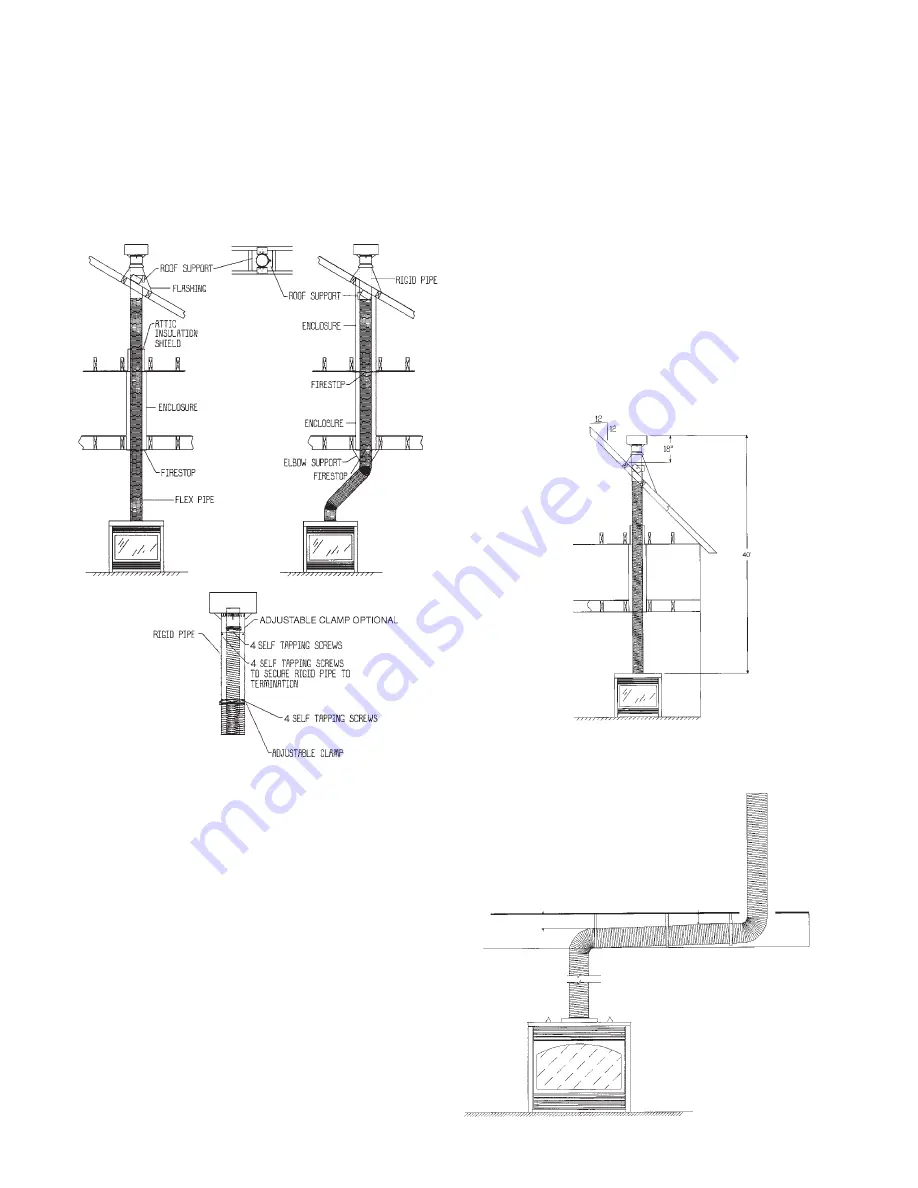
23
Using Flex Bends
4. Avoid cutting joists by offsetting the flex pipe. See Fig. 2.
5. When using 45˚ bends a bend support is required directly above the highest
bend.
6. When installing a bend in a joist area a minimum of 2
1
/
2
” clearance to com-
bustible to the top of bend must be maintained, sides and bottom of pipe, a
1” clearance to combustibles must be maintained. If running horizontal
through an area a 1
1
/
2
” minimum clearance to the top of the horizontal pipe
must be maintained.
7. Maximum vertical height of system should not exceed 40 feet.
8. Use roof support and 7” rigid pipe at roof level. Flex not permitted within
roof support.
9. When penetrating the roof a rigid 7” galvanized pipe must be used. Attach
the 7” flex to the 7” rigid with high temperature sealant, secure with four
screws assuring the flex and rigid pipe are secured. 4” flex pipe must be
secured the same way with 4 screws but must penetrate the 4” flex and 4”
section of termination. Attach 7” rigid pipe to 7” termination with sealant
and screw with 4 sheet metal screws. (See Fig. 3).
10. Vertical termination clearance is 18” (inches) above the roof, measured
from highest point of exit on the roof line.
11. Support vertical pipes to maintain minimum of one inch or greater clear-
ances to combustibles.
FIG. 1
FIG. 2
Venting Straight Up Through Roof
1. An Attic Insulation Shield must be installed where the vent passes from a
lower living space into an attic space where the chimney is not enclosed. It
is designed to keep insulation materials away from the chimney. See Fig. 1.
2. When installing the Attic Insulation Shield where the chimney passes from
a living space to an attic space, install the shield from below and nail in
place using 1” spiral nails.
3. A fire stop must be installed on the bottom side of the joists when passing
through a ceiling or floor. If an attic insulation shield is to be used, a fire
stop is not required.
FIG. 3
Roof Flashing
Ensure that you have the proper roof flashing by checking your roof
pitch using a level and two rulers, or by using a roof pitch card.
See figure below.
Slide a Roof Flashing suitable to your roof slope over the vent. Place
the edge of the flashing plate that will be on the higher part of the roof
slope under the shingles. Both the sides and the lower edge lay on top
of the shingles.
NOTE: At the top edge of the flashing plate, lift the shingles and
nail the plate to the roof deck, then cement the shingles to the plate
with a suitable waterproof mastic.
Ensure that the chimney is plumb. Square up the flashing plate and nail
in place to the roof deck. Use 12 nails with neoprene washers or cover
the heads with a suitable waterproof mastic.
Wrap the storm collar around the vent above the flashing. Secure the
ends together loosely with nut and bolt supplied. Slide the collar down
the vent until it comes in contact with the flashing. Tighten the bolt and
seal the Storm Collar to the vent with a suitable waterproof non-com-
bustible mastic.
The flashing and storm collar should be painted to match the roof
shingles. This will extend its life and improve the appearance. Clean,
prime and paint with suitable painting products.
1.5” Top of Horizontal Vent
2.5” Minimum Top of 90° Elbow
All other existing pipes 1” clearances to combustibles.
Support Straps required to maintain rise in venting.
OPTIONAL