ed
_rev.
00