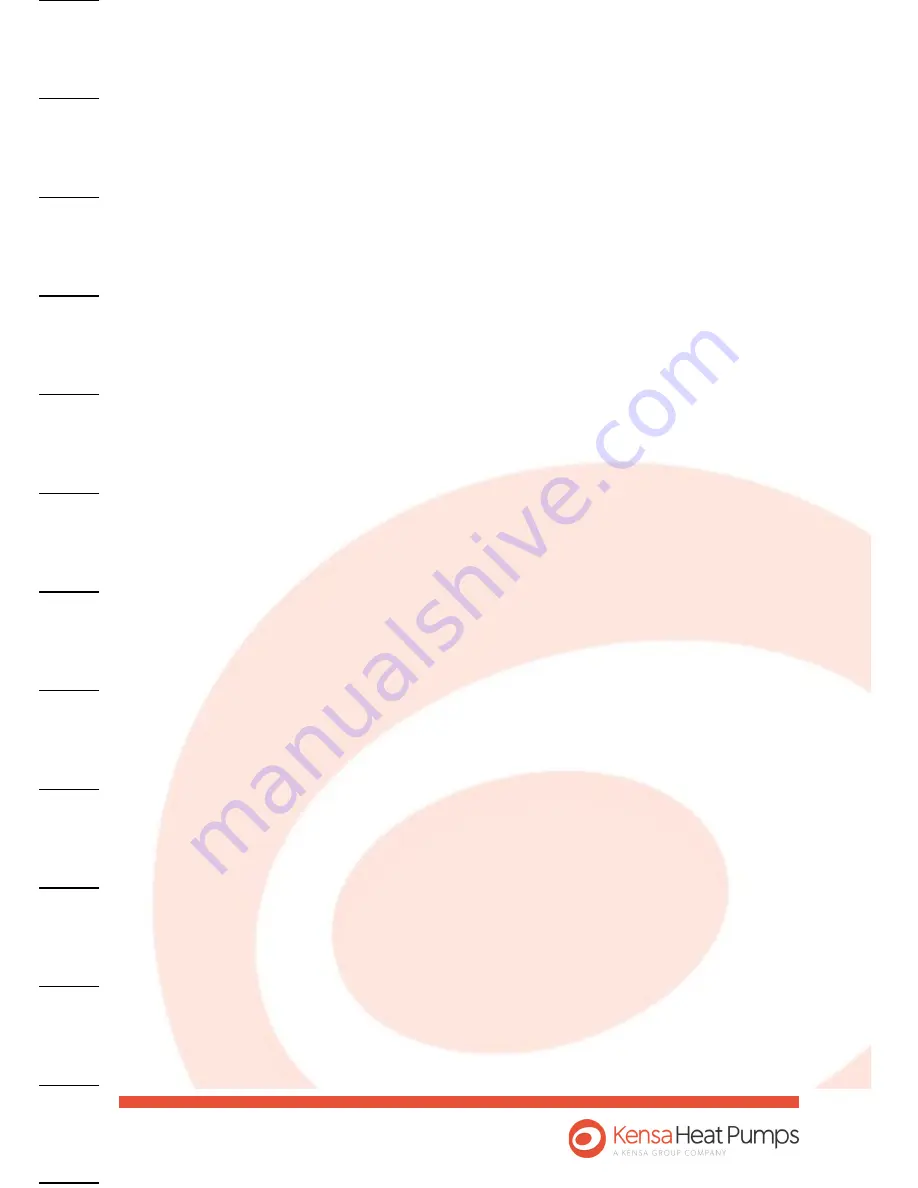
Evo Heat Pump Manual Version 5
Page 2 of 84
Contents Page
Section
Description
Page
1.......................
Introduction ..................................................................................
6
2.......................
Safety Information ........................................................................
7
2.1...........................
Access ......................................................................................................................
7
2.2...........................
Lighting ....................................................................................................................
7
2.3...........................
Tools and consumables ...........................................................................................
7
2.4...........................
Handling ...................................................................................................................
7
2.5...........................
Residual hazards ......................................................................................................
7
2.6...........................
Freezing ...................................................................................................................
7
2.7...........................
Disposal/decommissioning ......................................................................................
7
3.......................
General product information ........................................................
8
3.1...........................
Equipment delivery and handling ............................................................................
8
3.2...........................
Kensa Evo technical details ......................................................................................
9
3.3………………………..
Water Pump Curves
……………………………………………………………………………………………..
10
4.......................
Installation....................................................................................
12
4.1...........................
The Golden Rules of installing a heat pump ............................................................
12
4.2 ..........................
Underfloor heating schematic ................................................................................
12
4.3...........................
Radiators schematic. Space heating only ................................................................
14
4.4…………………………
Second Set Point Schematic
………………………………………………………………………………..
15
4.5...........................
Domestic Hot Water (DHW)
-
Schematic .................................................................
16
4.5.1........................
Type of DHW tank ...................................................................................................
16
4.5.2........................
DHW tank size .........................................................................................................
16
4.5.3........................
Immersion heater ....................................................................................................
16
4.5.4........................
Three Port Diverting Valve ......................................................................................
16
4.5.5........................
Tank Thermostat ......................................................................................................
17
4.5.6........................
DHW Timeclock .......................................................................................................
17
4.5.7........................
Secondary Returns...................................................................................................
17
4.5.8……………………..
Towel Rails
………………………………………………………………………………………………………….
18
4.6...........................
Mechanical Installation ...........................................................................................
20
4.6.1........................
Locating the Heat Pump ..........................................................................................
20
4.6.2……………………..
Removing the transit bolts
…………………………………………………………………………………..
20
4.6.3……………………..
Positioning the unit
……………………………………………………………………………………………..
22
4.6.4........................
Recommended clearances and dimensions.............................................................
22
4.6.5........................
Installation of the heat pump ..................................................................................
23
4.6.6 .......................
Meter Installations...................................................................................................
26
4.6.6.1 ....................
Meter Ready Installations........................................................................................
26
4.6.6.2…………………
Electrical metering
……………………………………………………………………………………………….
28
Safet
y
in
fo
rmatio
n
G
en
e
ral
p
ro
d
u
ct
in
fo
rmatio
n
In
stal
lati
o
n
Me
ch
an
ic
al
in
stal
lati
o
n
Ele
ctr
ic
al
in
stal
lati
o
n
Me
ch
an
ic
al s
et
to
ru
n
Co
n
tr
o
lle
r
Fau
lt
Fin
d
in
g
W
arr
an
ty
H
eat P
u
mp
se
ttin
gs
s
h
ee
t
In
tr
o
d
u
cti
o
n