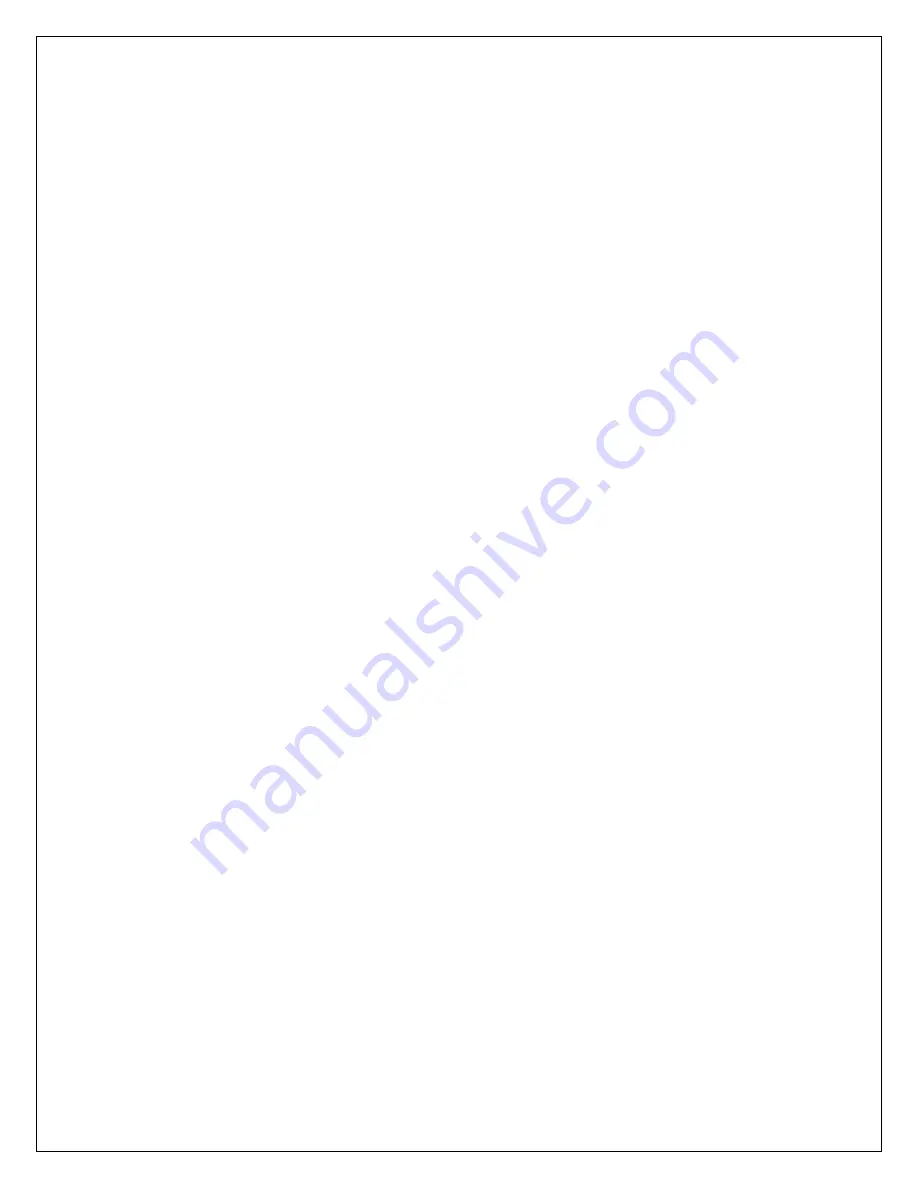
IOM/CPHM/DEC19/01
ISSUE DATE:14-12-2019
Page
40 | 48
REVISION NO.1
6. SAFETY INSTRUCTIONS WHILE MAINTENANCE & SERVICING.
Do not attempt repairs of the pump or its accessories which you do not know. Use
proper tools.
Before attempting any maintenance on a pump particularly if it has been handling any
form of hazardous liquid, it should be ensured that the unit is safe to work on. The
pump must be flushed thoroughly with suitable cleaner to purge away any of
the product left in the pump components.
This should be carried out by the plant operator and a certificate of
cleanliness obtained before starting work. To avoid any risk to health it is also
advisable to wear protective clothing as recommended by the site safety officer
especially when removing old packing, which may be contaminated.
Isolate the equipment before any maintenance work is done. Switch off the
main supply, remove fuses, apply lockouts where applicable and affix suitable
isolation warning signs to prevent inadvertent reconnection. In order to avoid the
possibility of maintenance personnel inhaling dangerous fumes or vapours, s h i f t t o
a location / suitable maintenance area by removal of bearing housing and shaft
assembly.
Check and ensure that the pump operates at below the maximum working pressure
specified in the manual or on the pump nameplate and before maintenance,
ensure that the pump is drained down.
Wear a suitable mask or respirator when working with packing and gasket containing
fibrous material, as these can be hazardous when the fibrous dust is inhaled.
Be cautious, if other supplier’s components have been substituted for genuine KBL
parts, these may then contain hazardous materials.
Store all oily rags or other flammable material in a protective container in a safe
place. Do not weld or flame cut on pipes/tubes that contain flammable fluids. Clean
them thoroughly with nonflammable solvent before welding or flame cutting on them.
Use solvent/chemical resistant gloves for hand protection.