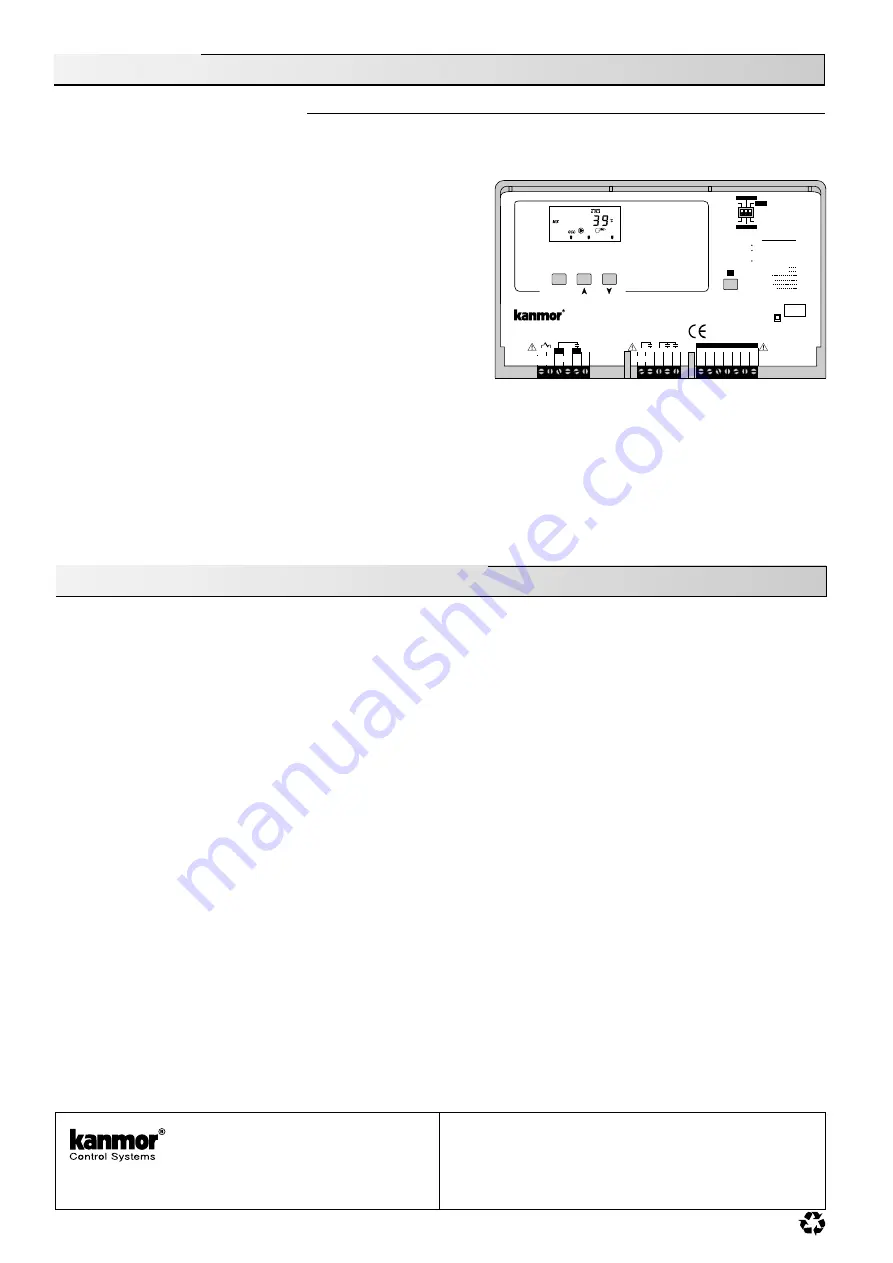
Technical Data
20 of 20
© 2003. All rights reserved.
Used under license by kanmor Control Systems Ltd.
All specifications are subject to change without notice.
Printed in Canada. D 360e - 06/03.
kanmor Control Systems Ltd.
5100 Silver Star Road
Vernon, B.C. CANADA V1B 3K4
250-545-2693 Fax. 250-549-4349
Web Site: www.kanmor.com
Limited Warranty and Product Return Procedure
Limited Warranty
The liability of kanmor Control Systems Ltd.
(“kanmor”) under this warranty is limited. The Purchaser, by taking
receipt of any kanmor product (“Product”), acknowledges the terms
of the Limited Warranty in effect at the time of such Product sale and
acknowledges that it has read and understands same.
The kanmor Limited Warranty to the Purchaser on the Products sold
hereunder is a manufacturer’s pass-through warranty which the Purchaser
is authorized to pass through to its customers. Under the Limited Warranty,
each kanmor Product is warranted against defects in workmanship and
materials if the Product is installed and used in compliance with kanmor’s
instructions, ordinary wear and tear excepted. The pass-through warranty
period is for a period of twenty-four (24) months from the production date
if the Product is not installed during that period, or twelve (12) months from
the documented date of installation if installed within twenty-four (24) months
from the production date.
The liability of kanmor under the Limited Warranty shall be limited to, at
kanmor’s sole discretion: the cost of parts and labor provided by kanmor to
repair defects in materials and/or workmanship of the defective product; or
to the exchange of the defective product for a warranty replacement product;
or to the granting of credit limited to the original cost of the defective product,
and such repair, exchange or credit shall be the sole remedy available
from kanmor, and, without limiting the foregoing in any way, kanmor is not
responsible, in contract, tort or strict product liability, for any other losses,
costs, expenses, inconveniences, or damages, whether direct, indirect,
special, secondary, incidental or consequential, arising from ownership or
use of the product, or from defects in workmanship or materials, including
any liability for fundamental breach of contract.
