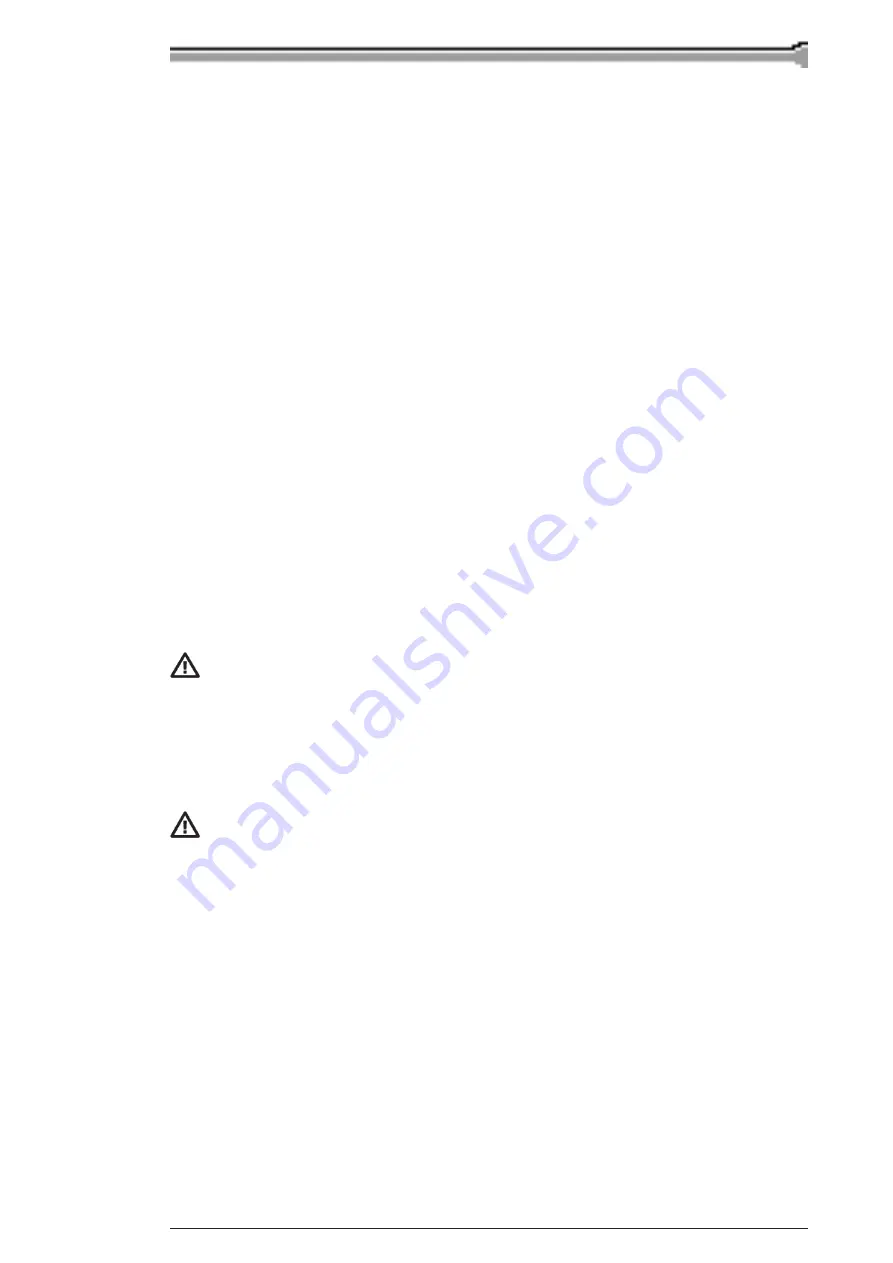
TTC 130, TTC 130F, TTC 160, TTC 160S, TTC 220, TTC 200W, TTC 250W, – 5
TTC 250WS/0109
©
COPYRIGHT
KEMPPI
OY
2.1. CONNECTING TTC-TORCH
Connect torch (and extension parts) according to welding machine’s operation instructions.
Tighten adaptors of torch carefully in order to avoid heating of adaptors, contact disturbances,
mechanical damage and water or gas leakage.
Check by connection of liquid hoses that there are no dirt, metal powder or other
wastes. Wastes may cause blocking in liquid circulation, throughburning of torch
or stopping or breaking of pump.
Connect liquid hoses of torch according to operation instruction of the cooling liquid circulation
unit. (They are fastened to pipe chassis.) Fix liquid hoses (torch – cooling liquid circulation unit)
in such a way that those having red code always are connected to corresponding red counter
connectors and the blue ones respectively to blue counter connectors.
hazards in special welding jobs, eg. for the danger of fire or explosion when welding container
type work pieces. Note! Fire can break out from sparks even several hours after the welding
work has been finished!
Mains voltage
Never take welding machine inside a work piece (eg. container or truck). Do not place welding
machine on a wet surface. Always check cables before operating the machine. Change defected
cables without delay. Defected cables may cause an injury or set out a fire. Connection cable
must not be compressed, it must not touch sharp edges or hot work pieces.
Welding power circuit
Isolate yourself by using proper protective clothing, do not wear wet clothing. Never work
on a wet surface or use defected cables. Do not put TIG-torch or welding cables on welding
machine or on other electric equipment. Do not press TIG-torch switch, if the gun is not directed
towards a work piece.
Welding fumes
Take care that there is sufficient ventilation during welding. Take special safety precautions
when welding metals which contain lead, cadmium, zinc, mercury or beryllium.
If connections cross, cooling liquid is circulating in wrong direction in torch, and
torch handle and neck body might be considerably heatened.
2.2. SWITCH AND REGULATOR OPERATIONS
The TTC torches are equipped with ON/OFF switch. Operation of switch in 2-functions,
4-functions and Minilog positions is described in operation instructions of the welding machine.
TTC torches can be equipped with RTC 10 or RTC 20 torch regulators which are available as
assessory. Regulators can be assembled in place of the original start-switch.
2. INSTALLATION