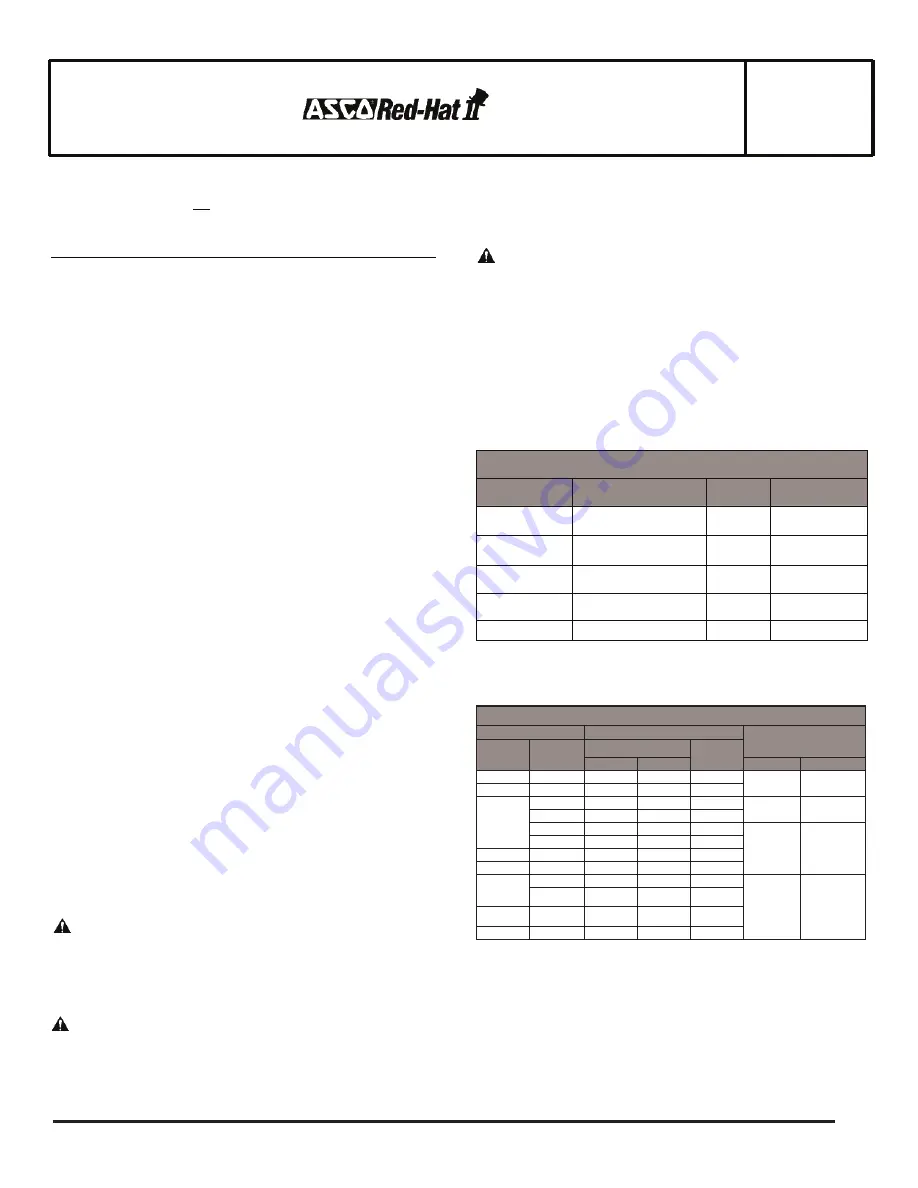
012420 / FLT-M02-0004
37
Kice Industries, Inc.
13. Appendix C
ASCO Valves
®
E255075 - 09/2015 All Rights Reserved.
I&M V_6583_R12
©
ASCO Valve, Inc.
50 Hanover Road, Florham Park, New Jersey 07932 www.ascovalve.com
Page 1 of 4
I&M V_6583_R12
Installation&Maintenance Instructions
OPEN-FRAME, GENERAL PURPOSE, WATERTIGHT/EXPLOSIONPROOF SOLENOIDS
OPTIONAL FEATURE FOR OPEN FRAME (GENERAL PURPOSE) CONSTRUCTION ONLY
SERIES
8016G/H
— SERVICE NOTICE —
ASCO
™
solenoid valves with design change letter “G” or “H” in the
catalog number (ex. 8210G1) have an epoxy encapsulated ASCO Red
Hat II
®
solenoid. This solenoid replaces some of the solenoids with
metal enclosures and open
-
frame constructions. Follow these installation
and maintenance instructions if your valve or operator uses this solenoid.
DESCRIPTION
Catalog numbers 8016G/H1 and 8016G/H2 are epoxy encapsulated
pull-type solenoids. The green solenoid with lead wires and 1/2 conduit
connection is designed to meet Enclosure Type 1-General Purpose, Type
2-Dripproof, Types 3 and 3S-Raintight, and Types 4 and 4X-Watertight.
The black solenoid on catalog numbers pre
xed “EF” is designed to meet
Enclosure Types 3 and 3S-Raintight, Types 4 and 4X-Watertight, Types 6
and 6P-Submersible, Type 7, Explosionproof Class I, Division1 Groups
A, B, C, & D and Type 9, -Dust-Ignitionproof Class II, Division1 Groups
E, F & G. The Class II, Groups F & G Dust Locations designation is
not applicable for solenoids or solenoid valves used for steam service or
when a class “H” solenoid is used. See
Temperature Limitations
section
for solenoid identi
cation and nameplate/retainer for service. When
installed just as a solenoid and not attached to an ASCO valve, the core
has a 0.250-28 UNF-2B tapped hole, 0.38 minimum full thread.
