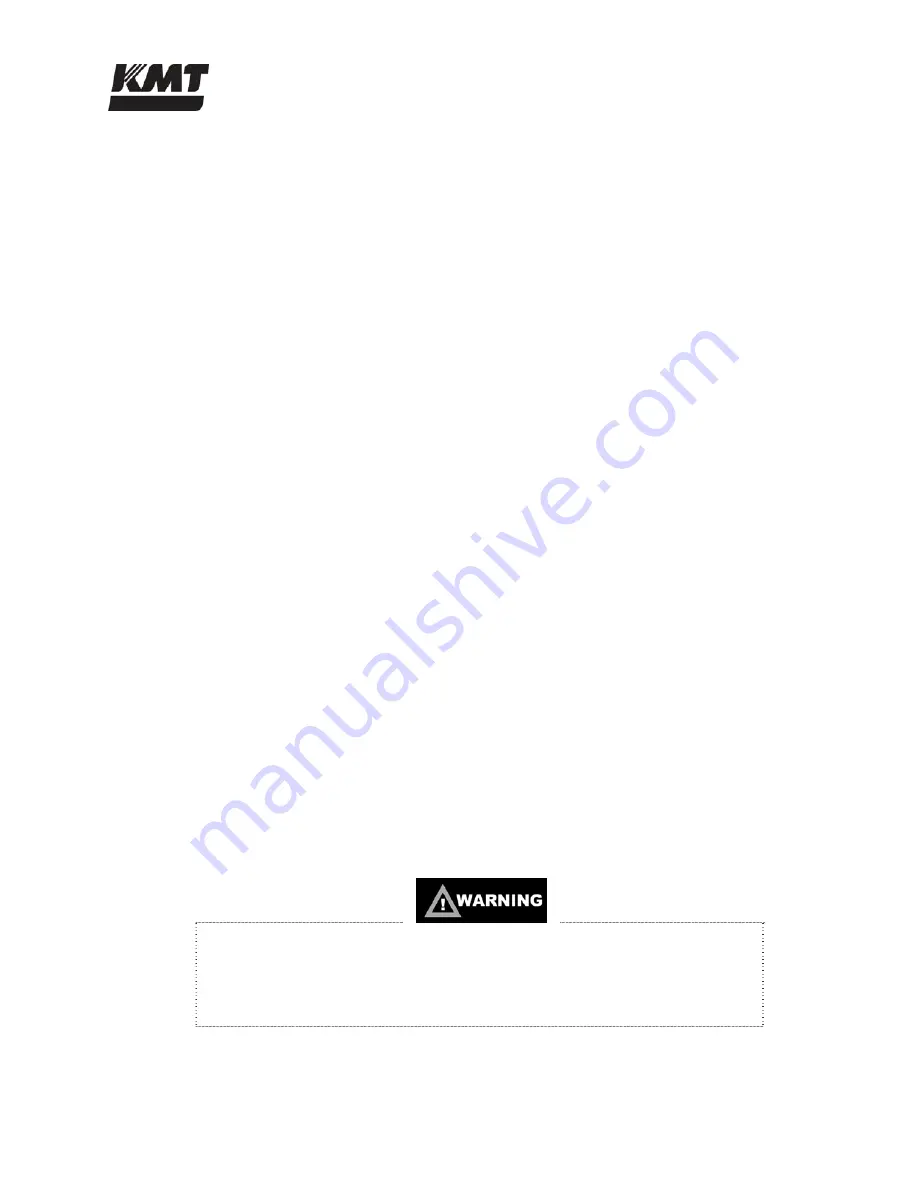
Section 8
High Pressure Water System
20479291
2-2012/Rev 04
8-11
4.
Connect the high and low pressure water piping, following the procedure, High and Low
Pressure Water Piping.
5.
Start the machine in low pressure mode to flush air from the high pressure components
and to check for obvious leaks. After 5-10 strokes, switch to high pressure operation and
check for leaks.
