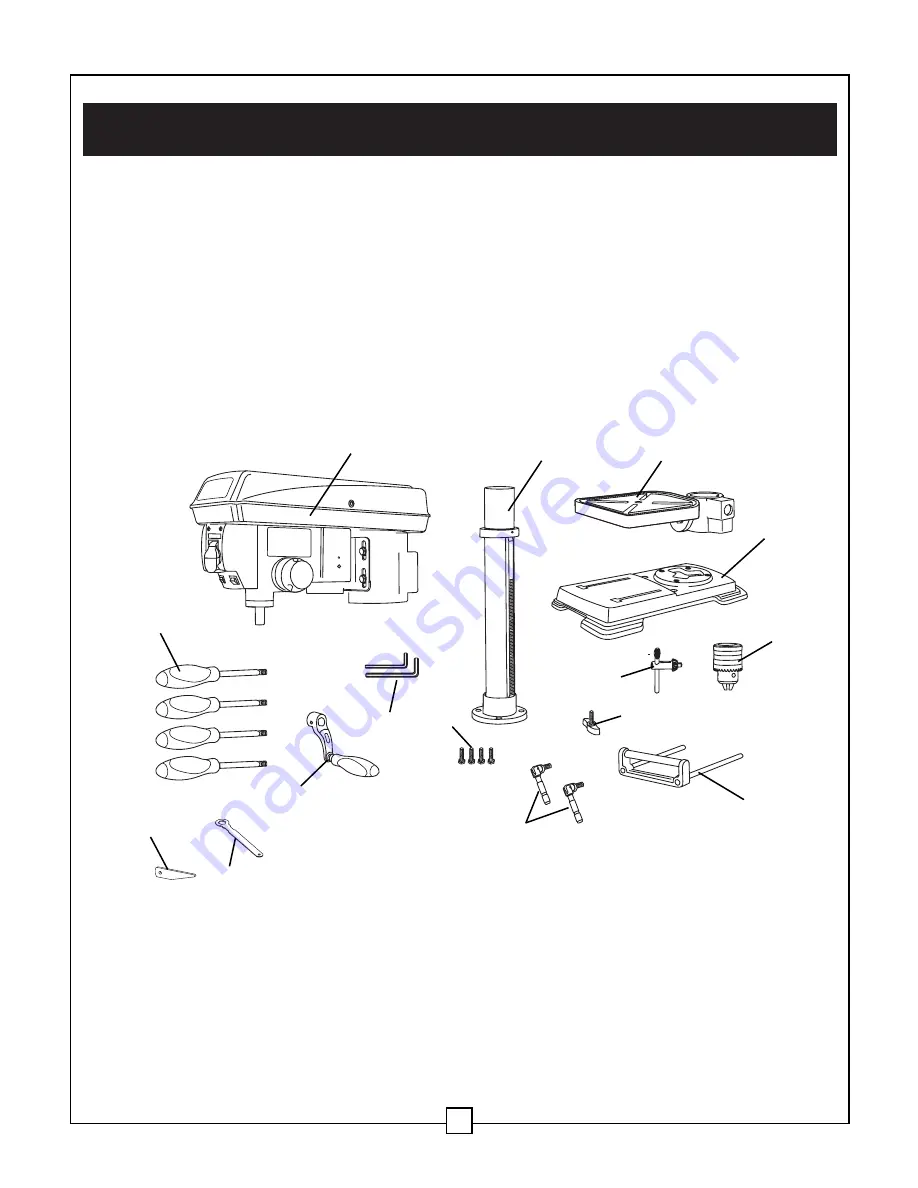
UNPACKING AND CLEANING
Unpack the bench drill press and all its parts, and compare against the list below. Do not discard
the carton or any packaging until the bench drill press is completely assembled.
To protect the bench drill press from moisture, a protective coating has been applied to the
machined surfaces. Remove this coating with a soft cloth moistened with kerosene. Do not use
acetone, gasoline, or lacquer thinner to clean. Apply a coat of paste wax to the table and column.
Wipe all parts with a clean, dry cloth.
VI. Assembly and adjustments
9
Fig. 2
A
Head/motor assembly
B
Column assembly and table bracket
C
Table
D
Base
E
Chuck
F
Extension wing with integrated rollers
G
Chuck key
H
Wing knobs (2)
I
Table lock handles (2)
J Hex head bolts (4)
K Table crank handle
L Hex keys (2)
M Feed and speed handles (4)
P Table adjustment wrench
Q Wedge
A
J
I
H
B
C
K
Q
P
L
G
E
F
D
M