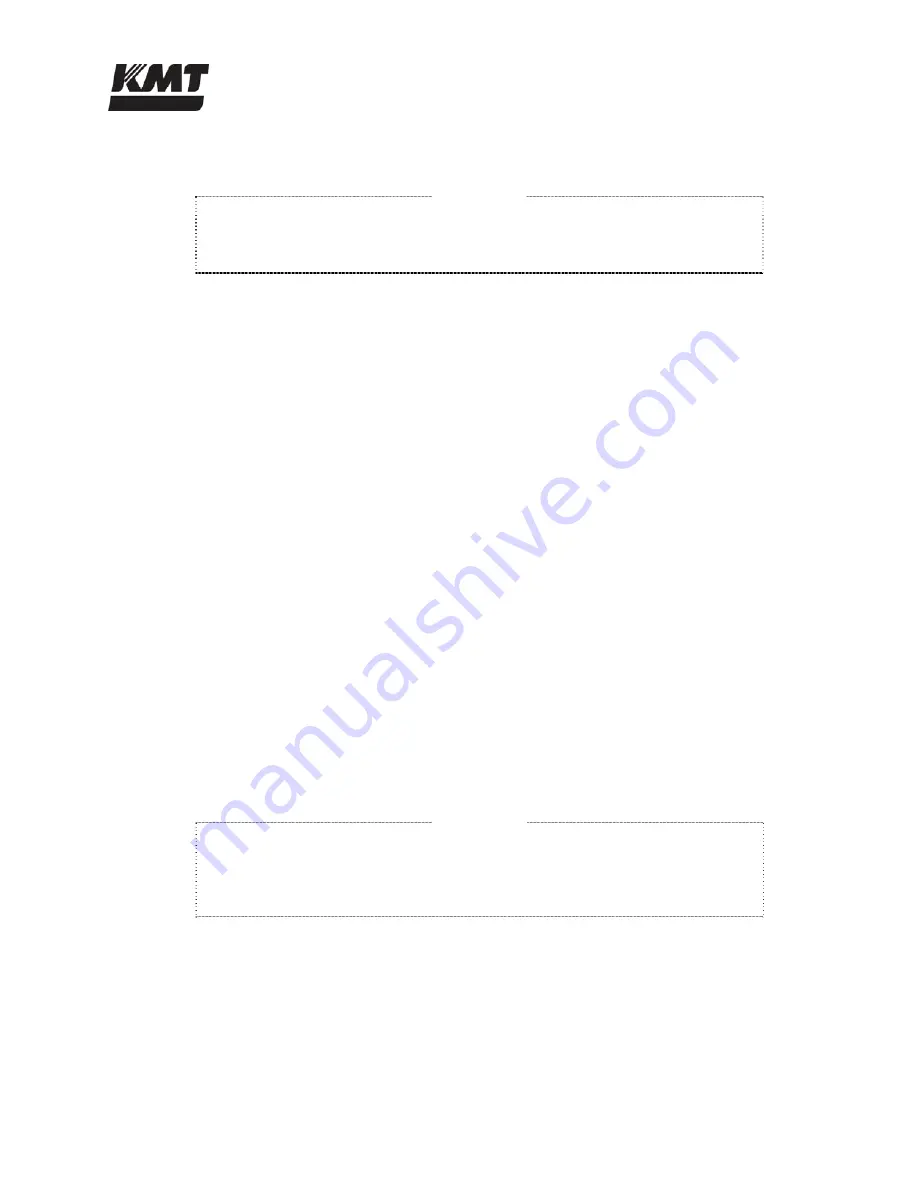
Section 8
High Pressure Water System
20479291
2-2012/Rev 04
8-26
5.
Inspect the plunger button sockets for unusual wear.
NOTE
Due to the high contact force between the piston and the plunger, the plunger may
make an impression in the bottom of the socket. This compression mark or
indentation is normal.
6.