Series 8016G/H are also available in:
•
Open-Frame Construction:
The green solenoid may be supplied
with 1/4
spade, screw or DIN terminals. (Refer to Figure 4)
□
DIN Plug Connector Kit No. K236034:
Use this kit only
for solenoids with DIN terminals. The DIN plug connector kit
provides a two pole with grounding contact DIN Type 43650
construction (See Figure 6).
•
Panel Mounted Construction:
These solenoids are speci
cally
designed to be panel mounted by the customer through a panel
having a .062 to .093 maximum wall thickness. (Refer to Figure 3
and section on
Installation of Panel Mounted Solenoid
).
•
Junction Box:
This junction box construction meets Enclosure
Types 2, 3, 3S, 4, and 4X. Only solenoids with 1/4
spade or screw
terminals may have a junction box. The junction box provides a
1/2
conduit connection, grounding and spade or screw terminal
connections within the junction box (See Figure 5).
OPERATION
When the solenoid is energized, the core is drawn into the solenoid base
sub-assembly.
IMPORTANT: When the solenoid is de-energized, the initial return
force for the core, whether developed by spring, pressure, or weight,
must exert a minimum force to overcome residual magnetism created
by the solenoid. Minimum return force for AC construction is 0.69lbs
(3.1N) and 0.31 lbs (1.38N) for DC.
INSTALLATION
Check nameplate for correct catalog number, service, and wattage. Check
front of solenoid for voltage and frequency.
WARNING:
Electrical hazard from the
accessibility of live parts. To prevent the possibility
of death, serious injury or property damage, install
the open - frame solenoid in an enclosure.
FOR BLACK ENCLOSURE TYPES 7 AND 9 ONLY
CAUTION: To prevent
fi
re or explosion, do not install
solenoid and/or valve where ignition temperature of
hazardous atmosphere is less than 165°C. On valves used for
steam service or when a class “H” solenoid is used, do not
install in hazardous atmosphere where ignition temperature
is less than 180°C. See nameplate/retainer for service.
NOTE:
These solenoids have an internal non-resetable thermal fuse to
limit solenoid temperature in the event that extraordinary conditions occur
which could cause excessive temperatures. These conditions include high
input voltage, a jammed core, excessive ambient temperature or a shorted
solenoid, etc. This unique feature is a standard feature only in solenoids
with black explosionproof/dust-ignitionproof enclosures (Types 7 & 9).
CAUTION: To protect the solenoid valve or operator, install
a strainer or
fi
lter, suitable for the service involved in the inlet
side as close to the valve or operator as possible. Clean
periodically depending on service conditions. See ASCO
Series 8600 and 8601 for strainers.
Temperature Limitations
For maximum valve ambient temperatures, refer to chart. The temperature
limitations listed, only indicate maximum application temperatures for
eld wiring rated at 90
°
C. Check catalog number pre
x and watt rating
on nameplate to determine maximum ambient temperature. See valve
installation and maintenance instructions for maximum
uid temperature.
NOTE:
For steam service, refer to
Wiring
section,
Junction Box
for
temperature rating of supply wires.
™
§ Minimum ambient temperature -40°F (-40°C).
* When used with watertight aluminum junction boxers (screw or spade) max.
ambient and
uid temperature will be reduced to 157°F (69.4°C)
** 10.6 Watt solenoids rated for 104°F are 8030, 8260, 8316, 8321, 8320, 8360
& 8344 valves while those rated for 140°F are 8040 valves
Temperature Limitations for Series 8003H, 8007H and 8202H solenoids
Watt Ratings
Maximum Ambient
Temperature
Pre
x
Coil
Class
AC
DC
60 Hz
50 Hz
°C
°F
EF
FT
6.1
8.1
-
52
125
EF
FB
9.1
11.1
-
FT
6.1
8.1
-
55
131
FB
9.1
11.1
-
HT
-
-
10.6
40
104
HB
-
-
18.6
EF
HT
-
-
10.6
EF
HB
-
-
18.6
HT
6.1
8.1
-
60
140
HB
9.1
11.1
-
EF
HT
6.1
8.1
-
EF
HB
9.1
11.1
-
= EF data applies to Explosionproof coils only.
= Some DC solenoid valves can be operated at maximum ambient
temperature of 55°C / 131°F with reduced pressure ratings. See valve
I&M for maximum operating pressure differential ratings.
= Steam Service Valves have a maximum ambient temperature of 55° C/
131°F.
Positioning
This solenoid is designed to perform properly when mounted in any
position. However, for optimum life and performance, the solenoid
should be mounted vertically and upright to reduce the possibility of
foreign matter accumulating in the solenoid base sub
-
assembly area.
Temperature Limitations For Series 8016G Solenoids for use on Valves
Rated at 6.1, 8.1, 9.1, 10.6 or 11.1 Watts
Watt
Rating
Catalog
Number Coil Pre
x
Class of
Insulation
Maximum §
Ambient Temp.
6.1, 8.1, 9.1 &
11.1
None, FB, KF, KP,
SC, SD, SF & SP
F
125°F (52°C)
6.1, 8.1, 9.1 &
11.1
HB, HT, KB, KH, SS, ST
& SU
H
140°F (60°C)
10.6**
None, KF, SF, SC, HT,
KH, ST & SU
F & H
104°F (40°C)
7.1 @ 60Hz
(8.1 @ 50Hz)
F & H
175°F (79°C)*
10.6**
F & H
140°F (60°C)