If leaks are detected, turn the machine off and remedy the problem. When the problem
has been remedied, repeat the start up procedure, moving from low to high pressure soon
after the intensifier starts pumping water. There is no further need to flush air from the
system.
High Pressure Cylinder Maintenance
The plunger seal area in the high pressure cylinder bore should be inspected and cleaned each
time the high pressure seal assembly is replaced.
1.
Clean the sealing area on the inside diameter of the high pressure cylinder and inspect the
bore for rings, scratches, pits, residue or other potential leak paths.
Seal material or residue can build up, forming a ring. Running a fingernail across the
buildup will cause it to appear as a surface flaw. Grooves or ridges are typically seal
debris buildup rather than marks on the inside diameter wall of the cylinder.
2.
Polish the inside diameter of the cylinder where the seal will locate with 600-grit wet/dry
sandpaper. Hold the sandpaper on the end of your finger and move in a cylindrical wiping
motion. Polish in a circumferential motion only. Do not polish or drag the sandpaper
along the length of the cylinder.
3.
Clean the residue from the inside diameter of the cylinder and re-inspect for surface
defects.
8.7
Hard Seal End Caps
KMT Waterjet recommends loosening the jackbolts and removing the hard seal end caps (HSEC)
only to service the inlet check valve and the cone seat on the sealing head.
Hard Seal End Cap Removal
Prior to removing electrical power or any high or low pressure piping, start the machine and
extend the on the end to be serviced to allow full exposure when the unit is disassembled.
1.
Turn the machine off and observe the appropriate Lockout/Tagout procedures.
Severe injury can result if the machine is not properly locked out. Observe
electrical Lockout/Tagout procedures before proceeding.
Ensure all pressure is relieved or blocked from the hydraulic and high pressure
circuits before proceeding.
Summary of Contents for STREAMLINE S50
Page 1: ...MANUAL 20479050 R04 STREAMLINE S50 WATERJET INTENSIFIER OPERATION AND MAINTENANCE MANUAL ...
Page 20: ......
Page 22: ......
Page 125: ...Section 11 Parts List 20479307 2 2012 Rev 04 11 4 Figure 11 1 Streamline S50 Intensifier Unit ...
Page 127: ...Section 11 Parts List 20479307 2 2012 Rev 04 11 6 Figure 11 2 Intensifier Assembly ...
Page 131: ...Section 11 Parts List 20479307 2 2012 Rev 04 11 10 Figure 11 5 Hydraulic Piston Assembly ...
Page 133: ...Section 11 Parts List 20479307 2 2012 Rev 04 11 12 Figure 11 6 High Pressure Piping ...
Page 135: ...Section 11 Parts List 20479307 2 2012 Rev 04 11 14 Figure 11 7 Hydraulic Power Package ...
Page 137: ...Section 11 Parts List 20479307 2 2012 Rev 04 11 16 Figure 11 8 Motor Pump Assembly ...
Page 139: ...Section 11 Parts List 20479307 2 2012 Rev 04 11 18 Figure 11 9 Hydraulic Manifold Assembly ...
Page 141: ...Section 11 Parts List 20479307 2 2012 Rev 04 11 20 Figure 11 10 Hydraulic Hose Connections ...
Page 143: ...Section 11 Parts List 20479307 2 2012 Rev 04 11 22 Figure 11 11 Reservoir Assembly ...
Page 145: ...Section 11 Parts List 20479307 2 2012 Rev 04 11 24 Figure 11 12 Bulkhead Pipe Assembly ...
Page 147: ...Section 11 Parts List 20479307 2 2012 Rev 04 11 26 Figure 11 13 Electrical Assembly ...
Page 149: ...Section 11 Parts List 20479307 2 2012 Rev 04 11 28 Figure 11 14 Junction Box ...
Page 157: ...Section 11 Parts List 20479307 2 2012 Rev 04 11 36 Figure 11 18 Heat Exchanger Kit Oil to Air ...
Page 158: ......
Page 159: ......