Apply FML-2 grease to new plunger button backup rings and o-rings. Install the rings in
the internal groove in the plunger socket. If the backup ring is not installed the plunger
can be forced out of the plunger socket.
7.
Install the retainer pins, verifying that each pin moves freely without excess side play in
the pin holes.
8.
Install the flat snap ring over the pins.
9.
Install the plungers and check the snap-in feature of the plunger attachment. Use the
plunger removal tool to ensure the pins retract to release the plunger, and close to retain
the plunger in a uniform manner.
Internal Check Valves
It is not necessary to service the internal check valves unless a problem is suspected. If the check
valves or the internal passages in the piston require service, plunger button, seal and pin servicing
is also recommended. See Figure 8-21, Hydraulic Piston.
1.
Loosen the set screw and remove the check valves and o-rings. Clean the internal
passages.
2.
Apply FML-2 grease to a new o-ring and install the new o-ring in the check valve
passage. Use a blunt, pencil-like instrument to position it in the bottom of the passage.
3.
Clean and install a new check valve with the chamfered end toward the o-ring.
4.
Sparingly apply Loctite, threadlocker adhesive to the set screw. Thread the screw over the
check valve cartridge and tighten.
NOTE
Excess threadlocker adhesive can clog the check valve or block the internal
passage. To avoid excess adhesive, position the set screw on an Allen wrench and
apply the adhesive. Hold the screw horizontal on a paper towel and rotate the
screw to remove excess adhesive.
Hydraulic Piston Installation
1.
Ensure the hydraulic cylinder bore is free of grit or contamination.
2.
Lubricate the bearing rings and seal assembly, and lightly lubricate 2-3 inches of the
cylinder bore with FML-2 grease.
Summary of Contents for STREAMLINE S50
Page 1: ...MANUAL 20479050 R04 STREAMLINE S50 WATERJET INTENSIFIER OPERATION AND MAINTENANCE MANUAL ...
Page 20: ......
Page 22: ......
Page 125: ...Section 11 Parts List 20479307 2 2012 Rev 04 11 4 Figure 11 1 Streamline S50 Intensifier Unit ...
Page 127: ...Section 11 Parts List 20479307 2 2012 Rev 04 11 6 Figure 11 2 Intensifier Assembly ...
Page 131: ...Section 11 Parts List 20479307 2 2012 Rev 04 11 10 Figure 11 5 Hydraulic Piston Assembly ...
Page 133: ...Section 11 Parts List 20479307 2 2012 Rev 04 11 12 Figure 11 6 High Pressure Piping ...
Page 135: ...Section 11 Parts List 20479307 2 2012 Rev 04 11 14 Figure 11 7 Hydraulic Power Package ...
Page 137: ...Section 11 Parts List 20479307 2 2012 Rev 04 11 16 Figure 11 8 Motor Pump Assembly ...
Page 139: ...Section 11 Parts List 20479307 2 2012 Rev 04 11 18 Figure 11 9 Hydraulic Manifold Assembly ...
Page 141: ...Section 11 Parts List 20479307 2 2012 Rev 04 11 20 Figure 11 10 Hydraulic Hose Connections ...
Page 143: ...Section 11 Parts List 20479307 2 2012 Rev 04 11 22 Figure 11 11 Reservoir Assembly ...
Page 145: ...Section 11 Parts List 20479307 2 2012 Rev 04 11 24 Figure 11 12 Bulkhead Pipe Assembly ...
Page 147: ...Section 11 Parts List 20479307 2 2012 Rev 04 11 26 Figure 11 13 Electrical Assembly ...
Page 149: ...Section 11 Parts List 20479307 2 2012 Rev 04 11 28 Figure 11 14 Junction Box ...
Page 157: ...Section 11 Parts List 20479307 2 2012 Rev 04 11 36 Figure 11 18 Heat Exchanger Kit Oil to Air ...
Page 158: ......
Page 159: ......