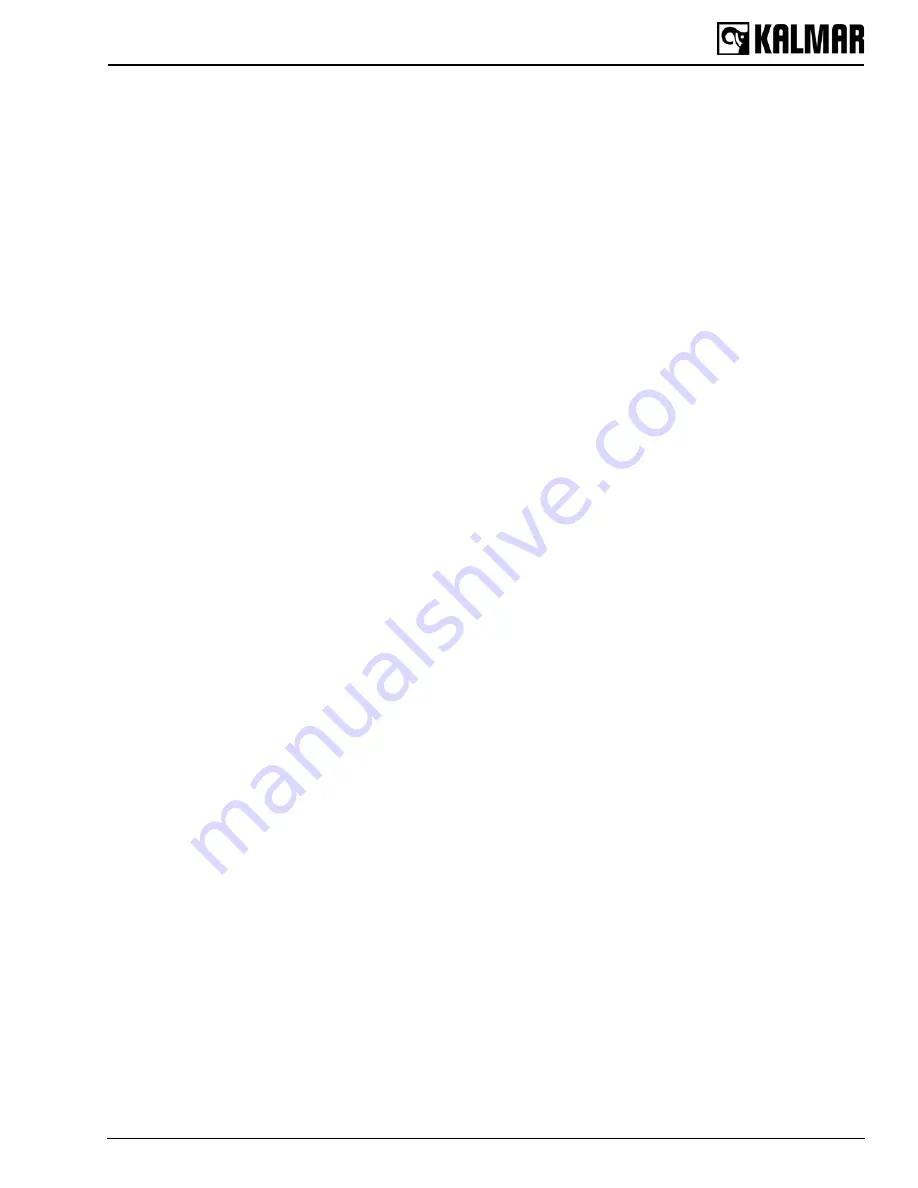
1 Introduction
7
4.
Inspect latch
for proper operation by inserting into buckle.
Latch must insert smoothly and you must hear an audible
click. Verify proper latching by tugging on belt. Latch must
not be worn, deformed or corroded.
Replace the entire belt
system.
5.
Inspect shoulder loop web guide (optional component)
Seat belt must move freely through shoulder loop.
Shoulder loop must also pivot freely and be free of
obstructions.
If necessary, adjust shoulder loop hardware
and/or remove obstruction.
6.
Inspect seat belt height adjuster
(optional component)
for damage. Mover adjuster up and down. It must move
freely and lock at the different height positions.
Replace the
entire belt system if necessary.
7.
Inspect retractor operation.
When pulled and released
slowly, seat belt must spool out and retract without locking.
Replace the entire belt system if necessary.
8.
Inspect mounting hardware
on both sides of seat.
Hardware should be tight. Hardware must not be missing,
rusted, corroded or damaged.
If necessary, replace
defective or missing hardware with authorized parts and/or
tighten hardware.
9.
Inspect tethers
for cuts, fraying, extreme or unusual wear.
Tethers must also be inspected for proper attachment and/
or adjustment.
If necessary, replace defective tethers.
Tighten and/or properly adjust tethers according to the
Seat Adjustment section on page 17.
10.
Inspect Komfort Latch
®
(optional component)
for function
and ability to clamp on web.
Replace the entire system if
necessary.
Cleaning of Seat Belt Fabric
— Sponge the seat belt clean
with mild soap and water. DO NOT use bleach, dye or
household detergents.
Electrical
Horn
— Operate the steering wheel-mounted horn to check
operation. (Check optional air horns if equipped.)
Instruments
— Check operation of all instruments and
gauges.
Lights
— Check to make sure all lights (interior, exterior,
headlights, etc.) function properly. Make sure the gauge and
dash backlighting is working properly.
Wiring
— Check to ensure all wiring is properly secured and
protected. Replace worn, cracked or chafed wires and looms.
Make sure factory wiring has not been compromised by
improper splicing or modifications.