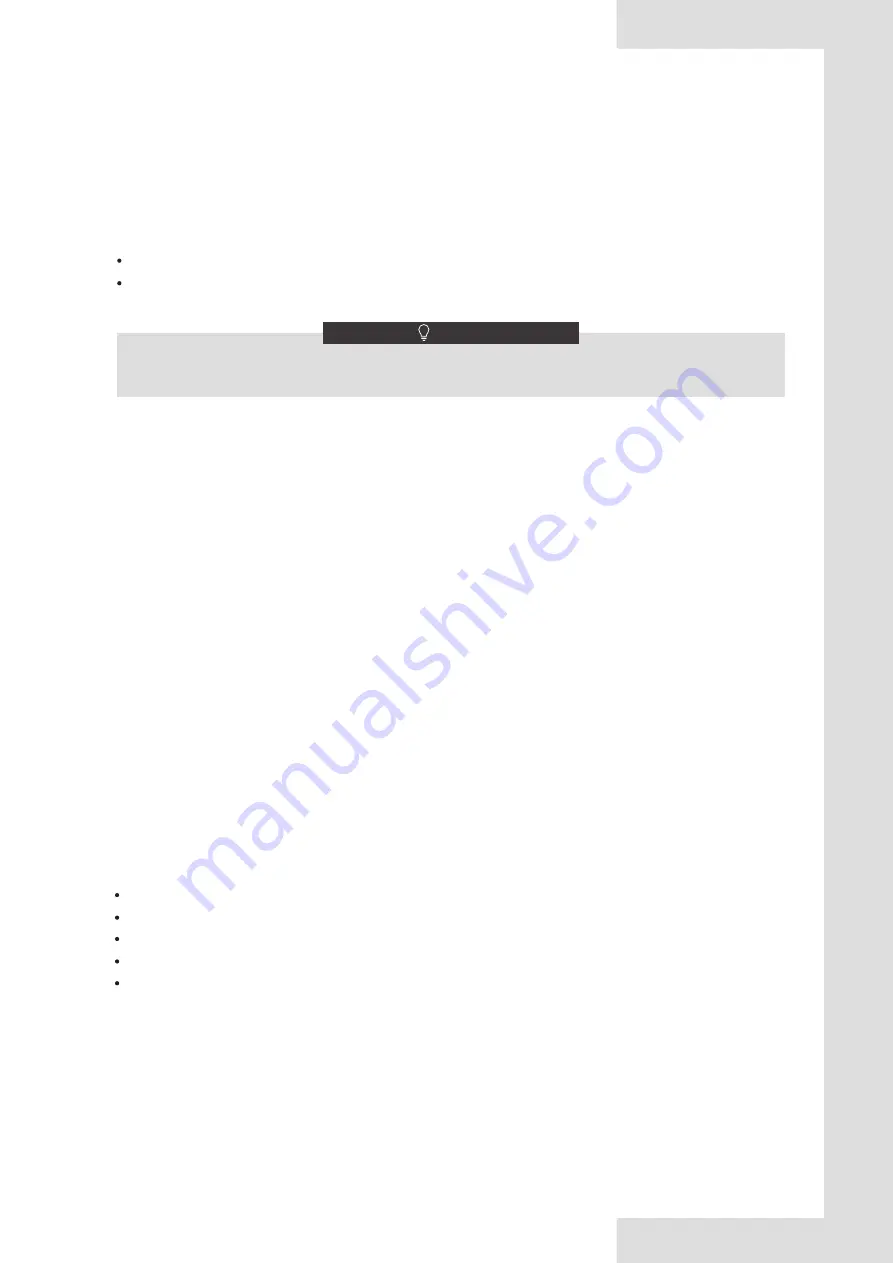
78
a) During repairs to sealed components, all electrical supplies shall be disconnected from the equipment being worked upon
prior to any removal of sealed covers, etc. If it is absolutely necessary to have an electrical supply to equipment during servicing,
then a permanently operating form of leak detection shall be located at the most critical point to warn of a potentially hazardous
situation.
b) Particular attention shall be paid to the following to ensure that by working on electrical components, the casing is not altered
in such a way that the level of protection is affected. This shall include damage to cables, excessive number of connections,
terminals not made to original specification, damage to seals, incorrect fitting of glands, etc.
