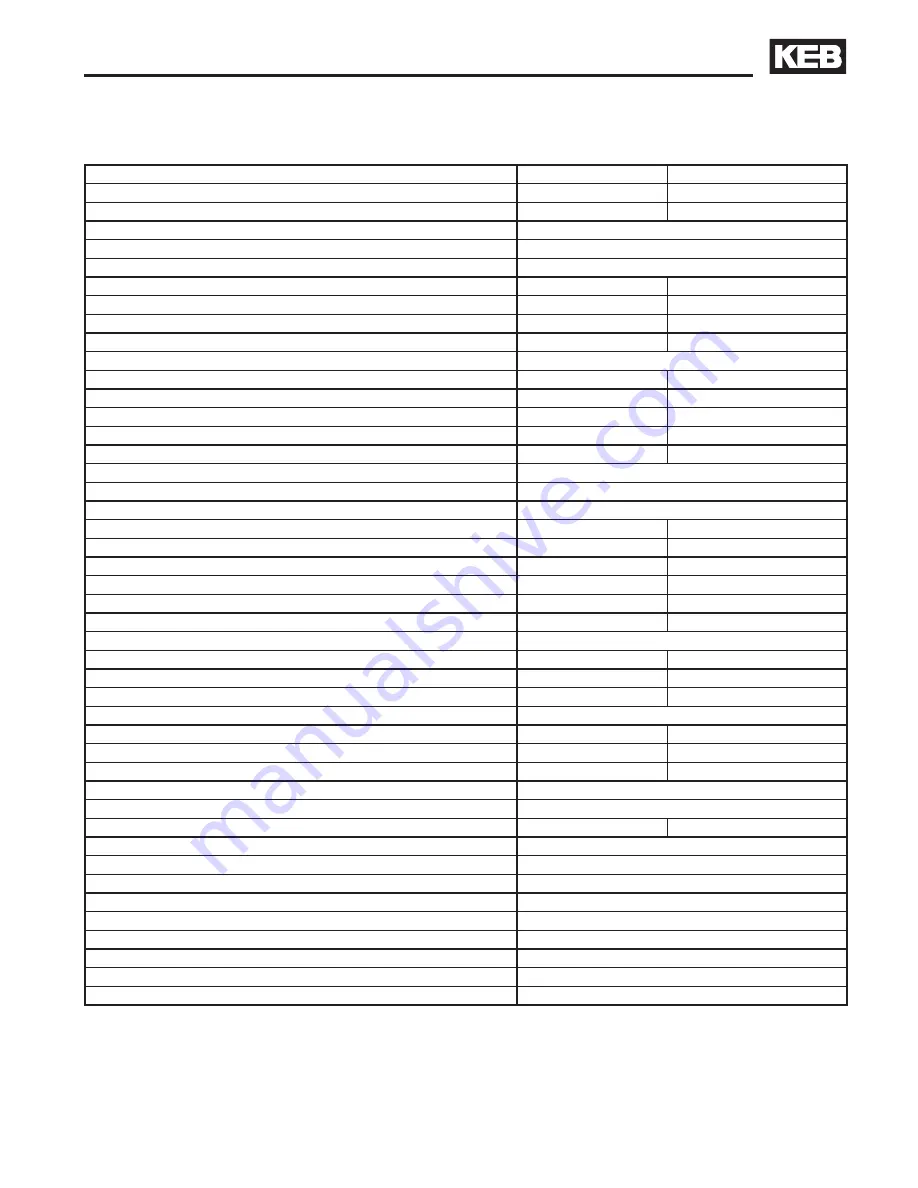
7
2.3 Technical Data
2.3.1 230 V-class
Product Description
Inverter Size
05
07
Recommended Motor Power
[hp]
1/2
1
Housing size
A
A
Input Ratings
Supply voltage
[V]
180...260 ±0 (230 V rated voltage)
Supply voltage frequency
[Hz]
50 / 60 +/- 2
Input phases
1
1
Rated input current
[A]
4,6
8
Maximum input fuse
[A]
10
15
Recommended wire gauge [awg]
14
14
Output Ratings
Rated output power [kVA]
0,9
1.6
Rated motor power
[kW]
0.37
0.75
Rated output current
[A]
2.3
4.0
Peak current (30 seconds)
[A]
4,1
7.2
Over current fault (E.OC) trip level
[A]
5.0
8.6
Overload curve (see annex)
1
Output voltage
[V]
3 x 0...V input
Output frequency
[Hz]
0…400Hz
Rated switching frequency
[kHz]
4
8
Maximum switching frequency
[kHz]
8
8
Power loss at rated operation
1)
[W]
30
60
Stall current at 4kHz
[A]
2.3
4
Stall current at 8kHz
[A]
2.3
4
Stall current at 16kHz
[A]
–
–
Braking Circuit
Min. braking resistance
2)
[Ω]
100
100
Typ. braking resistance
2)
[Ω]
180
100
Max. braking current
[A]
4.5
4.5
Installation Information
Max. shielded motor cable length at 4 kHz
3)
[ft]
30
30
Max. shielded motor cable length at 8 kHz
3)
[ft]
30
30
Max. shielded motor cable length at 16kHz
3)
[ft]
–
–
Tightening torque for terminal strip [in lb]
Not applicable
Environmental
Max. heat sink temperature TOH
[°C] 100°C / 212 °F
95°C / 203°F
Storage temperature
[°C]
-25...70 °C / -13…158°F
Operating temperature
[°C]
-10...45 °C / 14…113°F
Housing design / protection
Chassis / IP20
Relative humidity
max. 95% without condensation
Approvals
Tested in accordance with…
EN 61800-3 /UL508C
Standards for emitted interference
EN 55011 Class B / EN 55022 Class A
Standards for noise immunity
IEC 1000-4-2 / -3 / -4 / -5/ -6
Climatic category
3K3 in accordance with EN 50178
1) Rated operation means rated switching frequency, rated voltage, and rated output current.
2) Only for units with the braking circuit installed.
3) Maximum cable length is based on the the use of shield motor cables, ground current limitations, EMI levels
set forth in EN55011. Contact KEB for more information.