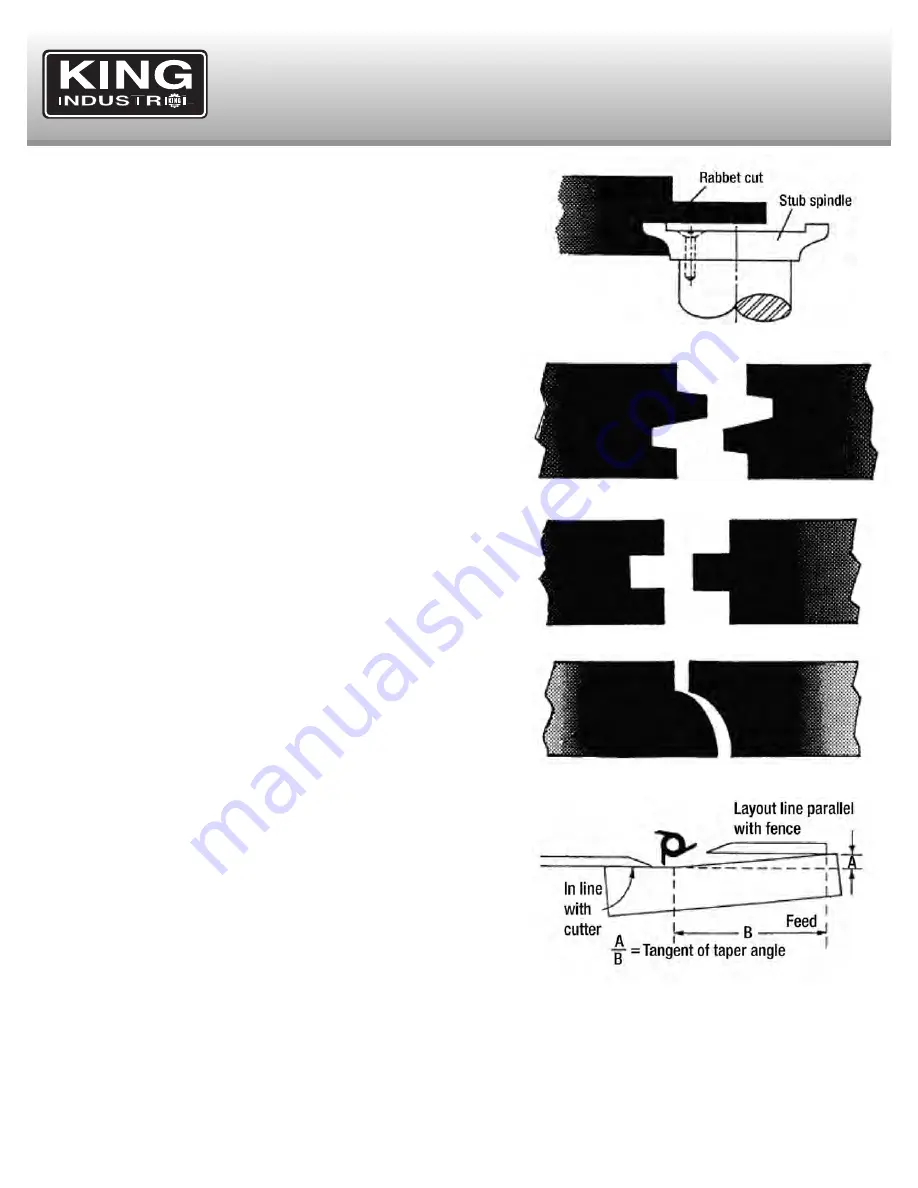
OPERATION
Operational guidelines
Sash and Door Shaping continued...
• Fig.53
shows both cuts required for a window sash rail end. The first operation
at top is a rabbet cut made with a groove cutter. The second operation is
performed with a stub spindle and buttonhead screw.
butt Joints
All butt-type joints require both workpieces to be perfectly square and
straight-edged.
Glue butt Joint
To perform a glue butt joint, both fences are kept inline and adjusted for a depth
of cut (Fig.54). The cuts on both workpieces are part-edge cuts which do not
reduce the stock width during the cutting procedure. When shaping the two
workpieces, one is fed top-side up; the other is fed bottom-side up.
Tongued Joint
Similar to the glue joint, both fences are kept in-line for the tongued joint and
adjusted for a 1/4” depth of-cut with no reduction in stock width. With this joint,
however, both workpieces are fed with the same side up as shown in Fig.55.
Drop Leaf Joint
When shaping a drop-leaf joint as shown in Fig.56, the leaf workpiece is shaped
with a Drop-Leaf Bead cutter; the table workpiece is shaped with a Drop-Leaf
Cove cutter.
With this type joint, the whole edge of both workpieces is shaped, same-side up,
and allowance made for a 1/16” reduction in width. Adjust the infeed fence to
reduce the workpiece width by 1/16”, and adjust the outfeed fence to
compensate for stock removed.
Taper Cuts
Taper cuts can be made by offsetting the fences for the amount of taper desired,
or with a layout line on the stock which can be paralleled to the infeed fence as
shown in Fig.57.
Start the cut by holding the stock against the infeed fence and swinging it into
contact with the outfeed fence just past the cutterhead. As the cut is started,
transfer pressure to hold the workpiece against the outfeed fence, and continue
feeding the workpiece through. After the first cut, the fences will have to be
readjusted in order for the second cut (parallel cut) and the final depth-of-cut to
remain true with the taper.
Caution:
Do not use the standard fence for short work (12” or less in length on
the side to be cut). Instead, use a miter gauge or special fixture to avoid losing
control of the workpiece.
FIGURE 53
FIGURE 54
FIGURE 55
FIGURE 56
FIGURE 57