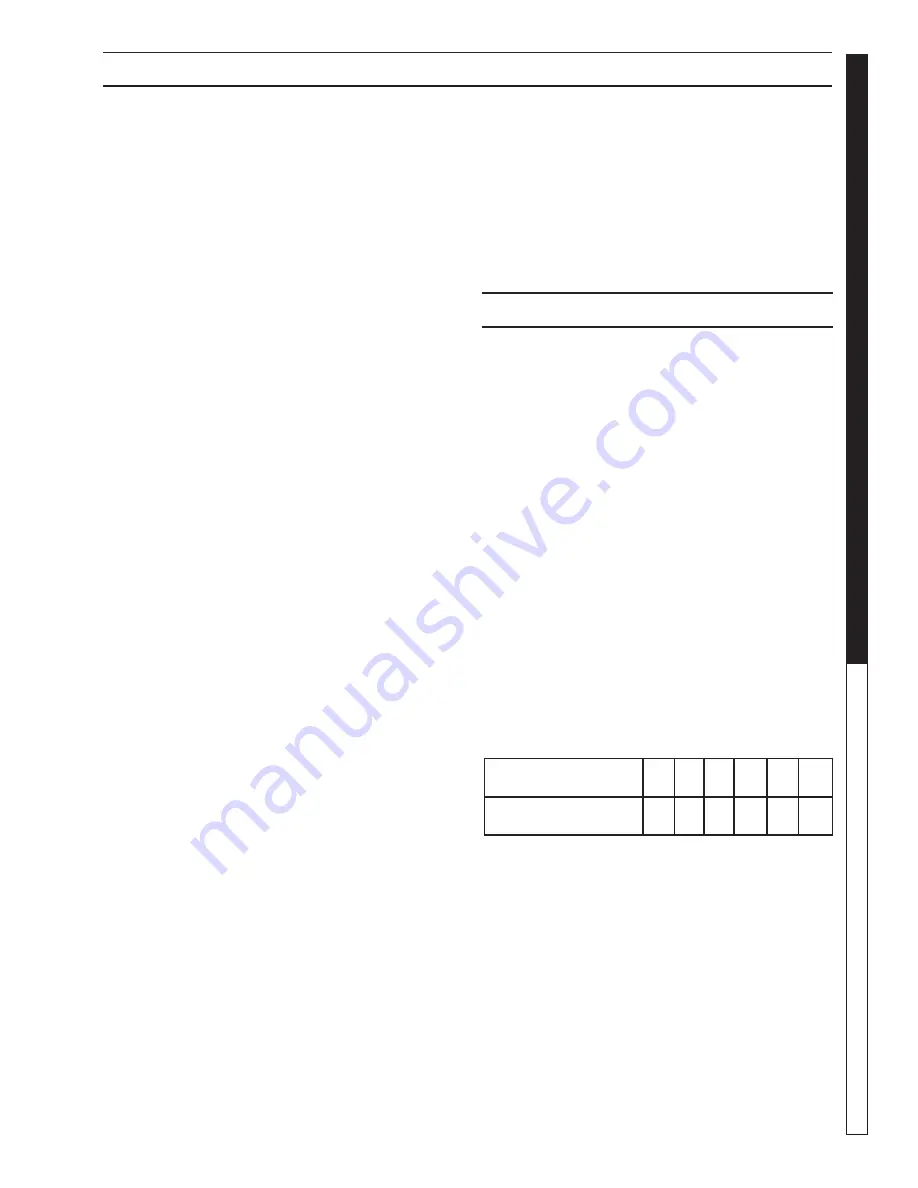
715-721 • HDS-NG LP • 9.800-160.0 • Rev. 4/10
19
PRESSURE WASHER
OPERATOR’S MANUAL
Spray Nozzles:
Each machine is equipped with one or more spray
nozzles, depending on the model. Different spray noz-
zles are calibrated for each machine, depending on
the flow and pressure of that particular model. Spray
nozzles vary in bore size and angle of spray. Popular
spray angles are 0°, 15°, 25°, 40°. When ordering,
please specify size and angle of nozzle. Nozzle size
for each machine is located on the serial plate.
Unloader Valves:
Unloader valves relieve pressure in the line when a
spray gun is closed. Unloader valves are preset and
tested at the factory before shipping. Occasional ad-
justment of the unloader may be necessary to main-
tain correct pressure. For valve adjustment contact
your nearest dealer.
Note: Tampering with the factory
setting may cause personal injury and/or property
damage, and will void the manufacturer's warranty.
Winterizing Procedure:
Damage due to freezing is not covered by warranty.
Adhere to the following cold weather procedures when-
ever the washer must be stored or operated outdoors
under freezing conditions.
It is necessary to protect your machine against freez-
ing when temperatures drop below 32° F. Siphoning a
small amount of antifreeze into the system is recom-
mended. This is done by pouring a 50-50 mix of anti-
freeze and water into the float tank and then siphoning
100% antifreeze through the detergent line with the
pump on. If compressed air is available, an air fitting
can be screwed into the float tank strainer fitting, and
by injecting compressed air, all water will be blown out
of the system. The use of a draft diverter will prevent
the wind chill factor from freezing the coil.
Low Pressure Diagnosis:
(Machines with spray gun)
Refer to Troubleshooting Chart for low pressure. If the
trouble is found to be either the unloader or the pump,
your next step is to determine which is the problem.
This can be done by eliminating the unloader from the
system and attaching the 50' discharge hose directly
to the pump. If high pressure is developed in this man-
ner, the pump is good and the unloader needs to be
repaired or replaced. If low pressure is still present,
then the pump needs repairing.
CAUTION: When using this procedure to test com-
ponents keep the spray gun open at all times.
High Limit Hot Water Thermostat:
For safety, each machine is equipped with an ad-
justable thermostat. In the event the temperature of
the water should exceed its operating temperature,
the thermostat will turn the burner off until the water
cools.
Pumps:
Use only SAE30 weight non-detergent oil. Change oil
after first 50 hours of use. Thereafter, change oil every
three months or at 500 hour intervals. Oil level should
be checked through use of the dipstick found on the
top of the pump or by the red dot visible through the oil
gauge window. Oil should be maintained at that level.
HEATING COILS
To Check Water Heater Coil for Leaks:
With the main burners "OFF" start the pumping unit
and allow it to run for a few minutes. With a drop light
or flashlight, check the burner compartment. If no
leaks are visible and water is dripping from the coils,
then it is condensation from the flue gases when the
burners are on.
Condensation from Heating Coil:
When cold water is being pumped into the water heater
coils and the burners are on, condensation will form
on the coils and drip down into the burner compart-
ment. This will give the appearance of a leaking coil,
particularly on cold humid days.
Scale Protection:
1. Fill container with Karcher scale inhibitor fluid
Rm 110 (Order No. 0.500-110.0).
2. Obtain water hardness values from local water
authority, or using a water hardness testing kit.
3. Adjust impulse transmitter in electric cabinet (pre-
set at #5).
When operating unit without a scale protection, the
heater coil may become scaled.
Gas Valve Regulator Adjustment:
Adjustment of the built-in regulator isn’t normally nec-
essary, since it is preset at the factory. However, field
adjustment may be accomplished as follows:
1. Attach manometer at both inlet and outlet pressure
ports.
2. Remove manifold pressure adjustment screw
cap.
3. With small screwdriver, rotate manifold pressure
adjustment screw clockwise to increase or coun-
terclockwise to decrease gas pressure.
MAINTENANCE & SERVICE
Water hardness (
2
dH)
5
10 15 20 25 30
Impulse transmitter
10
8
7 6.5
6
5.5