10) Repairs to sealed components
Ensure that apparatus is mounted securely.
Ensure that seals or sealing materials have not degraded such that they no longer serve the purpose of preventing the
ingress of flammable atmospheres. Replacement parts shall be in accordance with the manufacturer s specifications.
11) Repair to intrinsically safe components
Do not apply any permanent inductive or capacitance loads to the circuit without ensuring that this will not exceed the
permissible voltage and current permitted for the equipment in use. Intrinscially safe components are the only types that can be
worked on while live in the presence of a flammable atmosphere. The test apparatus shall be at the correct rating. Replace
components only with parts specified by the manufacturer. Other parts may result in the ignition of refrigerant in the atmosphere
from a leak.
12) Cabling
Check that cabling will not be subject to wear, corrosion, excessive pressure, vibration, sharp edges or any other adverse
environmental effects. The check shall also take into account the effects of aging or continual vibration from sources such as
compressors or fans.
13) Detection of flammable refrigerants
Under no circumstances shall potential sources of ignition be used in the searching for or detection of refrigerant leaks. A halide
torch (or any other detector using a naked flame) shall not be used.
14) Leak detection methods
The following leak detection methods are deemed acceptable for systems containing flammable refrigerants. Electronic leak
detectors shall be used to detect flammable refrigerants, but the sensitivity may not be adequate, or may need
re-calibration.(Detection equipment shall be calibrated in a refrigerant-free area.) Ensure that the detector is not a potential
source of ignition and is suitable for the refrigerant. Leak detection equipment shall be set at a percentage of the LFL of the
refrigerant and shall be calibrated to the refrigerant employed and the appropriate percentage of gas (25% maximum) is
confirmed. Leak detection fluids are suitable for use with most refrigerants but the use of detergents containing chlorine shall
be avoided as the chlorine may react with the refrigerant and corrode the copper pipe-work. If a leak is suspected ,all naked
flames shall be removed or extinguished. If a leakage of refrigerant is found which requires brazing, all of the refrigerant shall
be recovered from the system, or isolated(by means of shut off valves) in a part of the system remote from the leak . Oxygen
free nitrogen(OFN) shall then be purged through the system both before and during the brazing process.
15) Removal and evacuation
When breaking into the refrigerant circuit to make repairs of for any other purpose conventional procedures shall be used,
However, it is important that best practice is followed since flammability is a consideration. The following procedure shall be
adhered to:
Remove refrigerant;
Purge the circuit with inert gas;
Evacuate;
Purge again with inert gas;
Open the circuit by cutting or brazing.
The use of silicon sealant may inhibit the effectiveness of some types of leak detection equipment. Instrinsically safe
components do not have to be isolated prior to working on them.
NOTE
The refrigerant charge shall be recovered into the correct recovery cylinders. The system shall be flushed with OFN to render
the unit safe. This process may need to be repeated several times.
Compressed air or oxygen shall not be used for this task.
Flushing shall be achieved by breaking the vacuum in the system with OFN and continuing to fill until the working pressure is
achieved, then venting to atmosphere, and finally pulling down to a vacuum. This process shall be repeated until no refrigerant
is within the system.
When the final OFN charge is used, the system shall be vented down to atmospheric pressure to enable work to take place.
This operation is absolutely vital if brazing operations on the pipe-work are to take place.
Ensure that the outlet for the vacuum pump is not closed to any ignition sources and there is ventilation available.
Summary of Contents for Aquantia KHP-MO 4 DVR2
Page 2: ......
Page 23: ...19 Tank booster heater n d e d n d Automatic air purge valve r d r manometer d r...
Page 74: ...70 9 5 10 4...
Page 84: ...20 21 Automatic air purge valve Pressure relief valve...
Page 87: ...16125300002999 V C...
Page 88: ......