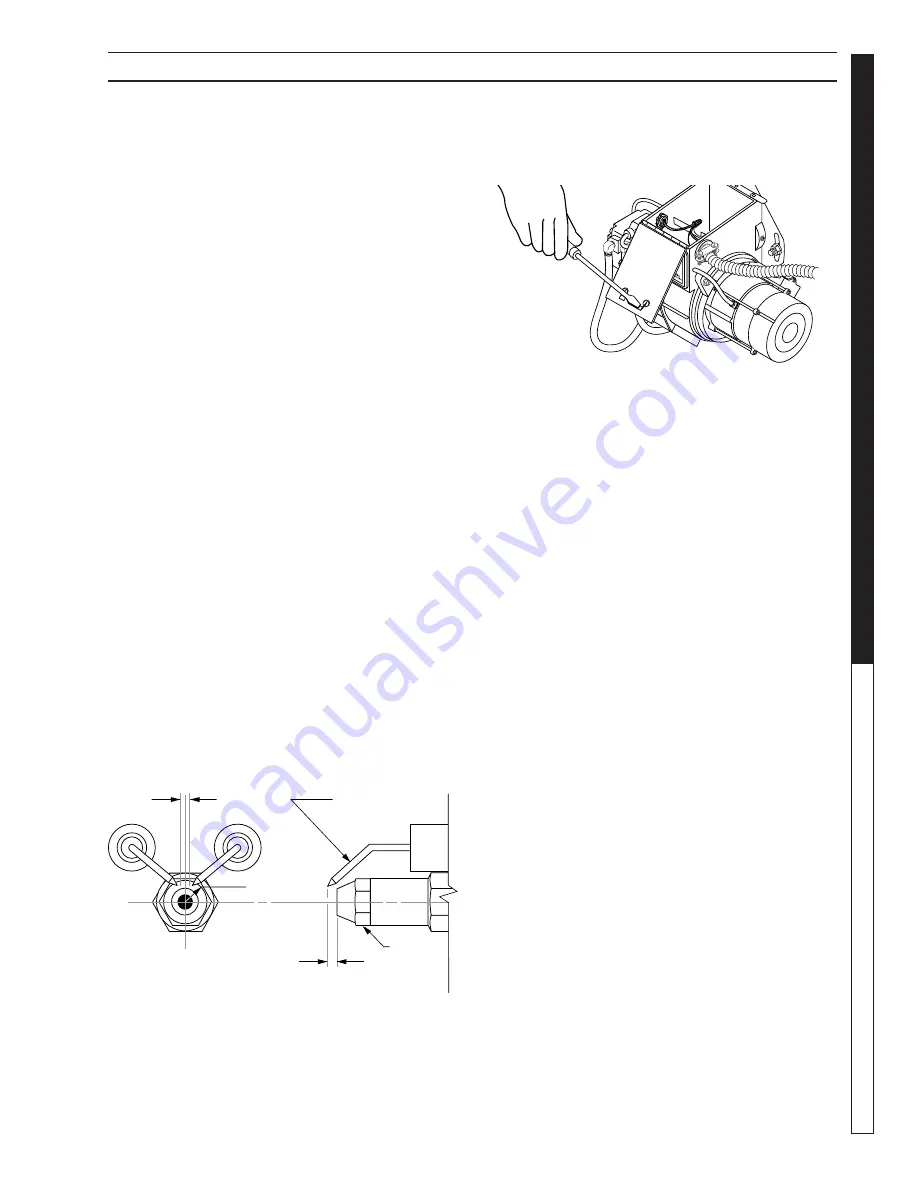
8.917-208.0 • HOT • Rev. 05/17
13
PRESSURE W
ASHER
OPERA
TOR’S MANU
AL
MAINTENANCE & SERVICE
Step 3 Attach a short section (3-5 ft.) of garden hose
to machine to siphon solution from an elevated
container. Turn machine on, allowing solution
to be pumped through coils back into the con-
tainer. Solution should be allowed to circulate
2-4 hours.
Step 4 After circulating solution flush entire system with
fresh water. Reinstall high pressure nozzle into
wand.
Rupture Disk
If pressure from pump or thermal expansion should
exceed safe limits, the rupture disk will burst, allow-
ing high pressure to be discharged through hose
to ground. When the disk ruptures it will need to be
replaced. Torque the replacement rupture disk to 35
foot pounds.
Fuel
Use clean fuel oil that is not contaminated with water
and debris. Replace fuel filter and drain tank every
100 hours of operation. Use No. 1 or No. 2 Heating
Oil (ASTM D306) only.
NEVER use gasoline in your
burner tank. Gasoline is more combustible than fuel
oil and could result in a serious explosion.
NEVER
use crankcase or waste oil in your burner. Fuel unit
malfunction could result from contamination.
Biodiesel fuels are becoming more popular as alter-
native fuels under the Green Initiative. Landa en-
dores the use of fuels that are blended with biodies-
els meeting ASTM D6751 and petroleum
fuels meeting ASTM D396. Landa offers no
opinion regarding the combustion characteristics
of B5 blends. B5 biodiesel fuels are 5% ASTM
D6751 biodiesel and 95% ASTM D396 fuel oil blend.
Electrode Setting
(See illustration below.)
Ignition Circuit
Periodically inspect wires, spring contact and elec-
trodes for condition, security and proper spacing.
Transformer test:
(CAUTION 10,000 VOLTS) use
defect free insulated screwdriver and keep fingers
Side View
Top View
1/16"
7/16"
5/32" Gap
Electrode
Nozzle
off blade! Lay blade across one contact: OK if arc
will span 1/2" between end of blade and other
contact (see illustration below).
Transformer Check
Burner Nozzle
Keep the tip free of surface deposits by wiping it with
a clean, solvent-saturated cloth, being careful not to
plug or enlarge the nozzle. For maximum efficiency,
replace the nozzle each season.
Fuel Control System
These machines utilize a fuel solenoid valve located
on the fuel pump to control the flow of fuel to the
combustion chamber. This solenoid, which is nor-
mally closed, is activated by the unloader's pressure
switch. When an operator releases the trigger on the
spray gun, the unloader goes into a by-pass mode,
thus stopping electrical current to the fuel solenoid
coil. With the solenoid closed, the fuel supply to the
combustion chamber ceases. Periodic inspection to
insure that the fuel solenoid valve functions properly
is recommended. This can be done by operating the
machine and checking to see that when the spray
gun is in the OFF position the burner is not firing.
Fuel Pressure Adjustment:
To adjust fuel pressure, turn the adjusting screw
(located at the regulator port) clockwise to increase,
counterclockwise to decrease. Do not exceed 200 psi.
NOTE: When changing fuel pump, a by-pass plug
must be installed in return line port or fuel pump
will not prime.
To adjust fuel pressure, First install a pressure gage
into the port just after the pump fuel exit. Turn the ad-
justing screw (located at the regulator port) clockwise
to increase, and counterclockwise to decrease. Do
not exceed 200 psi or lower the pressure below 130
PSI, when checked at the post-pump pressure port.
The fuel pressure may need to be adjusted due to
altitude. For every 500 ft altitude above sea level, the
boiling point of water goes down 1 °F. At high altitude
environments, this boiling point change may require
the heat input to be lowered so the water input does
not turn to steam earlier than at the factory settings
Summary of Contents for Landa HOT 2-1100
Page 2: ......
Page 20: ...Form 8 917 208 0 Revised 05 17 Printed in U S A ...