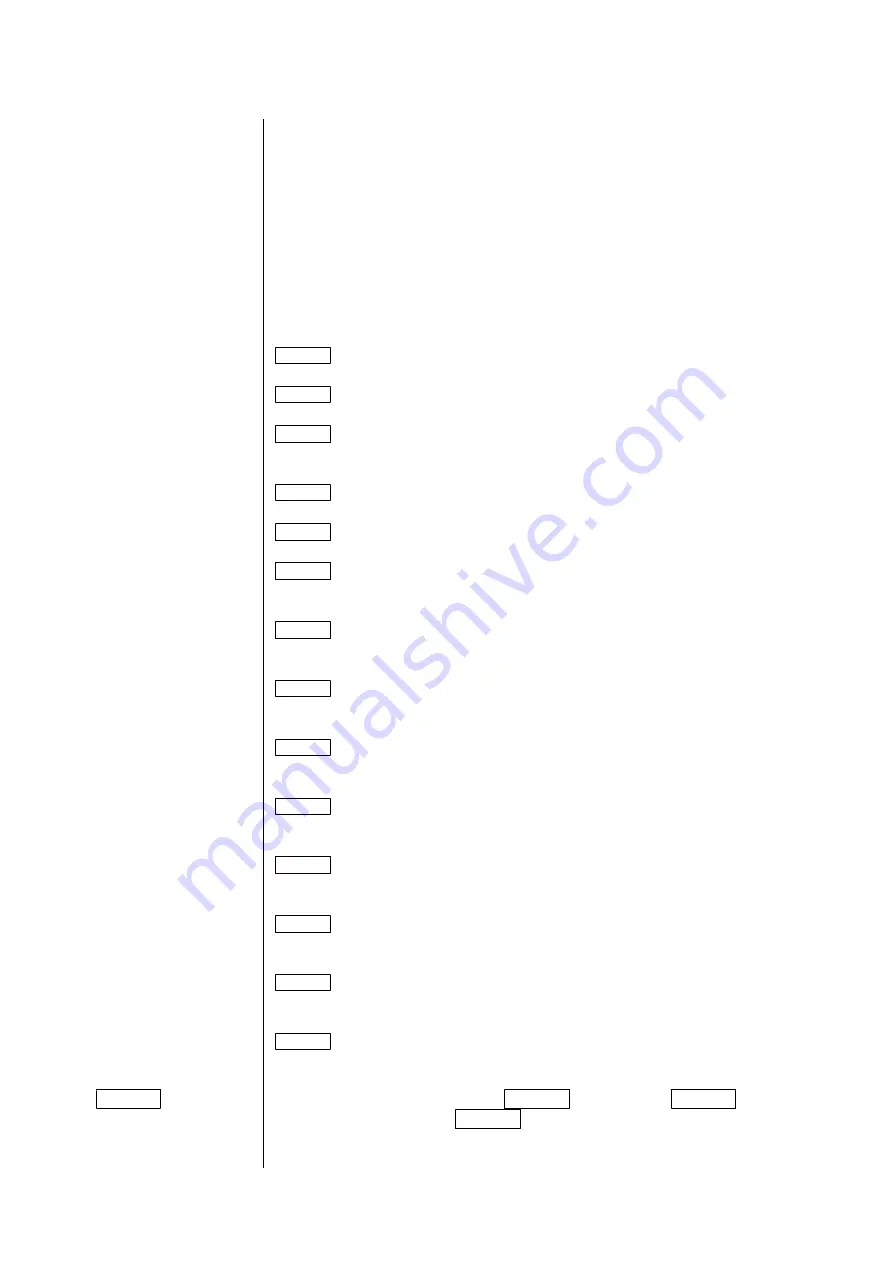
- 22 -
Error Messages
■
When the error codes shown below are displayed we recommend you to
contact the manufacturer. The following errors may sometimes be displayed
in cases when there is extreme interference. Please turn off the unit and on
again to see if the error code persists.
The followings are considered to be possible sources of interference.
Lightning strikes
・
Induction or arc casting machine in the vicinity
・
Radio transmitter in the vicinity
・
Induction motor in the vicinity
・
Unit unable to read power outlet frequency
Control system is malfunctioning
Memory function is abnormal
RAM malfunction for program parameters, default values etc.
Malfunction of chamber clockwise rotation
Malfunction of chamber counter clockwise rotation
Power control to muffle heater is malfunctioning
Possibly muffle heater breakdown is anticipated
Thermocouple is malfunctioning
Thermocouple breakdown is anticipated
Abnormal memory
Data in memory is out of normal programmable range
Abnormal heat rise
The error code is displayed when the muffle heat is abnormally high
Device malfunction of current flow to muffle heater
Computer detects current flow signal despite no current is flowing to heater
Malfunction of temperature detection device
Temperature signal is not received from thermocouple
Abnormal over pressure
Chamber pressure is higher than set level
Abnormal low pressure
Chamber pressure is lower than set level
Abnormal control P.C.B.
The error code is displayed in case the P.C.B is out of control.
is displayed
When the unit is re-booted after
is displayed,
is
●
displayed. The trouble of
should be solved for machine operation.
We recommend you to contact dealer/manufacturer for trouble shooting.