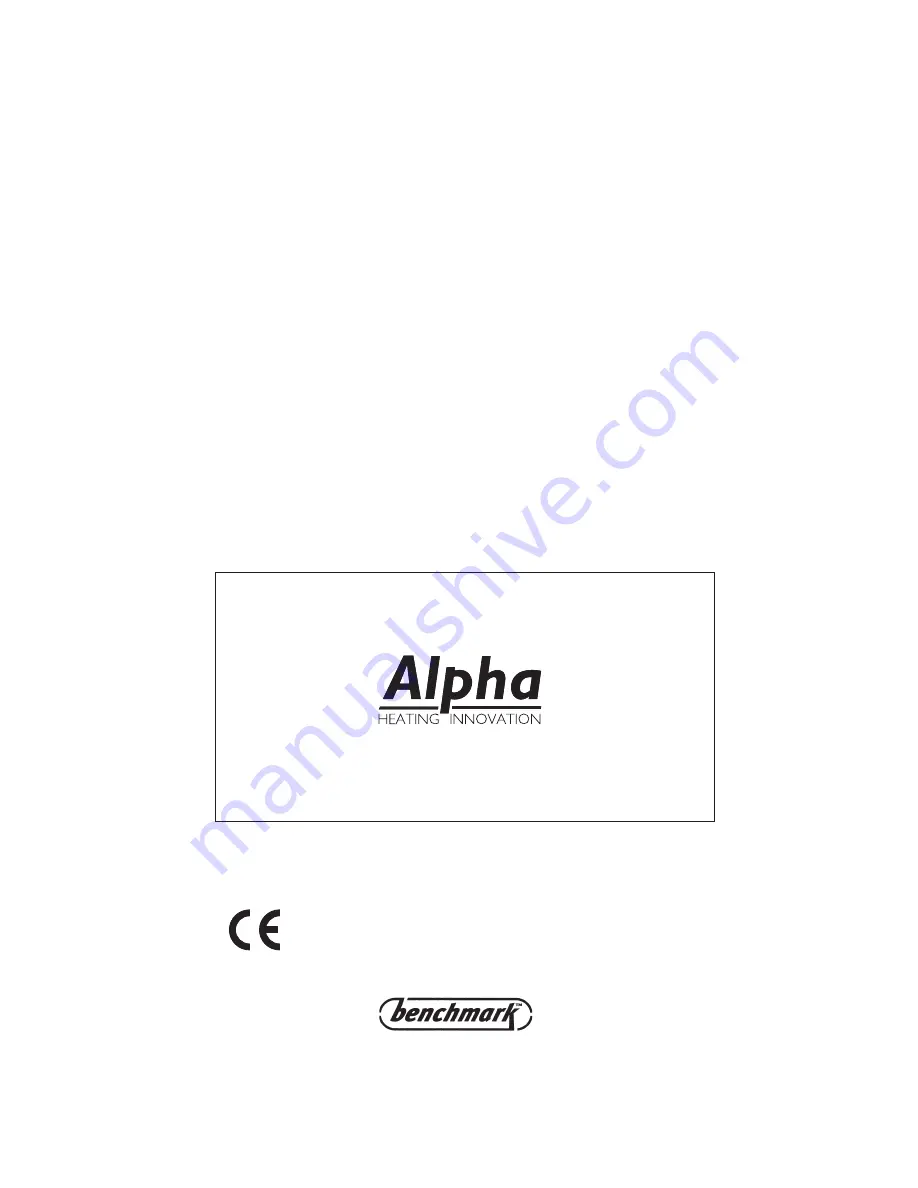
Installation and Servicing
Instructions
Alpha Pro Tec 50, 70, 90 and 115
Wall Mounted, Fan Assisted, Gas Fired, High Efficiency
Condensing System Boilers
For use with Natural Gas or Propane Gas (LPG)
Leave these instructions with the User
Nepicar House, London Road,
Wrotham Heath, Sevenoaks,
Kent TN15 7RS
For Technical help or for Service call ...
ALPHA HELPLINE
Tel: 0870 3001964
0051