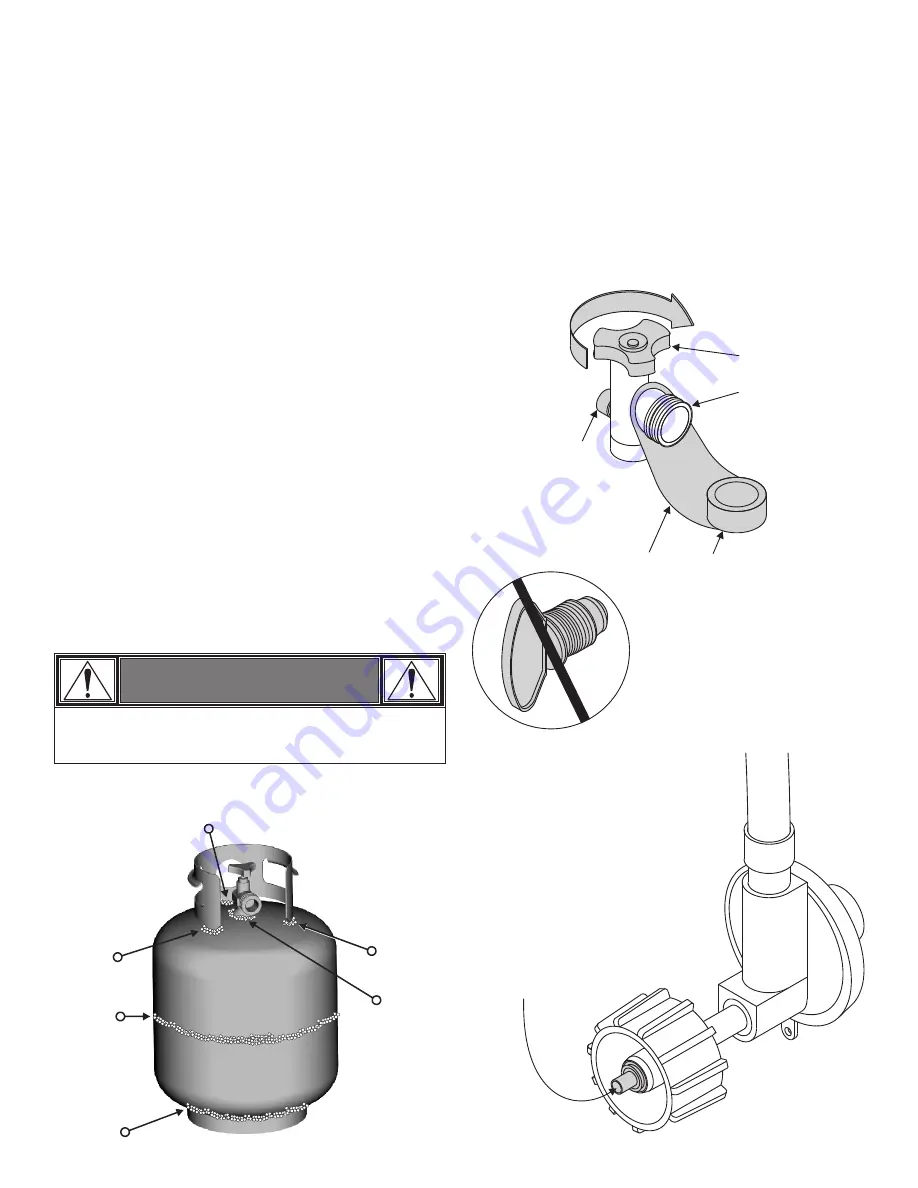
464224011 • 5
LP Tank Exchange
• Many retailers that sell grills offer you the option of
replacing your empty LP tank through an exchange
service. Use only those reputable exchange companies
that inspect, precision fill, test and certify their tanks.
Exchange your tank only for an OPD safety feature-
equipped tank as described in the "LP Tank" section of
this manual.
• Always keep new and exchanged LP tanks in upright
position during use, transit or storage.
• Leak test new and exchanged LP tanks BEFORE
connecting to grill.
• Place dust cap on cylinder valve outlet whenever the
cylinder is not in use. Only install the type of dust cap on
the cylinder valve outlet that is provided with the cylinder
valve. Other types of caps or plugs may result in leakage
of propane.
LP Tank Leak Test
For your safety
• Leak test must be repeated each time LP tank is
exchanged or refilled.
• Do not smoke during leak test.
• Do not use an open flame to check for gas leaks.
• Grill must be leak tested outdoors in a well-ventilated
area, away from ignition sources such as gas fired or
electrical appliances. During leak test, keep grill away
from open flames or sparks.
• Use a clean paintbrush and a 50/50 mild soap and water
solution. Brush soapy solution onto areas indicated by
arrows in figure below. Leaks are indicated by growing
bubbles.
WARNING
If “growing” bubbles appear do not use or move the LP tank.
Contact an LP gas supplier or your fire department!
Do not use household cleaning agents.
Damage to gas
valve/hose/regulator components can result.
Connecting Regulator To The LP Tank
1. LP tank must be properly secured onto grill. (Refer to
assembly section.)
2. Turn all control knobs to the OFF position.
3. Turn LP tank OFF by turning OPD hand wheel clockwise to
a
full stop.
4. Remove the protective cap from LP tank valve. Always use
cap and strap supplied with valve.
Safety Relief Valve
Nipple has to be centered
into the LP tank valve.
OPD Hand Wheel
Type 1 outlet with
thread on outside
ck
w
o
l
is
C
e
f
f
O
Do not insert a POL transport plug
(plastic part with external threads)
It will defeat the Safety Relief
Valve feature.
5. Hold regulator and insert nipple into LP
tank valve. Hand-tighten the coupling
nut, holding regulator in a straight line
with LP tank valve so as not to cross-
thread the connection.
Strap and Cap
into the Type 1 tank valve outlet.
Summary of Contents for 415.1664901
Page 36: ......