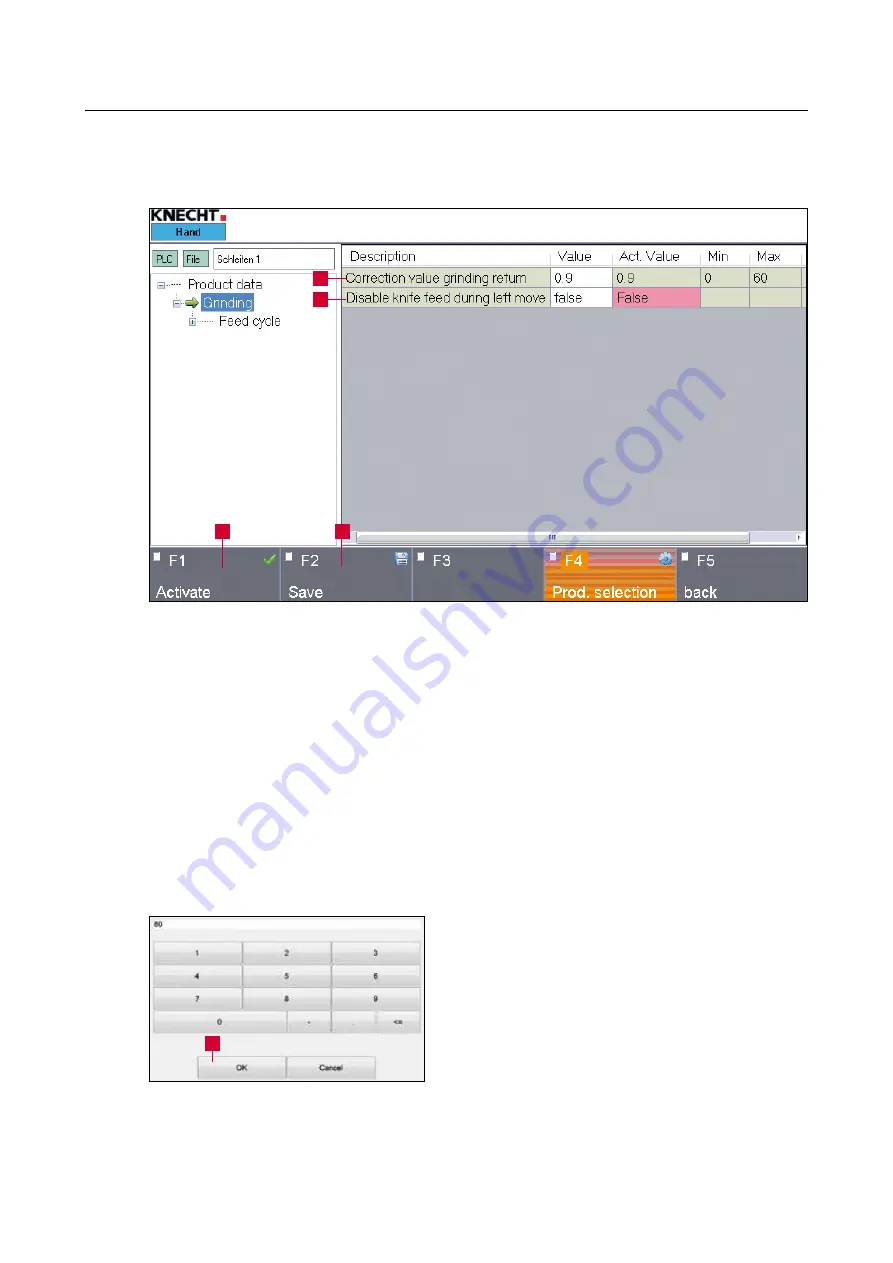
48
8. Control
8.4.1 Meaning of the “Grind” parameter
1
“Correction value grinding return”: The positioning time of the cycle times will be added
up and provides the basis for the return time. In order to compensate for imprecision, a
correction value on the return time for return runs is entered when changing segments.
The correction value is added to the total lead time.
2
“Disable knife feed during left move”: true = reset knife feed disabled, false = reset knife
feed enabled
To change the parameter, tap on the respective field highlighted in yellow. The window (8-13)
opens for “Number”, the window (8-14) for “Values”.
Select the desired number and confirm with “OK”
(8-13/1).
The touch panel field “Cancel” closes the window
without recording the number.
Figure 8-12
“Grinding” parameter
1
2
3
4
Figure 8-13
Editing “Number” parameter
1