The pass-through Limited Warranty applies only to those defective Products
returned to kanmor during the warranty period. This Limited Warranty does not
cover the cost of the parts or labor to remove or transport the defective Product,
or to reinstall the repaired or replacement Product, all such costs and expenses
being subject to Purchaser’s agreement and warranty with its customers.
Any representations or warranties about the Products made by Purchaser
to its customers which are different from or in excess of the kanmor Limited
Warranty are the Purchaser’s sole responsibility and obligation. Purchaser
shall indemnify and hold kanmor harmless from and against any and all
claims, liabilities and damages of any kind or nature which arise out of or
are related to any such representations or warranties by Purchaser to its
customers.
The pass-through Limited Warranty does not apply if the returned Product
has been damaged by negligence by persons other than kanmor, accident,
fi re, Act of God, abuse or misuse; or has been damaged by modifi cations,
alterations or attachments made subsequent to purchase which have not
been authorized by kanmor; or if the Product was not installed in compliance
with kanmor’s instructions and/or the local codes and ordinances; or if due
to defective installation of the Product; or if the Product was not used in
compliance with kanmor’s instructions.
THIS WARRANTY IS IN LIEU OF ALL OTHER WARRANTIES, EXPRESS
OR IMPLIED, WHICH THE GOVERNING LAW ALLOWS PARTIES TO
CONTRACTUALLY EXCLUDE, INCLUDING, WITHOUT LIMITATION,
IMPLIED WARRANTIES OF MERCHANTABILITY AND FITNESS FOR
A PARTICULAR PURPOSE, DURABILITY OR DESCRIPTION OF THE
PRODUCT, ITS NON-INFRINGEMENT OF ANY RELEVANT PATENTS
OR TRADEMARKS, AND ITS COMPLIANCE WITH OR NON-VIOLATION
OF ANY APPLICABLE ENVIRONMENTAL, HEALTH OR SAFETY
LEGISLATION; THE TERM OF ANY OTHER WARRANTY NOT HEREBY
CONTRACTUALLY EXCLUDED IS LIMITED SUCH THAT IT SHALL
NOT EXTEND BEYOND TWENTY-FOUR (24) MONTHS FROM THE
PRODUCTION DATE, TO THE EXTENT THAT SUCH LIMITATION IS
ALLOWED BY THE GOVERNING LAW.
Product Warranty Return Procedure
All Products that are believed to have
defects in workmanship or materials must be returned, together with a written
description of the defect, to kanmor through its Representative. If kanmor
receives an inquiry from someone other than a kanmor Representative,
including an inquiry from Purchaser (if not a kanmor Representative) or
Purchaser’s customers, regarding a potential warranty claim, kanmor’s sole
obligation shall be to provide the address and other contact information
regarding the appropriate Representative.
Caution
The nonmetallic enclosure does not provide grounding between conduit connections. Use grounding type bushings and
jumper wires.
Mixing Control 360e
Floating Action
Literature —
D 360e, D 070e, E 021e.
Control
— Microprocessor PID control; This is not a safety (limit) control.
Packaged weight
— 2.8 lb. (1250 g), Enclosure A, blue PVC plastic
Dimensions —
6-5/8” H x 7-9/16” W x 2-13/16” D (170 x 193 x 72 mm)
Approvals
— CE approved, meets ICES & FCC regulations for EMI/RFI.
Ambient conditions
— Indoor use only, 32 to 102
°
F (0 to 39
°
C), < 90% RH non-
condensing. Altitude <2000 m, Installation Category II,
Pollution Category II.
Power supply
— 230 V ±10% 50 Hz 2300 VA
System Pump Relay — 230 V (ac) 10 A 1/3 hp, pilot duty 240 VA
Boiler Relay
— 230 V (ac) 10 A 1/3 hp, pilot duty 240 VA
Open Relay
— 230 V (ac) 10 A 1/3 hp, pilot duty 240 VA
Close Relay
— 230 V (ac) 10 A 1/3 hp, pilot duty 240 VA
Mix Demand
— 20 to 260 V (ac) 2 VA
Sensors included —
NTC thermistor, 10 k
Ω
@ 77
°
F (25
°
C ±0.2
°
C) fl=3892
Outdoor Sensor 070e and 2 of Universal Sensor 071e.
Optional devices
— kanmor type #: 032e, 070e, 071e, 076e, 079e.
Do not apply power
Signal wiring must be
rated at least 300 V.
L
N
Pmp
N
Sw
Sys
UnO Com Boil
Mix
Pwr Opn Cls
Mix Com Out Indr
1
3
5
2
4
6
9 10
7 8
11
12 13 14 15 16 17 18
Mix
Power
Boiler
Demand
Advanced
Installer
Boiler Sensor
Supply
30% Enable
10% Enable
Return
Item
Test
Terminal
Unit
Mixing
Demand
INSTALLATION CATEGORY II
Made in Canada
Power:
230 V
±
10% 50 Hz 2300 VA
Relays:
230 V (ac) 10 A 1/3 hp, pilot duty 240 VA
Demand: 20 to 260 V (ac) 2 VA
H1
21
1B
To increase or decrease the
building temperature:
• Press the
Item
,
▲
,
▼
buttons
simultaneously for 1 sec. to
enter the ADJUST menu
• Use the
▲
,
▼
buttons to adjust
the
ROOM
setting
Display defaults back to VIEW
menu after 20 seconds.
ROOM
-
Set to desired room temperature.
OUTDR DSGN
-
Set to coldest (design)
outdoor temperature.
Terminal Unit
Set to
High Mass Radiant
1
Low Mass Radiant
2
Fan Coil
3
Convector
4
Radiator
5
Baseboard 6
Refer to brochure for more information.
Installer Instructions
Mixing Control 360e
Floating Action
Open
Motor
Speed
Close