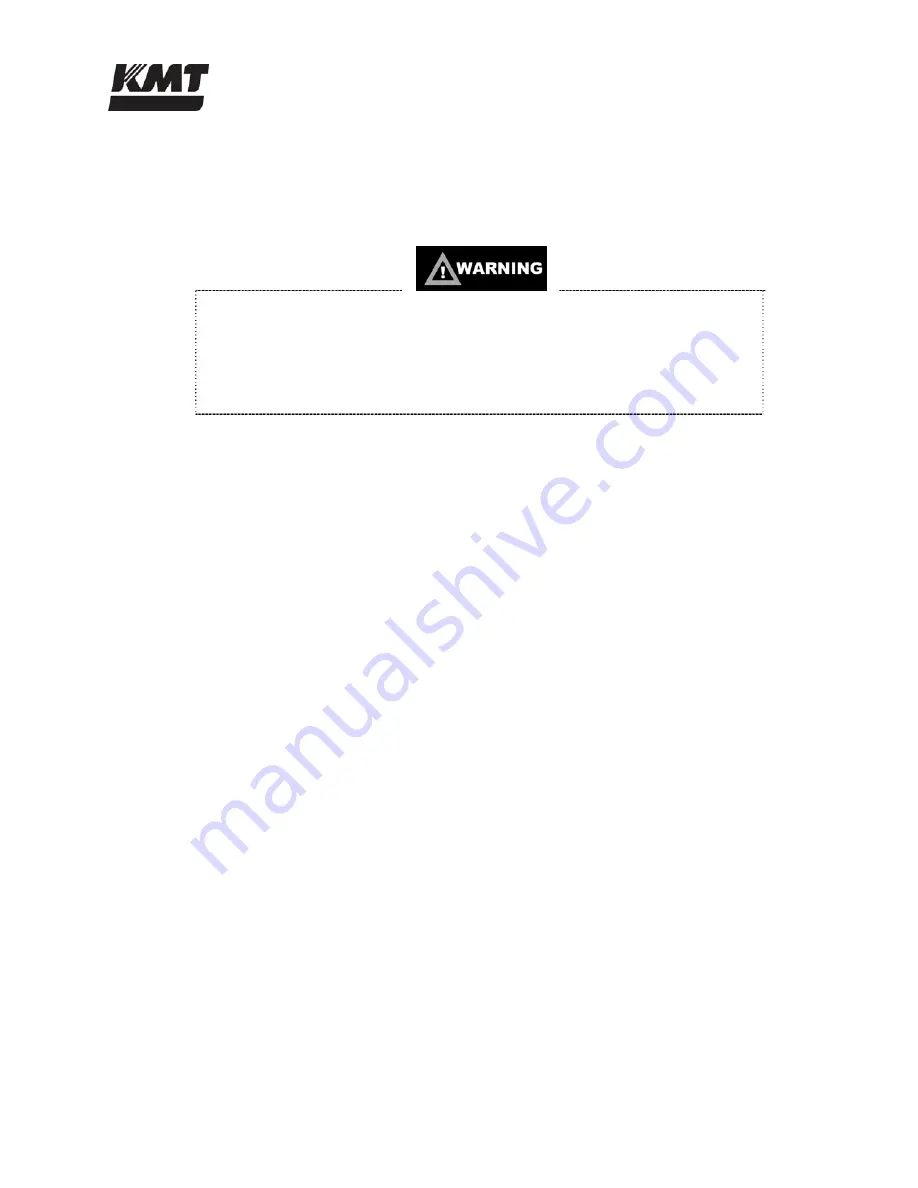
Section 8
High Pressure Water System
20479291
2-2012/Rev 04
8-8
8.5
High and Low Pressure Water Piping
Before performing any maintenance on the high pressure components, it is necessary to remove
the high and low pressure water piping. The following procedure should be used to remove and
install the piping.
Severe injury can result if the machine is not properly locked out. Observe
electrical Lockout/Tagout procedures before performing maintenance on the high
pressure system components.
Ensure all pressure is relieved or blocked from the hydraulic and high pressure
circuits before performing maintenance.
1.
Turn the cutting water supply off.
2.
Loosen and remove the high pressure gland fitting connected to the discharge high
pressure check valve. Move the tubing to clear the work area.
3.
Loosen and remove the low pressure piping connected to the inlet water port on the hard
seal end cap.
4.
When the required maintenance has been completed and the components reassembled,
connect the low pressure water piping to the inlet water port on the hard seal end cap.
5.
Apply Pure Goop to the threads on the high pressure gland fitting. Before installing the
high pressure fitting, ensure proper collar position, 1-1/2 to 2-1/2 threads should be
exposed. Install and tighten the fitting to the torque specifications in Table 8-1.
6.
Turn the cutting water supply on and check for low pressure leaks.
7.
Remove the cutting orifice and start the machine. Operate in low pressure mode to flush
the high pressure passages.
8.
Install the orifice and operate at high pressure to check for leaks.
8.6
High Pressure Cylinder Assembly
KMT Waterjet recommends removing the high pressure cylinder, sealing head and end cap as an
assembly for servicing the plunger, high pressure seals, hydraulic piston and seal cartridge.
Removing the jackbolts in the hard seal end cap is not recommended except to service the inlet
check valve and cone seat on the sealing head.
Summary of Contents for STREAMLINE S50
Page 1: ...MANUAL 20479050 R04 STREAMLINE S50 WATERJET INTENSIFIER OPERATION AND MAINTENANCE MANUAL ...
Page 20: ......
Page 22: ......
Page 125: ...Section 11 Parts List 20479307 2 2012 Rev 04 11 4 Figure 11 1 Streamline S50 Intensifier Unit ...
Page 127: ...Section 11 Parts List 20479307 2 2012 Rev 04 11 6 Figure 11 2 Intensifier Assembly ...
Page 131: ...Section 11 Parts List 20479307 2 2012 Rev 04 11 10 Figure 11 5 Hydraulic Piston Assembly ...
Page 133: ...Section 11 Parts List 20479307 2 2012 Rev 04 11 12 Figure 11 6 High Pressure Piping ...
Page 135: ...Section 11 Parts List 20479307 2 2012 Rev 04 11 14 Figure 11 7 Hydraulic Power Package ...
Page 137: ...Section 11 Parts List 20479307 2 2012 Rev 04 11 16 Figure 11 8 Motor Pump Assembly ...
Page 139: ...Section 11 Parts List 20479307 2 2012 Rev 04 11 18 Figure 11 9 Hydraulic Manifold Assembly ...
Page 141: ...Section 11 Parts List 20479307 2 2012 Rev 04 11 20 Figure 11 10 Hydraulic Hose Connections ...
Page 143: ...Section 11 Parts List 20479307 2 2012 Rev 04 11 22 Figure 11 11 Reservoir Assembly ...
Page 145: ...Section 11 Parts List 20479307 2 2012 Rev 04 11 24 Figure 11 12 Bulkhead Pipe Assembly ...
Page 147: ...Section 11 Parts List 20479307 2 2012 Rev 04 11 26 Figure 11 13 Electrical Assembly ...
Page 149: ...Section 11 Parts List 20479307 2 2012 Rev 04 11 28 Figure 11 14 Junction Box ...
Page 157: ...Section 11 Parts List 20479307 2 2012 Rev 04 11 36 Figure 11 18 Heat Exchanger Kit Oil to Air ...
Page 158: ......
Page 159: ......