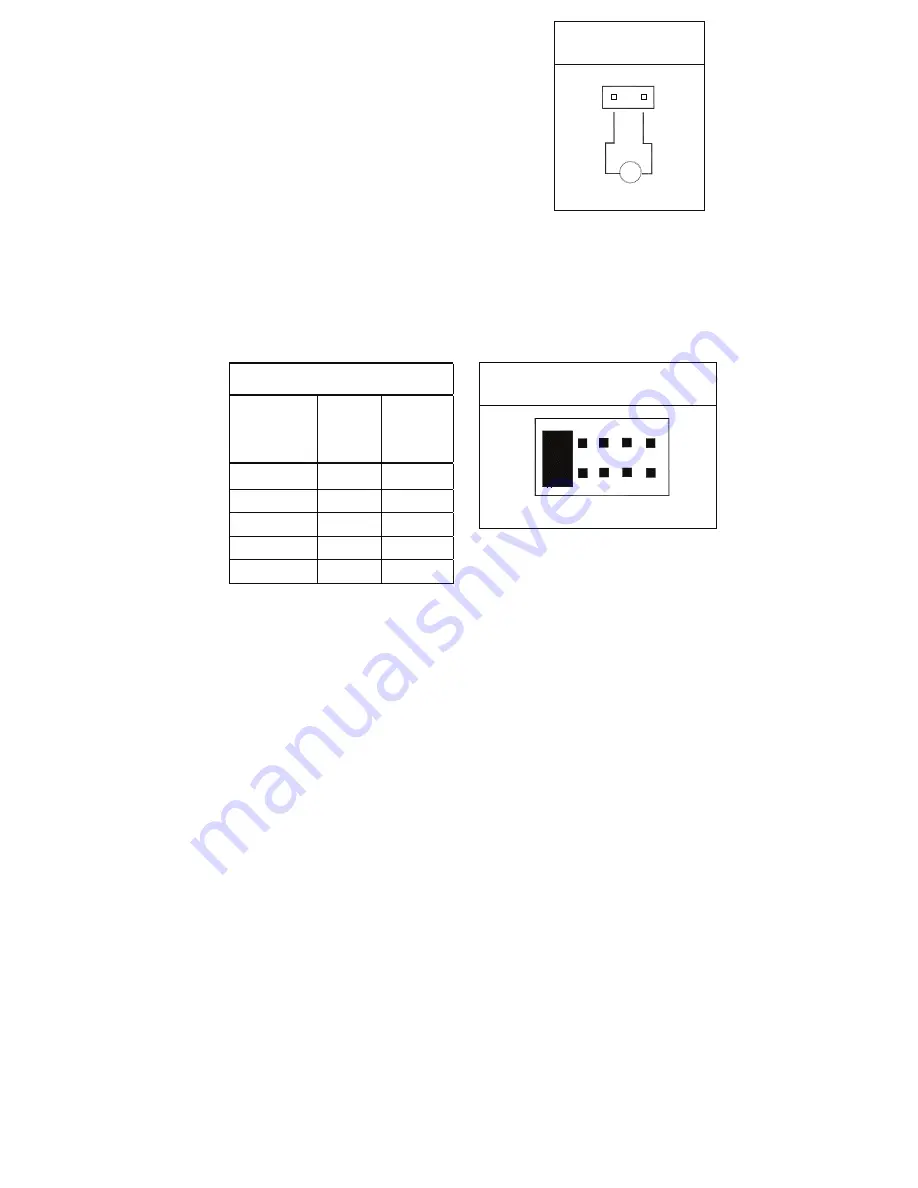
19
6.11 Tach-Generator Feedback, J1
–
The KBRG-212D is
factory set for armature feedback which provides good
load regulation for most applications. For superior
load regulation analog tach-generator feedback can
be used.
Connect the tach-generator to J1, so that the polarity
of the tach-generator is the same with respect to the
input signal polarity.
Note:
If tach-generator is wired for reverse polarity,
the motor will run at full speed. See Figure 9.
7
SETTING SELECTABLE JUMPERS
The KBRG-212D has customer selectable jumpers which must be set before the control
can be used. See Figure 1, on page 10 for jumper locations.
7.1 J2 – Armature Current
– Select the J2 position (1.7, 2.5, 3.3, 5, 7.5) closest to the
rated motor current. See Figure 10 and Table 9.
Note:
The maximum output current is set to 150% of the J2 position, which may be reset
using the FCL and RCL Trimpots. See Section 10.3, on page 26.
FIGURE 9 –
J1 -TACH-GENERATOR
FEEDBACK
+ -
G
J1
+ -
FIGURE 10 - J2 – ARMATURE
CURRENT JUMPER
(SHOWN IN FACTORY SETTING)
2.5A
7.5A
1.7A
3.3A
5.0A
J2
TABLE 9 –
MOTOR HORSEPOWER
J2 Position
Motor
Current
(DC Amps)
90 VDC
180 VDC
7.5A 3/4 1
½
5.0A 1/2 1
3.3A 1/3 3/4
2.5A 1/4 1/2
1.7A 1/6 1/3