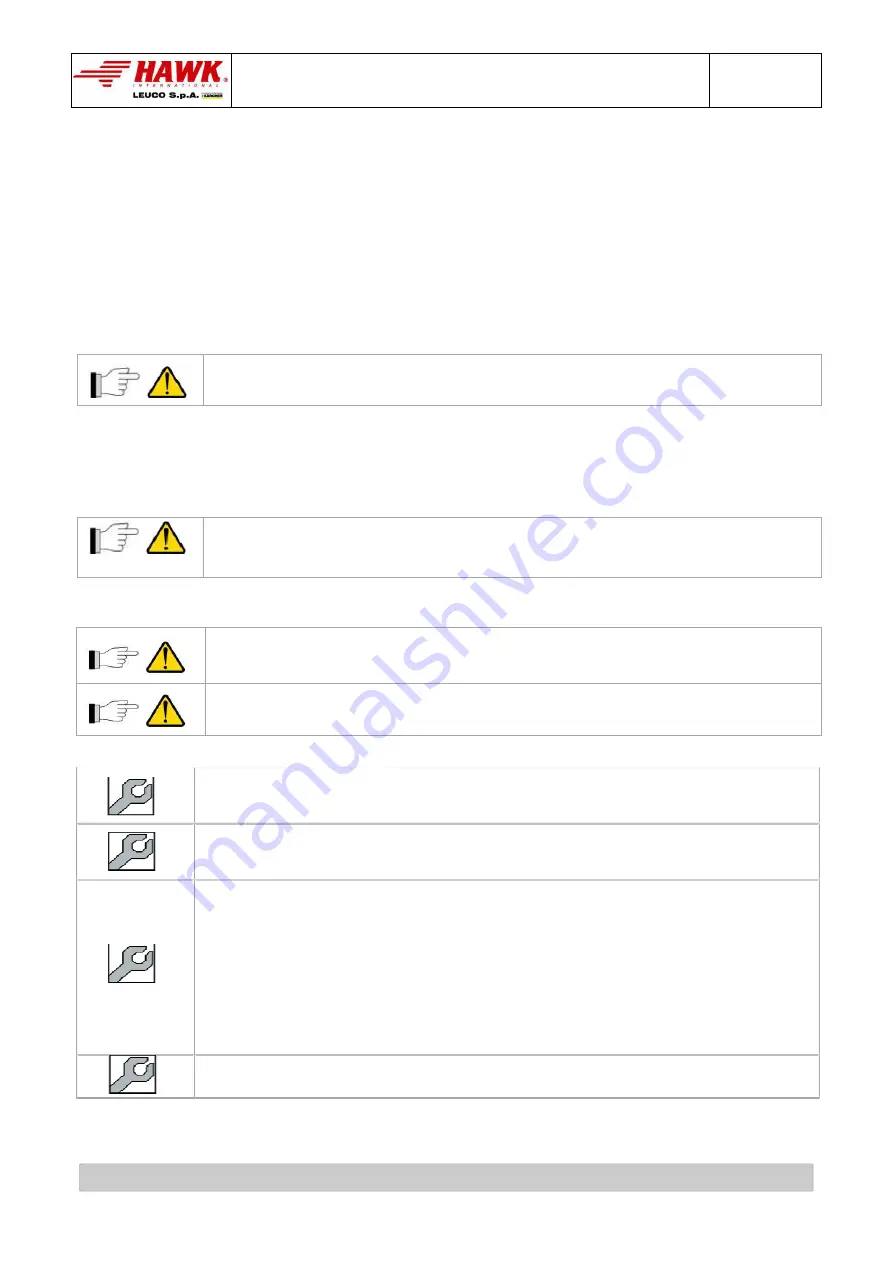
This Manual is the exclusive property of the Manufacturer. Reproduction, in any form whatsoever, even partially, is prohibited.
Instruction Manual
High pressure piston pumps – Series NMT-EBCW, NMT-EBCH, XLTI-EBCH, XLTI-ESA
Rev. 0
Page 17 of 25
4.2
Prohibited use
The equipment must not be used:
•
by different users from those specified in section 1.1.2;
•
for different uses from those specified in Chapter 2 and section 4.1;
•
in different ambient conditions from those specified in section 2.2;
•
in different end machines from those specified in section 4.1;
•
with different fluids from those listed in Chapter 2;
•
in waterworks for drinking water;
•
for foodstuff applications;
•
for pharmaceutical products.
Should the equipment be operated for other uses than those specified above, the Manufacturer shall be
entitled to review the warranty conditions.
5
ASSEMBLY AND INSTALLATION
Read this chapter carefully before installing the machine.
Incorrect installation of your pumping system may cause injuries to people and damage to property. So, it
is essential to comply with all instructions listed below.
The pumps can be installed in various ways: with pulley drive, direct drive or with flange coupling.
Use a suitable flexible coupling for direct coupling with an electric motor
Make sure the pulleys are aligned if pulley driven; adjust the belt tension and provide adequate safety
protection.
The pump must be installed horizontally to the base to facilitate optimised lubrication on a vibration-free base.
The motor rotation direction must be the same as the eccentric shaft (direction marked on the shaft).
The pump inlet line must be sized according to the flow rate and its diameter for fluid flow must in no case be
inferior to the inlet diameter. The line must have as little constrictions as possible (elbows, T-fittings, reduced
diameter, etc.). Each joint in the inlet line must be properly insulated using Teflon tape or a similar product in
order to prevent air leaks or intake (cavitation). Cavitation consists in the formation of vapour bubbles in a liquid
whose implosion generates abnormal and very harmful stresses on all the pump components. For longer pump
service life fluids with sand or other solid particles must not be circulated in the pump as they jeopardise the
efficiency of the valves, pistons and seals.
This can be avoided by fitting a filter on the inlet pipe - oversized with respect to the pump flow rate - which shall
be subjected to periodic cleaning.
The delivery line must be suitable to resist the pump working pressure. Very narrow transit areas may cause
pressure losses to the nozzle.