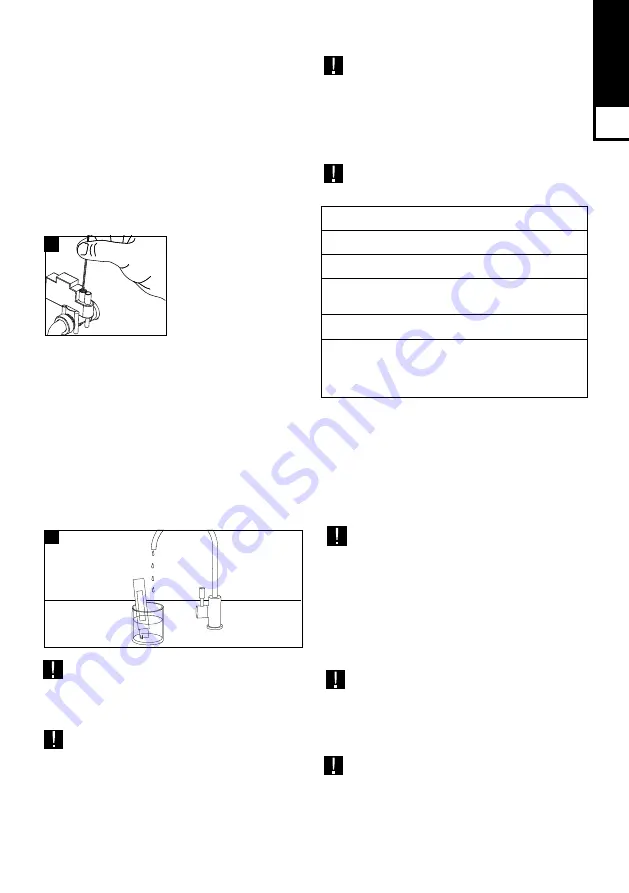
25
TM
6.4. SYSTEM STOP, START AND WATERTIGHT CHECK
Turn off the equipment’s tap on the work surface with the
hydraulic and electric power on (according to model), and
carry out a visual inspection of the equipment ensuring no
leakages occur (during approx. 1 minute).
To ensure the correct working of all the equipment’s com-
ponents, close the tank valve, thus completing a rapid sys-
tem pressurisation. In the event of the pump failing to stop
(PUMP model), adjust the maximum pressure gauge setting
with a 2mm Allen key until the pump stops (9).
In the case of the SO model, after turning the tap off and
closing the tank valve, check that, after a few minutes, the
water flow to the drain stops completely.
Keep the equipment pressurised for a few minutes, carrying
out a visual inspection to find possible leakages or drips.
Once complete, open the pressurised tank valve again.
6.5. RINSING AND CLEANING
Turn on the equipment’s tap and check the quality of the
water being dispensed with a conductivity tester or TDS;
check the reduction of salt obtained is sufficient in relation
to the water to be treated (10).
Warning: In the event of discovering that the water
dispensed does not adhere to current national legisla-
tion, close the inlet valve, empty the equipment with
the tap, disconnect it from the electric mains (PUMP model),
and contact your technical service facility.
Warning: Wait one hour for the tank to fill with the
equipment on standby. Empty the equipment via the
tap. Repeat this process twice before consuming treated
water.
9
TDS
10
7. MAINTENANCE
Warning: Some of your equipment’s components,
such as the membrane pre and post filters are con-
sumable items which have limited lifetime.
Their duration will depend on the quality of the local
water, consumption, type of use and specific water con-
ditions such as extreme turbidity, high chlorine levels,
excessive iron content etc.
Warning: With the aim of guaranteeing the quality of
the water supplied by your equipment, it should un-
dergo regular maintenance.
Recommended maintenance
•
Sediment pre-filter: At least once a year *
•
Carbon pre-filter: At least once a year *
•
Osmosis membrane: Every 3 years approx. (for soft wa-
ter - hardness >15ºHF)
•
Post-filter: At least once a year. *
•
Sanitization: During initial operation. At least once a
year in function of the use. Each time components in con-
tact with water are accessed or water has not been con-
sumed for more than a month.
*
In function of the characteristics of the water and its use.
All maintenance should be carried out by qualified techni-
cians who should handle the equipment properly, as well
as using original replacement parts in order to maintain
the equipment’s characteristics, warranty, equipment
features as well as preserving the quality of the water
dispensed.
Warning: The use of non-original replacement parts,
non-regulatory installation or initial operation,
maintenance or improper use may invalidate the
warranty, as well as rendering invalid the equipment’s
certifications.
An excess of any compound (total chlorine, turbidity,
hardness etc.) may reduce the equipment’s useful life and
certain components. This maintenance advice is only a
guide.
Warning: All replacement parts come in specially
designed individual packaging to ensure hygienic
storage and transit. Take special hygiene measures
when removing said parts from their packaging as well as
during handling of the various components and connec-
tors.
Warning: Before dismantling the equipment, make a
note of all material necessary for the required main-
tenance (read section 6 installation) as well as the
necessary space for work. Work should be carried out in a
correctly lit place, in appropriate hygienic conditions and
with sufficient space to work comfortably.
Summary of Contents for ERGO RO BLUE
Page 1: ...IU Instructions for use Reverse osmosis equipments...
Page 2: ......
Page 4: ......
Page 5: ...User s Manual UM Reverse osmosis equipments...
Page 9: ...9 UM 8 NOTES...
Page 10: ......
Page 11: ...Data Sheet Service Book DS Reverse osmosis equipments...
Page 12: ...DS 12...
Page 20: ......
Page 21: ...Technical manual TM Reverse osmosis equipments...
Page 27: ...27 TM 8 NOTES...
Page 28: ......
Page 29: ...Sanitising procedure SP Reverse osmosis equipments...
Page 34: ...8 NOTES SP 34...
Page 35: ...8 NOTES SP 35...
Page 36: ...ERGOROBLUEIU2018 IU...