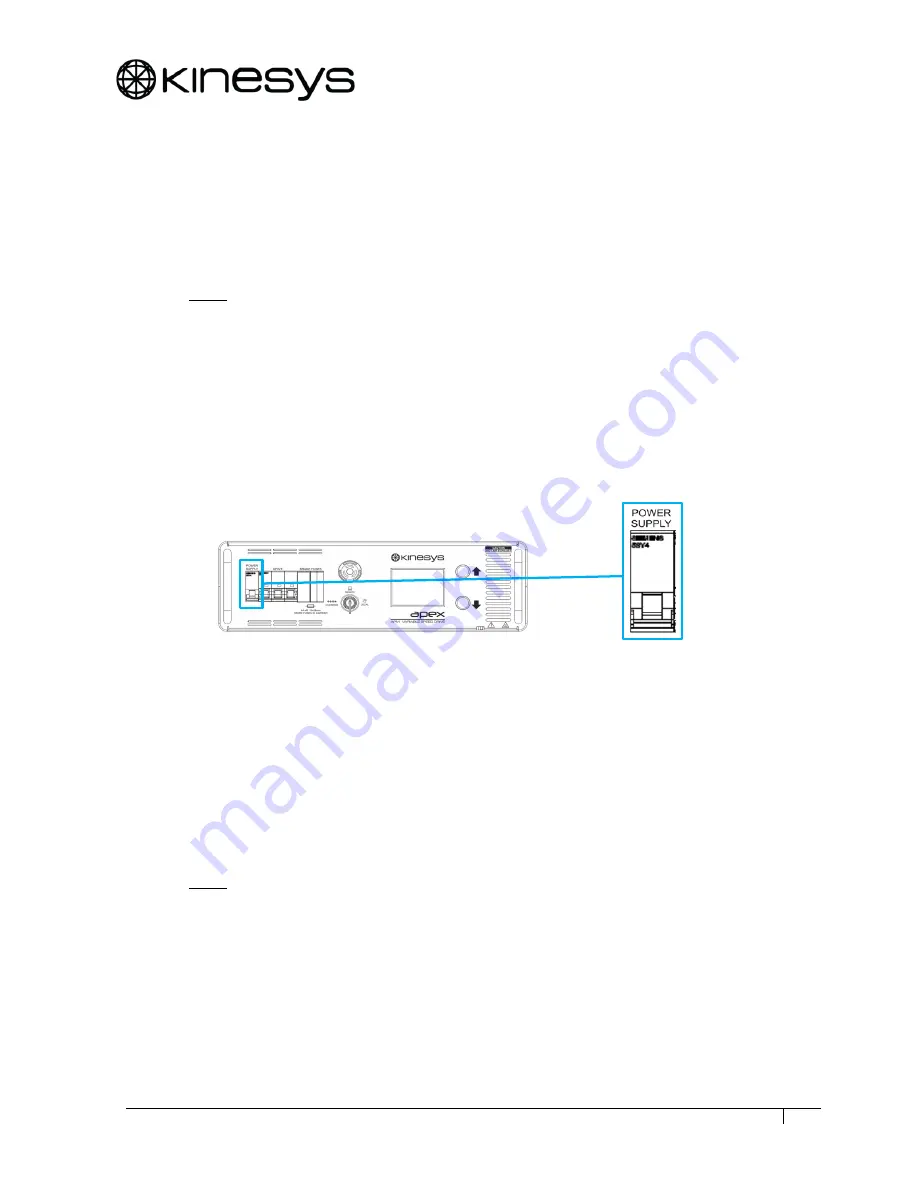
USER GUIDE
apexDRIVE User Guide 9200162 0v10
22
6 Circuit protection
Each apexDRIVE uses Miniature Circuit Breakers (MCB) to protect the power
supply to the apexDRIVE control and the connected apexHOIST.
Additionally fuses are provided to protect the electromagnetic brakes in the
apexHOIST.
WARNING!
DO NOT ATTEMPT TO KEEP AN MCB POWERED ON BY HOLDING THE
LEVER IN THE ON POSITION
WARNING!
ALWAYS REPLACE FUSES WITH SAME TYPE AND RATING. SPARE FUSES
ARE SUPPLIED IN THE ‘BRAKE’ FUSE CARRIER
6.1
Control ‘POWER SUPPLY’ MCB
Figure 19
Power MCB
The
POWER SUPPLY
MCB is used to turn the apexDRIVE on and off. With the
MCB lever up the apexDRIVE is on, moving the MCB lever down will turn the
apexDRIVE off.
If the power MCB should trip in to the down position try to move the lever up to
restore power. If the MCB immediately trips again this indicates a fault. Switch
over to an alternative apexDRIVE and contact your supplier or Kinesys for support.
WARNING!
DO NOT ATTEMPT TO KEEP AN MCB POWERED ON BY HOLDING THE
LEVER IN THE ON POSITION