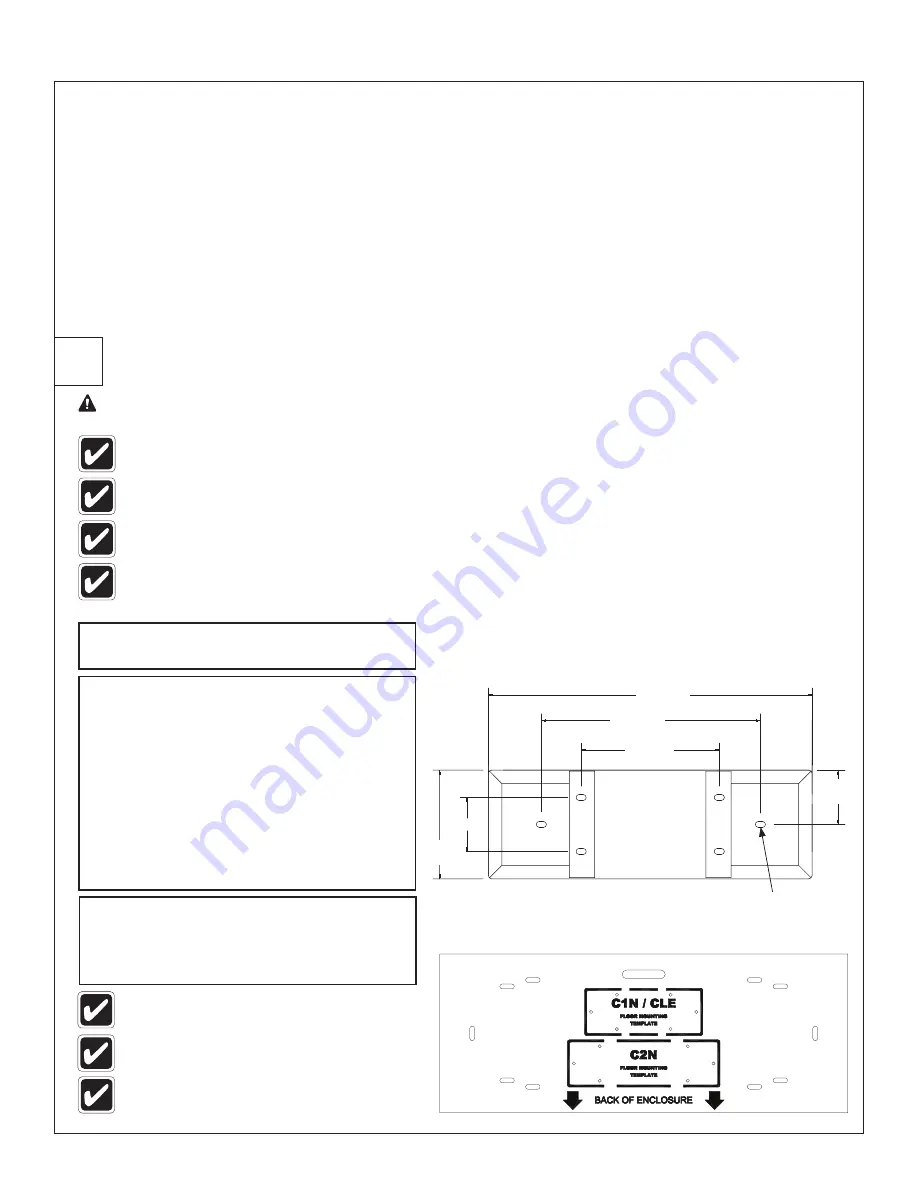
4
C2N Series Tankless Heater
Installation
5/3/2016
Bradley •
215-1821 Rev. B; ECN 16-17-005
Packaging
Crates are constructed from 3/4" (19mm) OSB .
Crate dimensions approx: 44" x 28" x 12" (1118mm x 711mm x 305mm)
Crates should not be stacked more than 2 high .
All crates must be stacked evenly and horizontally .
Safety issues related to packaging:
• Product should be transported with the care associated to packages labeled “FRAGILE” even if packaging is not
marked accordingly .
• Standard safety procedures for forklift transport and large items less than 1000lbs (454 kgs) should be followed at
all times .
• When stored, crate must be supported in entirety of its length and width .
Mounting Heater
1
WARNING HIGH VOLTAGE SHOCK. Disconnect power supply before performing any work inside
the heater enclosure.
A
Set heater in a vertical, upright position
with the water outlet located at top .
B
Standard Wall Mount
Mount heater to the wall using the (4)
mounting brackets on the back of the
enclosure . Bolt the heater to the vertical
surface . Vertical surface must support
150 lbs or more .
Optional Leg Kit
Use the floor mounting template on the
side of the crate to help with alignment .
Secure heater by bolting each leg to the
floor using 3/8" (10mm) anchor bolts .
C
Install the pressure and temperature relief
valve on hot water outlet immediately
following the union .
NOTICE! Valve must empty into a drain.
For best results, install heater as close as possible to the point of use.
Installation should be performed by a qualified plumber or electrician.
Long pipe runs are not recommended. A heat loss of 1°F for every 10ft (3 meters) of uninsulated
pipe can occur.
When determining a mounting location, give consideration to the location of the main electrical panel
and ensure accessibility of the cabinet enclosure door and other plumbing for service/maintenance. 36"
(914mm) minimum in front of the cabinet enclosure is required.
24"
(609mm)
16¼"
(413mm)
10¼"
(260mm)
4"
(102mm)
4"
(102mm)
8"
(203mm)
⁷⁄₁₆
" x ¾"
(10mm x 20mm)
Slot
(6 Places)
Rectangle outlines on template are not
actual size of heater.
Template may require cutting to fit into
tight areas.
Holes are for alignment purposes and may
not represent actual drill size for mounting
hardware.