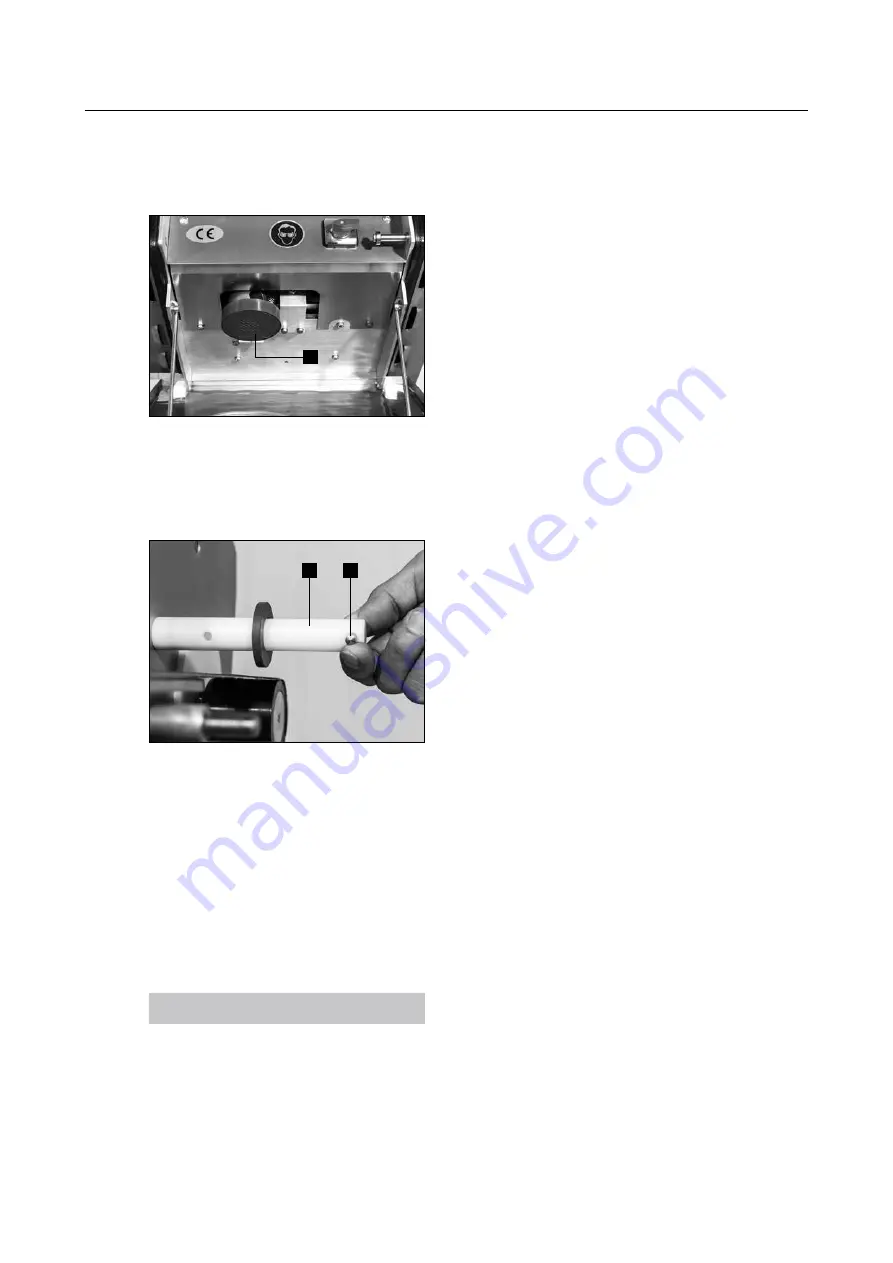
35
7.10 Coolant unit
In the USK 160 S, the coolant is supplied through
continuous circulation around the grinding wheel
using a submersible pump (7-14/1).
The abrasives are not immersed in water while the
machine is idle. The grinding sludge is collected in
the water tray.
The submersible pump is driven by the motor via a
circular belt.
7.10.1 Belt cooling
The submersible pump feeds the coolant through
the water nozzle to the wet-grinding belt.
Coolant is apportioned by the swiveling of the
water nozzle.
In doing so, the flow rate of the coolant does not
change, rather the impact angle on the grinding
belt.
The pin (7-15/1) on the water nozzle (7-15/2) indi-
cates the angle at which the coolant will hit.
The standard setting is perpendicularly down-
wards.
Turning clockwise = more coolant
Turning counterclockwise = less coolant
For cleaning, the water nozzle is simply pulled out
after removing the protection hood.
NOTICE
Opposed to the belt side, for which as much
coolant should be applied to the wet-grind-
ing belt, the finned grinding wheel or serra-
tion grinding wheel must receive more subtle
doses.
7. Operation
Figure 7-14
Submersible pump
Figure 7-15
Adjusting the water nozzle
1
2
1
Summary of Contents for USK 160 S
Page 2: ...2 ...