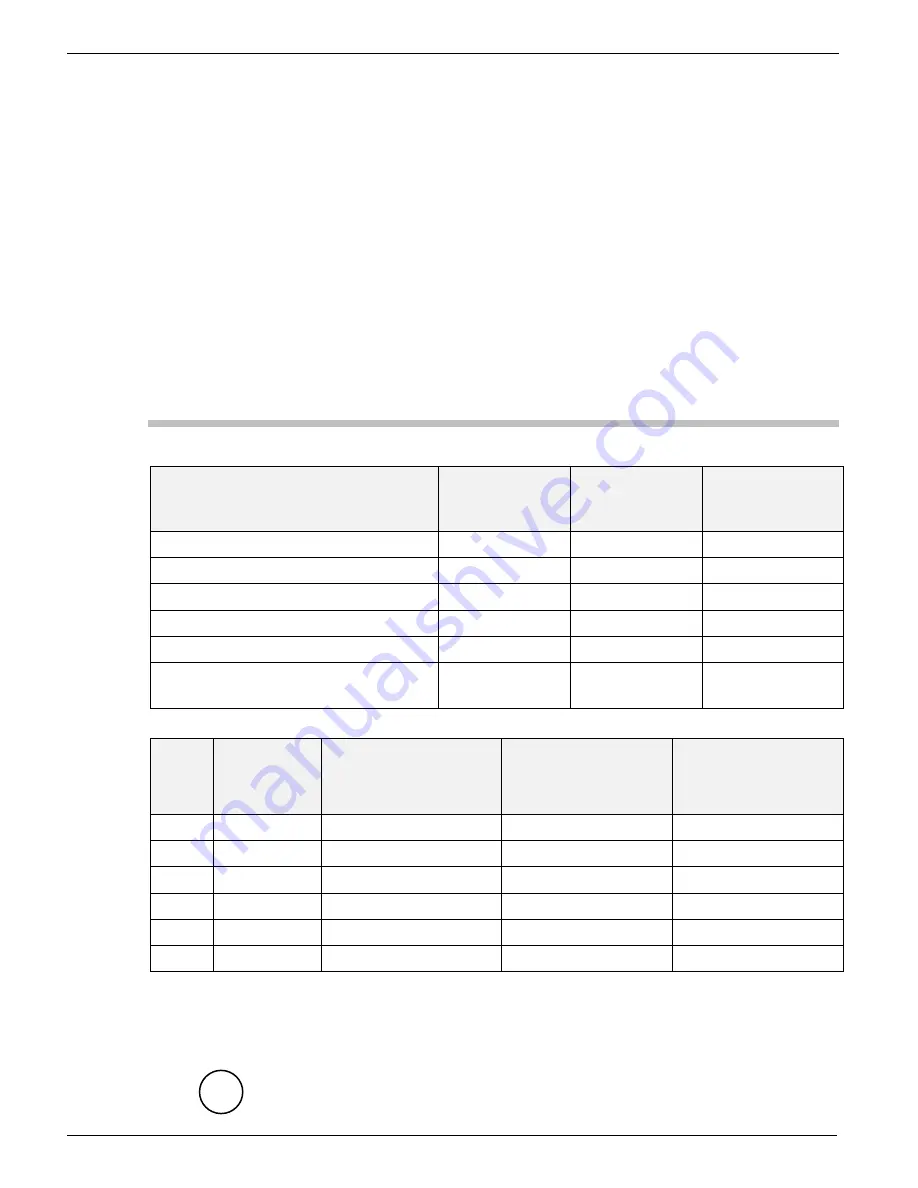
D
OCUMENT
301900,
R
EVISION
D
46
E
PI
S
ENSOR
U
SER
G
UIDE
User-Supplied Cable
If you are using your own cable, be sure that is has sufficient conductors of
the required wire gauge for your installation and that it provides adequate
shielding to maintain the noise performance of the EpiSensor. The
conductors used for the signals and the control signals (Cal and CCE) carry
little current. The table in the section above shows the resistance and
calculated voltage drop for different lengths of cables when using an Altus
recorder. You can substitute your own values to calculate the allowed cable
length.
In order to exceed these lengths, use a regulated power supply that supplies
12-15 V. Calculate the voltage drop in the cable at the maximum supply
current and make sure that it meets the minimum operating voltage for the
chosen configuration.
Table 9: EpiSensor cabling requirements (1 foot = 0.3048 meters)
Sensor Type
EpiSensor low-
power, 2g,
2.5V S/E
EpiSensor low-
noise, 2g, 5V
differential
EpiSensor low-
noise, 2g, 20V
differential
Sensor minimum operating voltage
10.0
10
11.5V
Maximum supply current
30.0
52
70mA
Minimum supply voltage
11.6
11.6
11.6V
Allowed cable voltage drop
1.6
1.6
0.1V
One-way allowed cable drop
0.8
0.8
0.05V
One-way allowed resistance
at full-scale output
26.7
15.4
0.7 Ohms
Cable
AWG
Cable
Resistance
per 1000 Feet
Low-power 2g, 2.5V
Single-ended Maximum
Cable Run in Feet
Low-noise 2g,5V
Differential Maximum
Cable Run in Feet
Low-noise 2g, 20V
Differential Maximum
Cable Run in Feet
24
27.70
950
550
20
22
17.50
1500
880
40
20
10.90
2400
1400
60
18
6.92
3850
2200
100
16
4.35
6100
3500
160
14
2.73
9700
5500
260
Grounding
The cable assembly technique used for connecting the EpiSensor to an
Altus instrument is designed to allow future compliance with the
requirements of the emissions and immunity standards (EN 55022
CE