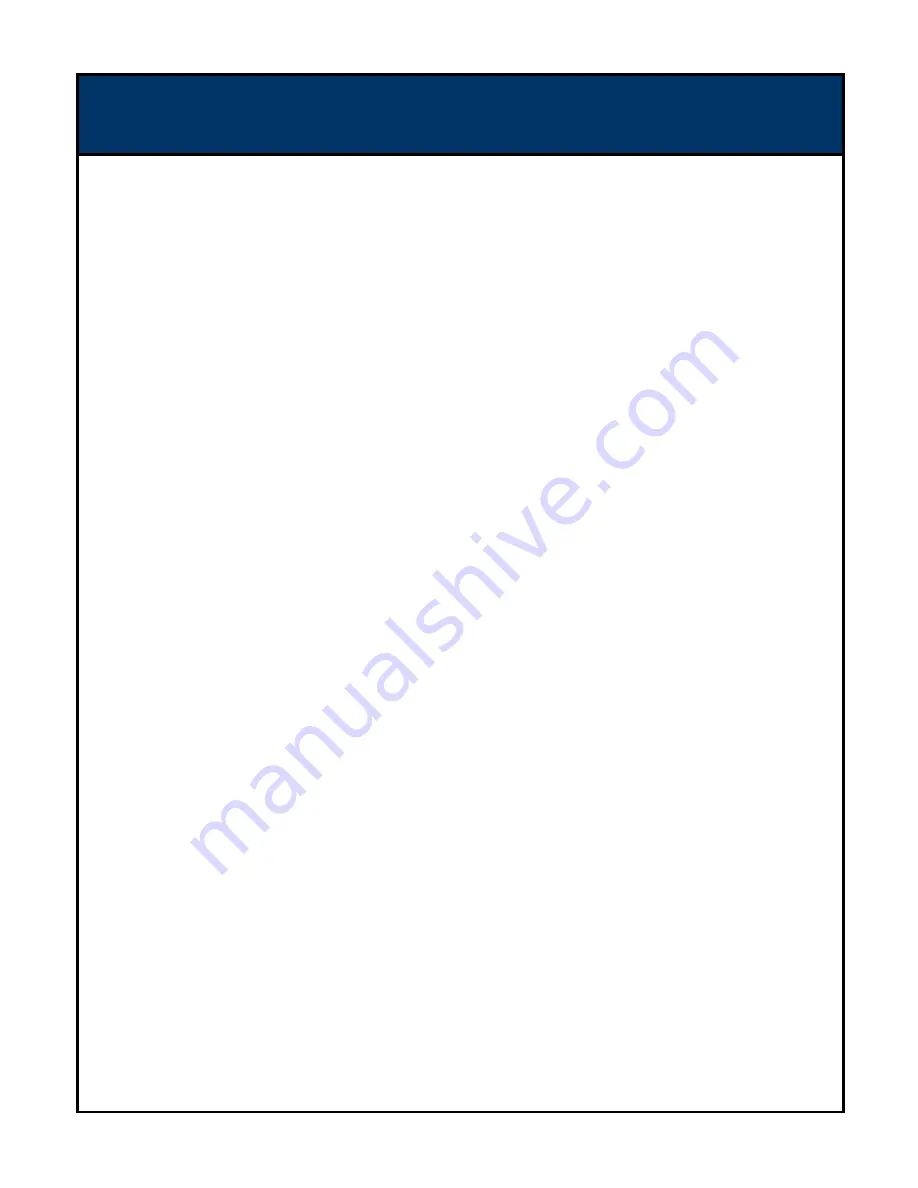
CONTENTS
1) overall view
1 -1. General information
**************************************
3
2) Product description
2 - 1. Boiler Specification
**************************************
4
2 - 2. Product dimensions
**************************************
5
2 - 3. Burner Specification
**************************************
6
3) Installation
3 - 1. Standard chimney installation
**************************************
9
3 - 2. Standard heating & hot water installation
**************************************
11
3 - 3. Standard gas connection installation
**************************************
14
3 - 4. Burner connection spec
**************************************
15
3 - 5. connecting Electricity
**************************************
16
4) Main part spec
4 - 1. Gear pump
**************************************
17
4 - 2. Electronic pump
**************************************
17
4 - 3. Ignition transformer
**************************************
19
4 - 4. Connector
**************************************
19
4 - 5. Ignition bar
**************************************
20
4 - 4. Adjustment and gas conversion
**************************************
21
5) Burner direction for assembly
5 - 1. Burner part exploded view
**************************************
22
6) Teat working
6 - 1. Check list before switching - on
**************************************
24
7) Direction For assembly
7 - 1. Boiler part exploded view
**************************************
25
7 - 2. Part name
**************************************
26
8) Maintenance guide
8 - 1. Assembly of Burner
**************************************
27
8 - 2. Assembly of Temp. and Overheating Sensors
**************************************
28
8 - 3. How to clean Heat exchanger's Exhaust tube
**************************************
29
9) Function of the controller
9 - 1. Main controller part mane
**************************************
30
9 - 2. Room control part mane (CTR-5700 plus)
**************************************
31
9 - 3. Room control LED panel
**************************************
32
10) Troubleshooting guide (error code)
10 - 1. Finding failure
**************************************
33
11) Technical Data Table
**************************************
34
10) Memo
**************************************
35
11) Warranty
**************************************
36
2페이지
Summary of Contents for TURBO-17
Page 25: ...7 Direction for assembly 7 1 Boiler Part exploded view 25페이지 ...
Page 35: ...12 Memo 35페이지 ...
Page 36: ...13 Warranty 36페이지 ...