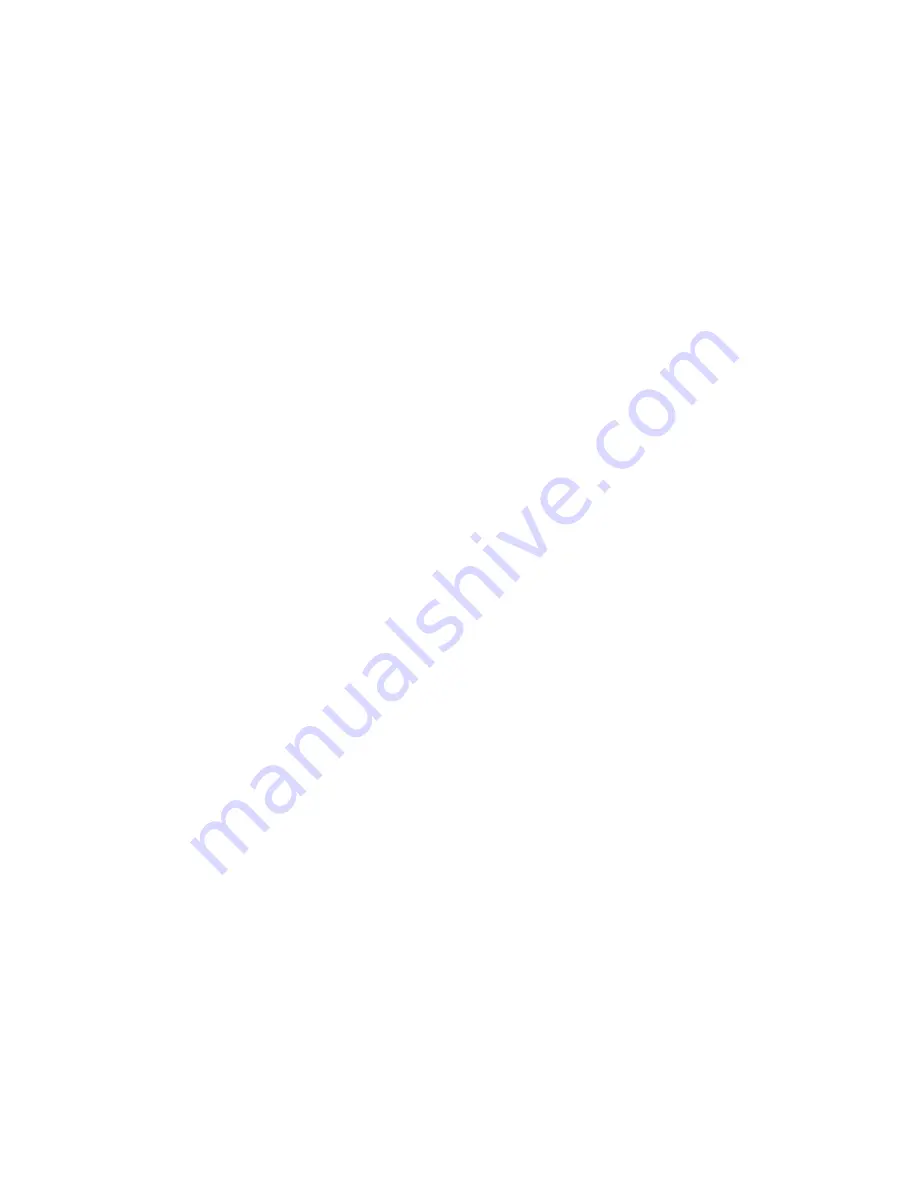
It is the purchaser and/or operator’s responsibility to….
Read and understand the information contained in this
manual.
Operate, lubricate, assemble and maintain the
equipment in accordance with all instructions and
safety procedures in this manual.
Inspect the equipment and replace or repair any
parts that are damaged or worn which under contin-
ued operation would cause damage, wear to other
parts, or cause a safety hazard.
Return the equipment or parts to the authorized
King Kutter dealer, from where it was purchased, for
service or replacement of defective parts that are
covered by warranty. (The King Kutter Factory may
inspect equipment or parts before warranty claims
are honored.)
Payment of all costs incurred by the dealer for traveling
to or transporting the equipment for warranty inspection
and or claims.
4
Summary of Contents for 999998
Page 2: ......
Page 10: ...10 Figure E Figure F Figure G Figure H Figure I Figure J...
Page 25: ...25 1...
Page 26: ...26 2 3...
Page 27: ...27 4 5...
Page 28: ...28 6 7 MODEL NO DESCRIPTION SN XXXXXXXXXX 8...
Page 40: ...40 40 HP GEARBOX...
Page 42: ...42 60 HP GEARBOX...
Page 44: ...44 80 HP GEARBOX...
Page 47: ...47...
Page 48: ......