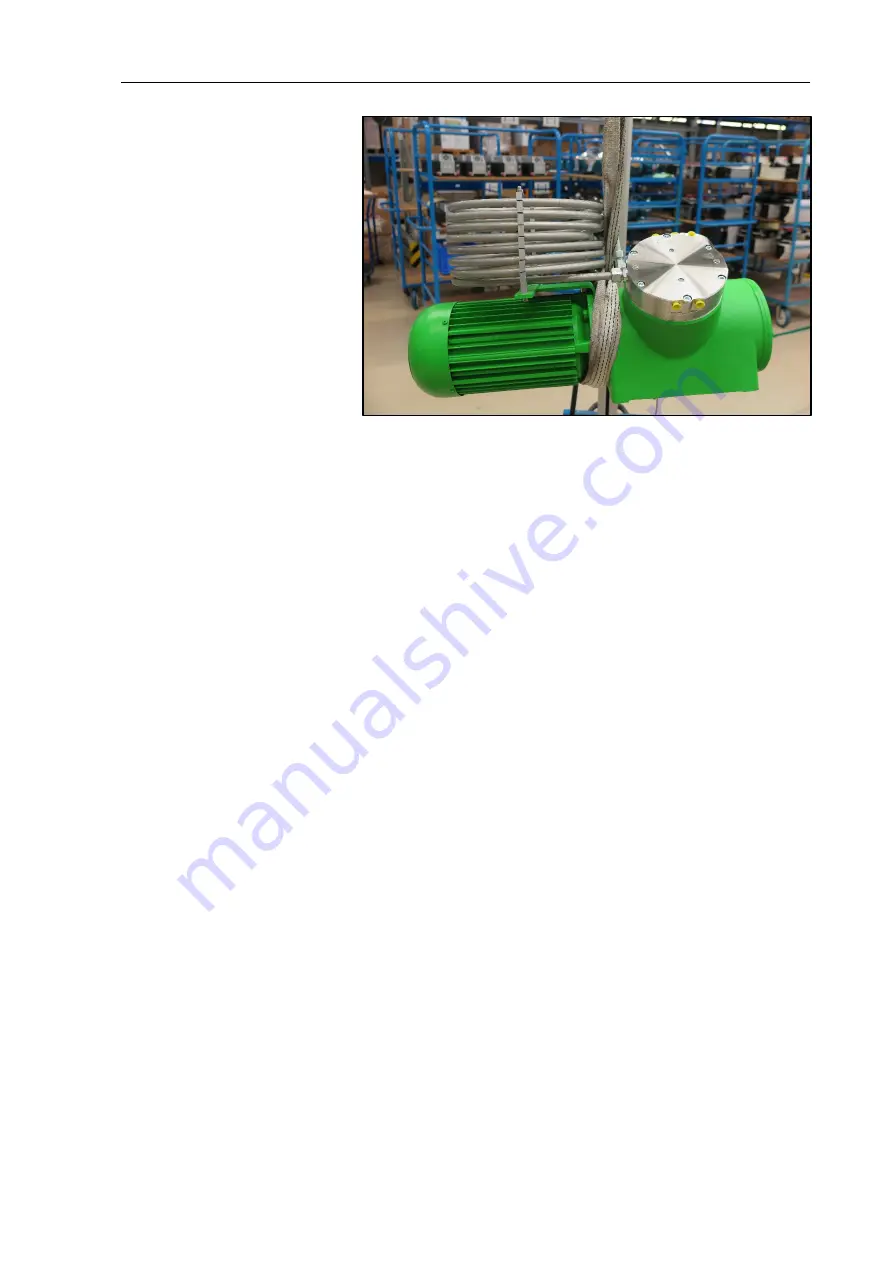
Diaphragm pump N 2400.15
Transportation
Translation of original Operating and Installation Instructions, english, KNF 308934-308937 09/18
17
Fig. 5:
2. Fix the harness between compressor housing and motor (Fig.
5).
3. Make sure that the lifting load cannot be transferred from the
belt to the pump connection.
4. Use a lifting device to lift the pump out of the packaging.
5. Place the pump carefully at the installation location.
Summary of Contents for N 2400.15
Page 38: ......
Page 39: ......
Page 40: ...KNF worldwide Find your local KNF partner on www knf com...