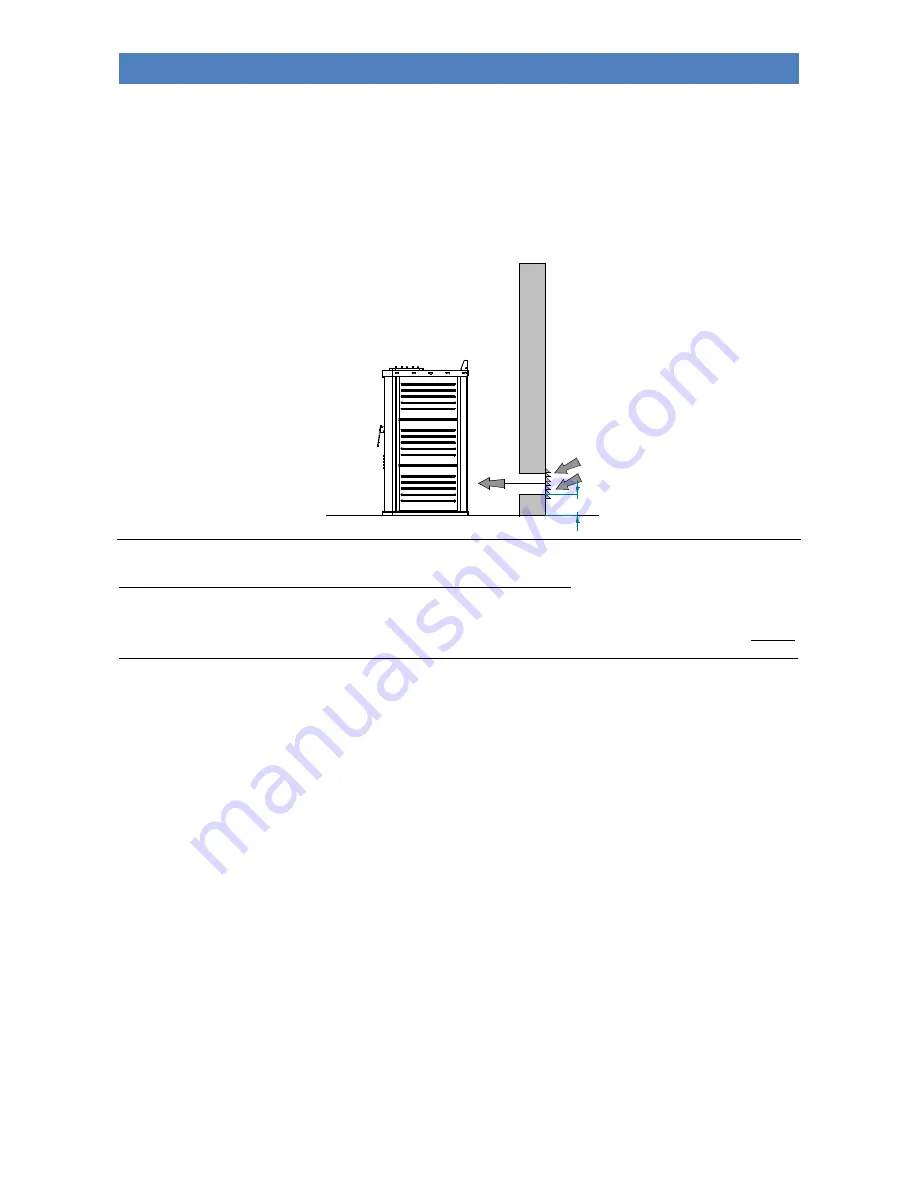
STAR 14 PELLET BOILER STOVE
11
EN - Rev. 2.1
Do not connect the external air vent directly to the appliance through piping. If there are other heating or extraction
devices inside the room, the air vents must guarantee a sufficient amount of air for properly operating all the devices.
Only sealed appliances (e.g. C type gas appliances, according to the UNI 7129 Standard) or appliances that do not
cause a lower pressure compared with the external environment can pre-exist or be installed in the place where the
appliance is installed.
Extractor fans can cause malfunctions to the appliance if used in the same room.
Fig. A
20
The flue pipe and connection to the same
The flue pipe is an essential element for the efficient operation of the appliance. The flue must have a minimum cross-
sectional area as that indicated in the technical specifications of the appliance (100 mm). Each product must be
equipped with its own flue, without other adjoining elements (boilers, chimneys, stoves etc.). The flue dimensions are
closely related to its height, which must be measured from the appliance flue gas outlet to the base of the stack. In order
to guarantee adequate draught, the chimney stack flue outlet surface must be twice as big as the flue pipe cross-section.
The discharge pipe for combustion products generated by the forced draught device, must comply with the following
requirements:
-
It must seal off the combustion gases, as well as being waterproof and suitably isolated and insulated in relation to
the conditions of use (refer to UNI 9615);
-
It must be made of suitable materials capable of withstanding normal mechanical stress, heat, and the effects of
combustion gases and condensate, if any;
-
It must go upwards after the vertical section, for the entire remaining part, with a minimum gradient of 5%; The sub-
horizontal section must not have a length greater than ¼ of the effective height H of the flue or chimney, and must
not be longer than 2,000 mm;
-
It must preferably have a round internal cross-section: square or rectangular cross-sections must have rounded
corners with radius not inferior to 20 mm;
-
It must have a constant, free and independent internal cross section;
-
Rectangular cross-sections must have a maximum ratio of 1.5 between the sides;
-
If the flue pipe is installed on the outside it is essential that it is insulated in order to avoid the flue gas cooling
allowing condensation to form;
-
Parts made from non-combustible materials (it is absolutely prohibited the use of aluminium flue pipe) - capable
of withstanding combustion gases and potential condensation - must be used for mounting the flue gas pipes (for the
section from the appliance to the flue inlet);
-
It is forbidden to use fibre cement pipes to connect the appliance to the flue;
-
Flue pipes must not pass through rooms in which the installation of combustion devices is prohibited;
-
The flue pipes must be assembled in such a way as to guarantee adequate sealing of flue gases during low pressure
operation of the appliance;
-
The installation of horizontal sections is prohibited;
-
It is prohibited to use counter sloping elements;
-
The flue gas pipe must allow for the recovery of soot or be cleanable, and must have a constant cross-section;