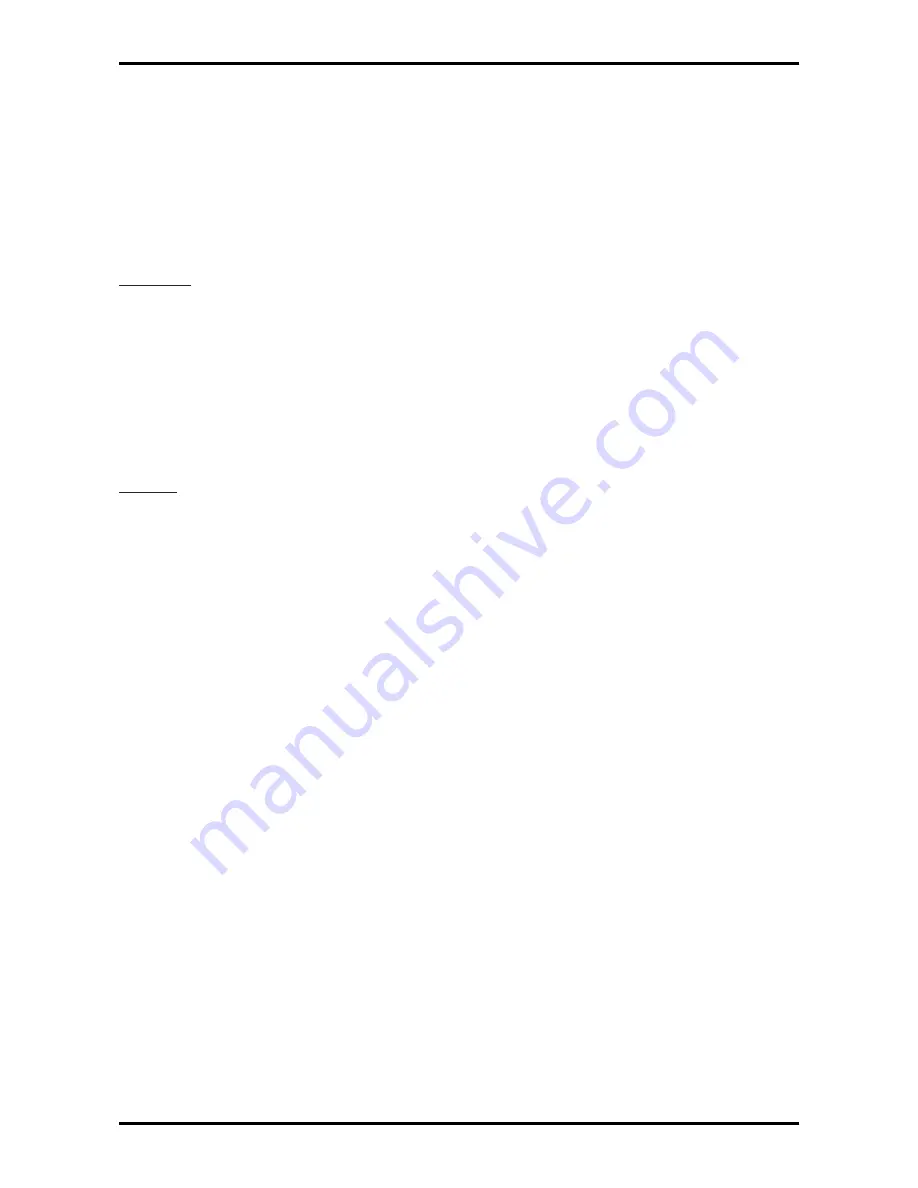
HDS 1000 DE
11
4. Removal of internal deposits
If there are internal deposits in the pipe lines, the flow resistance increases with the result that the
overflow protection can switch over.
According to legal regulations, only boiler cleansing compounds which have certification marks can be
used to remove the deposits:
RM 100
6.287-008
dissolves limestone and simple compounds consisting of limestone
and detergent residues.
RM 101
6.287-013
dissolves deposits which cannot be dissolved with RM 100.
Procedure
Caution!
The gases that are given off are combustible.
Do not smoke and provide good ventilation.
– Fill a 20-litre container 3/4 full of water.
– Add one litre of boiler-cleansing compound to the 15 litres of water.
– Connect water hose direct to the pump head and hang the free end in the container.
– Connect the spray lance without nozzle and insert in the container.
– Switch unit switch to “Burner on”, until approx. 40 °C has been reached.
– Turn off unit and let it stand for 20 minutes.
– Then pump the unit until empty.
Caution: When the descaling process is in action, the handgun must always remain pressed.
– To conclude, we recommend the use of an alkaline solution (e.g. RM 81) to be pumped through the
unit via the detergent tank to provide protection against corrosion and to neutralise the acid residue.
5. Repairs
The safety valve is adjusted and sealed in the factory; it may not be changed. Checking of the overflow
valve and safety valve should be carried out only by a specialist technician.
6. High-pressure hoses
Devote special attention to the hoses. Every high-pressure hose must accord with the safety
regulations and must be marked with the maximum permitted operating pressure, the manufacturer’s
set date for usage and the manufacturer.
High-pressure hoses may not be kinked, stretched, crushed or damaged in any other way. Damaged
high-pressure hoses are in danger of bursting and must be replaced without delay.
High-pressure hoses of short service life and those which are not repaired properly are extraordinarily
dangerous. Therefore use only certificated and marked high-pressure hoses.
Kärcher original high-pressure hoses meet the safety requirements.
7. Notes on the fuel pump for the burner
Even when the unit is running in cold-water mode, it must not be allowed to operated without fuel oil or
diesel in the fuel tank, otherwise there is a danger that the fuel pump will dry-run and in consequence
the drive clutch and fuel pump will be destroyed.
Summary of Contents for HDS 1000 DE
Page 1: ...5 959 083 06 01 HDS 1000 DE...
Page 2: ......